Products Used in London Transport Bus Maintenance:
- Sifbronze No. 1 Welding Rods: Utilized in repairing and reinforcing bus components, ensuring strength and longevity in essential parts like suspension and exhausts.
- Sifsteel No. 11 Filler Wires: Used in fusion welding of intricate parts, allowing for precise repairs of cross members and other vital components.
- Brazing Techniques: Employed in rebuilding worn parts and extending the service life of bus components, maintaining London Transport’s fleet.
London Transport has long been celebrated for operating one of the world’s largest and most efficient public bus systems. At the heart of this achievement lies the iconic red buses and behind-the-scenes efforts to keep the fleet running smoothly. With nearly 8,000 buses in operation by the mid-20th century, the repair and maintenance of London’s buses were critical to the city’s transport infrastructure. Enter Sifbronze products, which played a crucial role in ensuring these vehicles remained in top condition, allowing London Transport to deliver reliable services to millions of passengers daily.
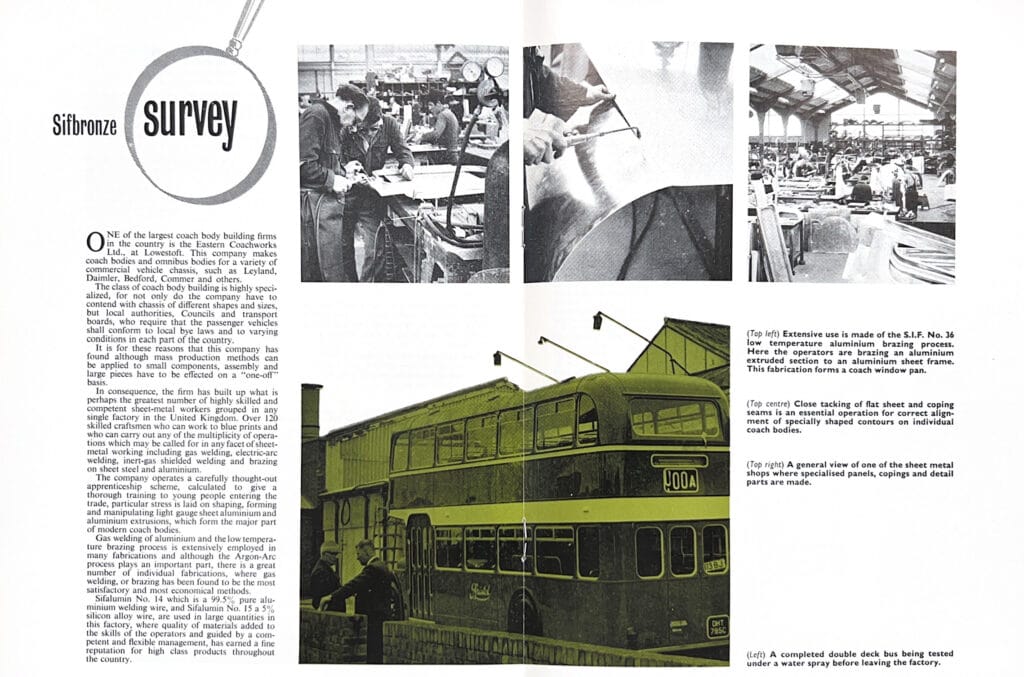
The sprawling London Transport network required a sophisticated approach to vehicle upkeep, with multiple garages dedicated to ensuring that buses stayed on the road. The Aldenham Bus Works and Chiswick Bus Works were two of the most prominent repair centres in the capital. These facilities overhauled buses, from routine repairs to large-scale component replacements.
At Chiswick Bus Works, Sifbronze No. 1 welding rods were integral in repairing worn bus parts. High-stress areas such as suspension systems and exhaust cross members often required significant welding work to restore them to “as new” condition. Worn suspension plates were built up using Sifbronze rods, which provided the necessary strength and durability to withstand the continuous strain of London’s bustling streets. Skilled welders employed advanced brazing techniques to fuse new metal to old parts, extending the life of bus components far beyond their original design.
In addition to suspension repairs, using Sifsteel No. 11 filler wires was crucial in the precise fusion welding of smaller, intricate bus parts. Welders used these filler wires to restore and reinforce exhaust cross members and other high-wear components. These parts were subject to immense heat and pressure during the buses’ operation, and Sifsteel’s precision ensured that repairs were reliable and long-lasting.
A significant part of London Transport’s repair philosophy revolved around reusing and rebuilding existing parts rather than replacing them with new ones. This approach saved costs and allowed the buses to return to service faster. Welders at Chiswick were trained to identify worn but serviceable components, which could be rebuilt using brazing and welding techniques. This recycling of parts was essential for maintaining the vast fleet while keeping repair costs manageable.
