Products Used in Raleigh Cycle Manufacturing:
- Sifbronze No. 1 Welding Rods: Employed in the high-speed welding of cycle frames, offering strength and durability in frame assembly.
- Sifsteel No. 11 Filler Wires: These are used for the fusion welding of intricate parts such as handlebars and tricycle frames, ensuring strong and reliable joints.
- Sifbronze and Copper Brazing Techniques: Essential for assembling various cycle components with precision and efficiency.
Based in Nottingham, England, Raleigh Industries emerged as the world’s largest cycle manufacturing factory, producing over one million bicycles annually by the mid-20th century. As a leader in bicycle innovation, Raleigh embraced advanced welding and brazing techniques to maintain their position at the forefront of the industry, with Sifbronze products playing a key role in the production process.
In the highly competitive bicycle manufacturing sector, fusion welding, bronze welding, and brazing were critical in meeting the industry’s demand for both quality and performance. Raleigh’s commitment to innovation was evident through its constant experimentation with new methods, many of which were driven by necessity and practical experience.
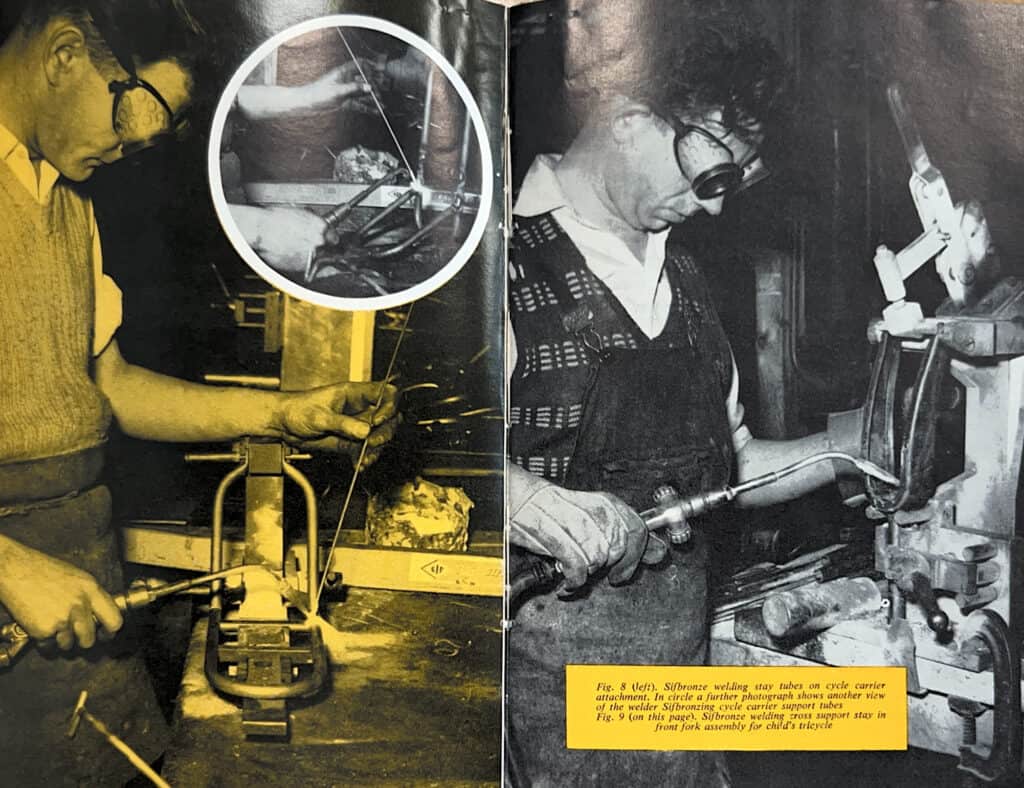
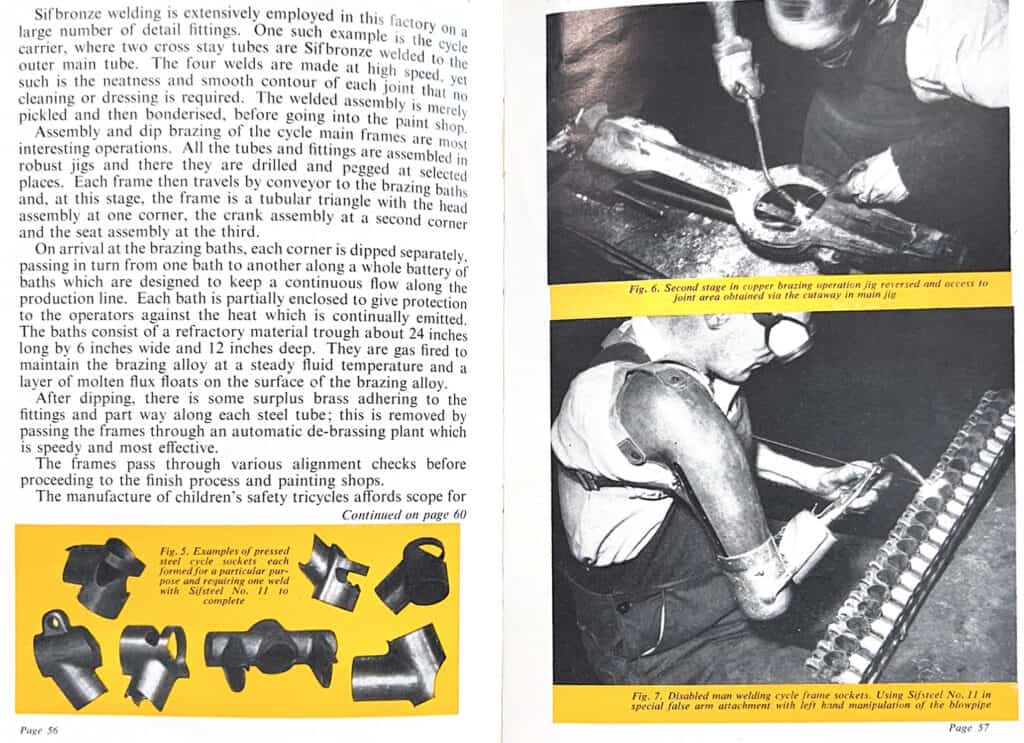
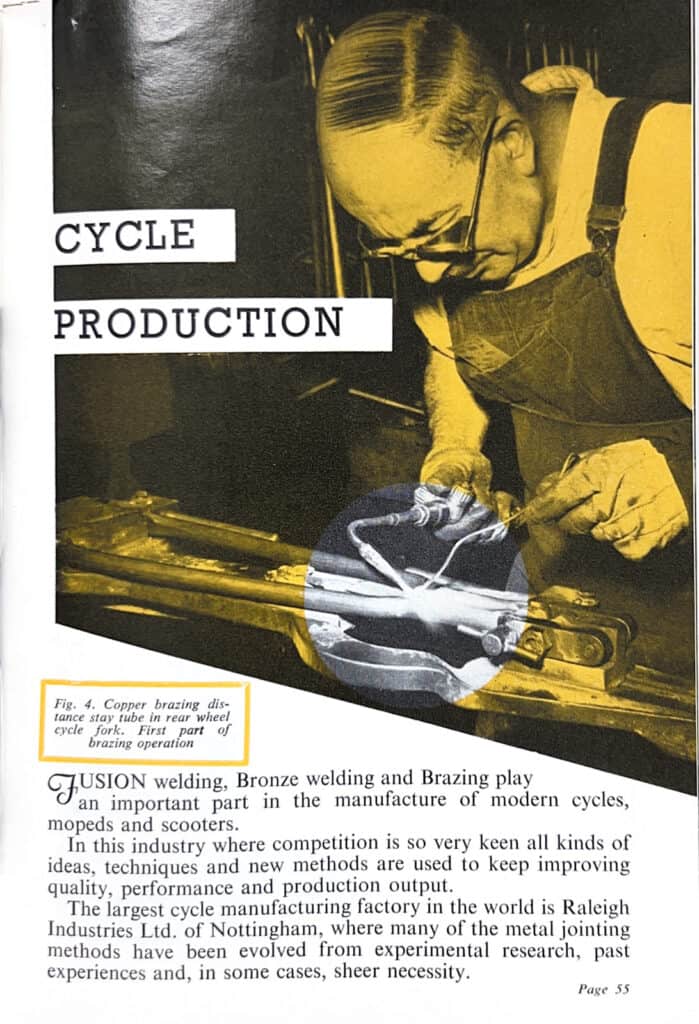
At the core of Raleigh’s success was using Sifbronze No. 1 rods in welding cycle frames. These welding rods provided the strength and flexibility needed for assembling durable cycle parts, particularly in high-stress areas like the cycle carrier. With Sifbronze, Raleigh welders made precise, high-speed welds that required minimal cleaning or dressing, allowing for efficient production without sacrificing quality. The welded assemblies were bonded and painted, with Raleigh bikes renowned for their sleek, smooth finish.