At Aldenham Bus Works, the scale of operations was even more impressive. Capable of overhauling up to 50 buses each week, Aldenham was an essential cog in the London Transport machine. Buses would enter Aldenham for complete overhauls, with every aspect of the vehicle inspected, repaired, or replaced as necessary. Sifbronze welding and brazing products were indispensable in this process, helping keep London’s fleet on the road for many years.
One key focus of the overhaul process at Aldenham was the careful restoration of the chassis and engine components. The buses would first be dismantled to their bare chassis, and the individual parts were assessed. Components that required further work would be sent to the welding shop, where skilled technicians used Sifbronze products to bring them back to their former glory. Brazing techniques were instrumental in repairing aluminium and iron parts, allowing the welders to fuse metals and ensure the strength of critical components.
While welding and repair played a crucial role in London’s bus maintenance, attention was also paid to safety and efficiency. The Aldenham and Chiswick work employed a system of colour coding and rigorous inspections to determine the level of repair required for each bus. This method allowed London Transport to manage its massive workload while ensuring that no bus returned to the road without being thoroughly checked and repaired.
The Sifbronze legacy in London Transport’s bus network is a testament to the strength and durability of these welding products. By using Sifbronze No. 1 welding rods and Sifsteel No. 11 filler wires, London’s bus system continued operating efficiently, even in the face of growing demand and wear. The role of these welding products in maintaining the fleet cannot be overstated, as they helped extend the life of the buses, keeping them running on the streets of London for decades.
By the time London’s transport system peaked in the mid-20th century, the combination of advanced repair techniques and reliable materials like Sifbronze ensured that buses could handle the rigours of daily operation in one of the world’s busiest cities. Sifbronze products supported London Transport’s commitment to quality service and helped maintain the heritage and legacy of the city’s famous red buses.
Through the use of innovative welding and brazing techniques, supported by products from Sifbronze, London Transport set the standard for bus repair and maintenance. Their approach ensured that buses remained reliable, cost-effective, and able to meet the growing needs of the city’s population for decades to come.

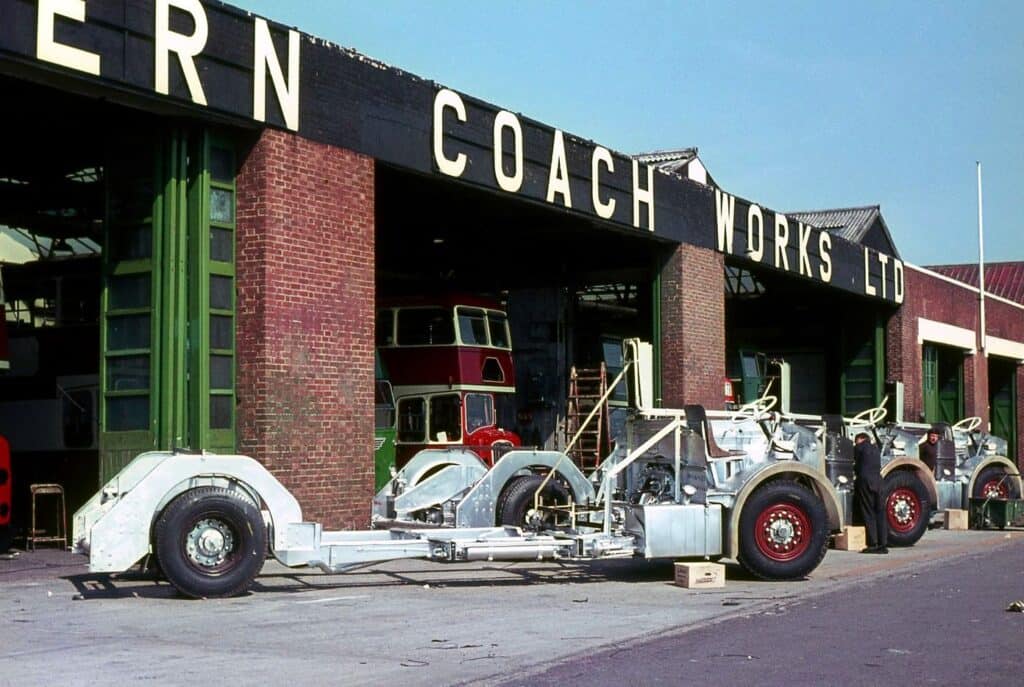
- References –
- Eastern coachworks ECW Lowestoft factory remembered – https://www.youtube.com/watch?v=N2MnJrguA6U
- Logo – Eastern Coach Works logo. | I’ve had one of these ECW logo’s… | Flickr
- Eastern Coachworks Ltd – Pin page (pinterest.com)
- Eastern Coachworks badge – CYU8020 ECW | Eastern Coach Works Ltd badge inside the Brist… | Flickr
- Eastern Coach Works Pictorial Tribute – Eastern Coach Works (pinterest.com)
- Article Links –
- Eastern Coach Works – Wikipedia