Copper brazing techniques, which were used extensively in the factory, further enhanced the production process. Frames were submerged into brazing baths, allowing molten brazing alloy to bond the metal parts together. The resulting frames were passed through a de-brassing plant, quickly and effectively removing surplus brass. This process ensured that each frame was securely bonded and aesthetically polished, ready for painting and assembly.
One of Raleigh’s standout products was the Raleigh Sports Model, a high-performance cycle on which extensive Sifbronze welding was carried out. The frames are made lighter and stronger through careful welding and brazing processes, which sets the cycling durability and speed standard.
In addition to adult bicycles, Raleigh produced a wide range of children’s cycles, including the popular Sunbeam Winkie and Tiny Toddler tricycles. These models utilized Sifsteel No. 11 filler wires for fusion welding, allowing rapid and accurate assembly. Two welders working together could complete up to 1,800 pairs of handlebars per week, an extraordinary output made possible by the precision and reliability of Sifbronze and Sifsteel welding consumables.
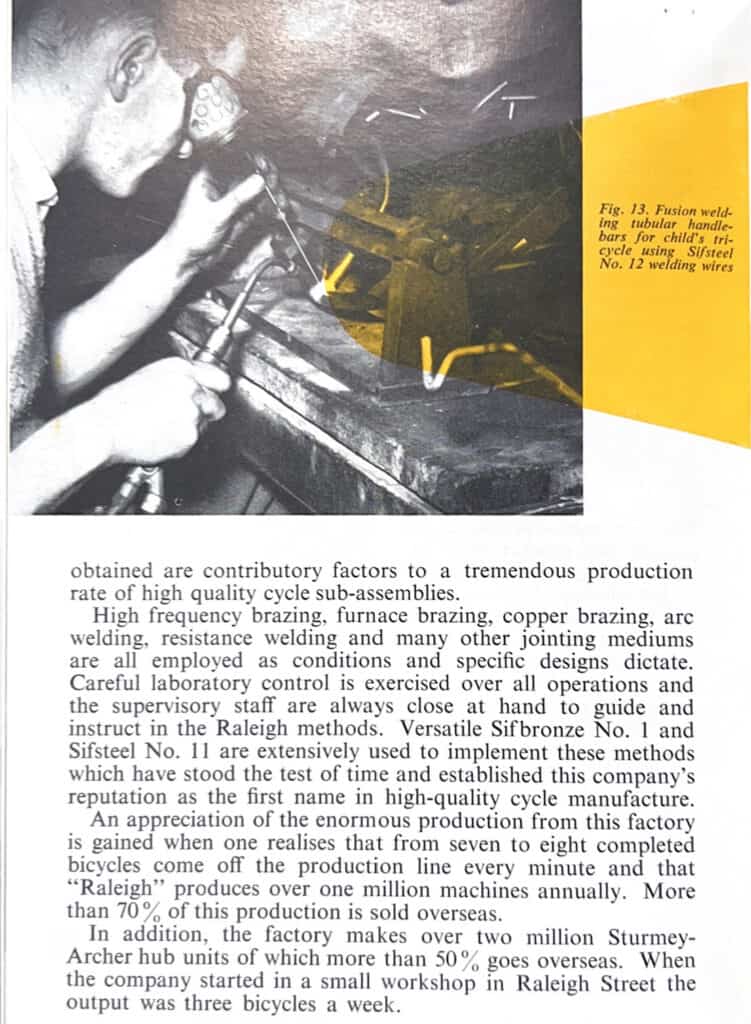
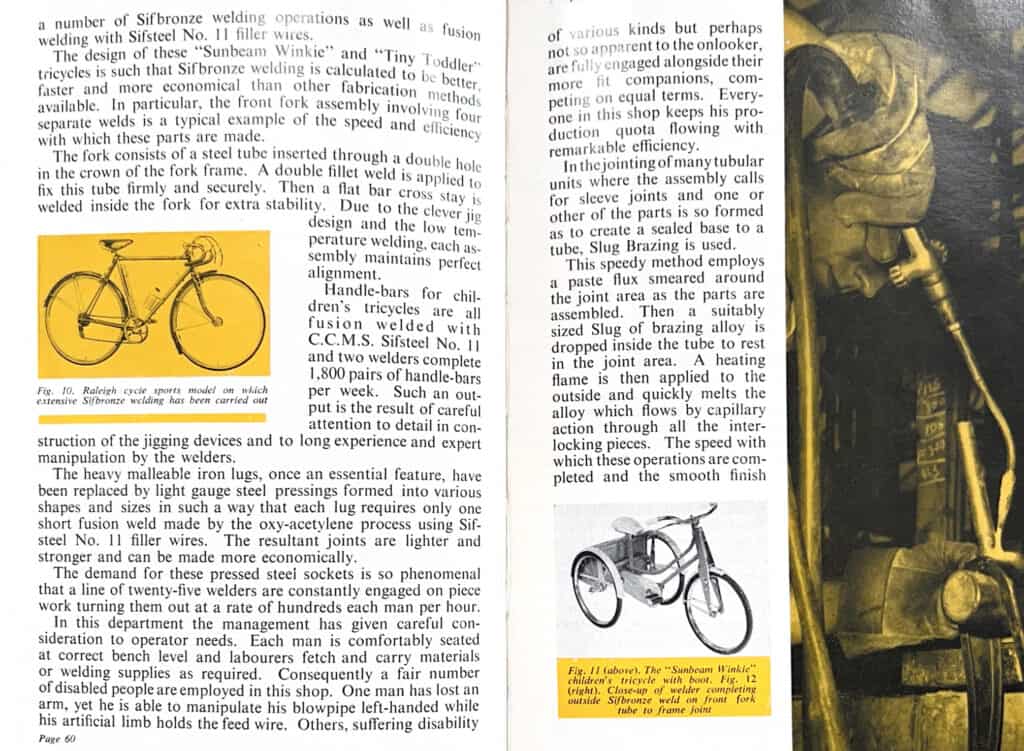
Raleigh’s ability to mass-produce cycles efficiently without compromising on quality was further supported by its use of automatic de-brassing plants and high-frequency brazing. These processes allowed Raleigh to maintain a continuous production flow while ensuring that each cycle was built to the highest standards. By the 1950s, Raleigh’s factory could produce seven to eight completed bicycles every minute, a testament to the innovation and dedication that characterised the company’s approach.
As Raleigh expanded its operations, the company became a household name in the UK and gained a significant international presence. With more than 70% of production sold overseas, Raleigh Cycles became synonymous with quality and performance across the globe. The company’s use of Sifbronze welding rods and Sifsteel filler wires was vital to maintaining this reputation, ensuring that every bicycle that rolled off the production line met the high standards that Raleigh was known for.
Through their innovative use of Sifbronze and Sifsteel welding products, Raleigh Industries produced millions of affordable and reliable bicycles. Their commitment to quality and the latest welding techniques helped them dominate the global cycling market for decades, cementing Raleigh’s legacy as one of the most influential cycle manufacturers in history.