Products Used in the Jaguar D-Type Fabrication:
- Sifbronze No. 1 Rods: These rods were employed for welding high-strength joints in the steel tubular chassis and provided both precision and durability.
- Reynolds 531 Steel Tubes: Lightweight yet incredibly strong, these steel tubes formed the structural backbone of the D-Type’s chassis.
- Test Rig Apparatus: Specialized equipment ensured the welded chassis components’ precision and alignment, minimising any distortion risk.
In the high-octane world of motorsport, success is driven by innovation, precision, and advanced materials. One of the standout examples of this is the Jaguar D-Type, a car that left its mark on racing history. At the core of its success was the advanced Sifbronze welding process, which played a pivotal role in fabricating its steel tubular chassis.
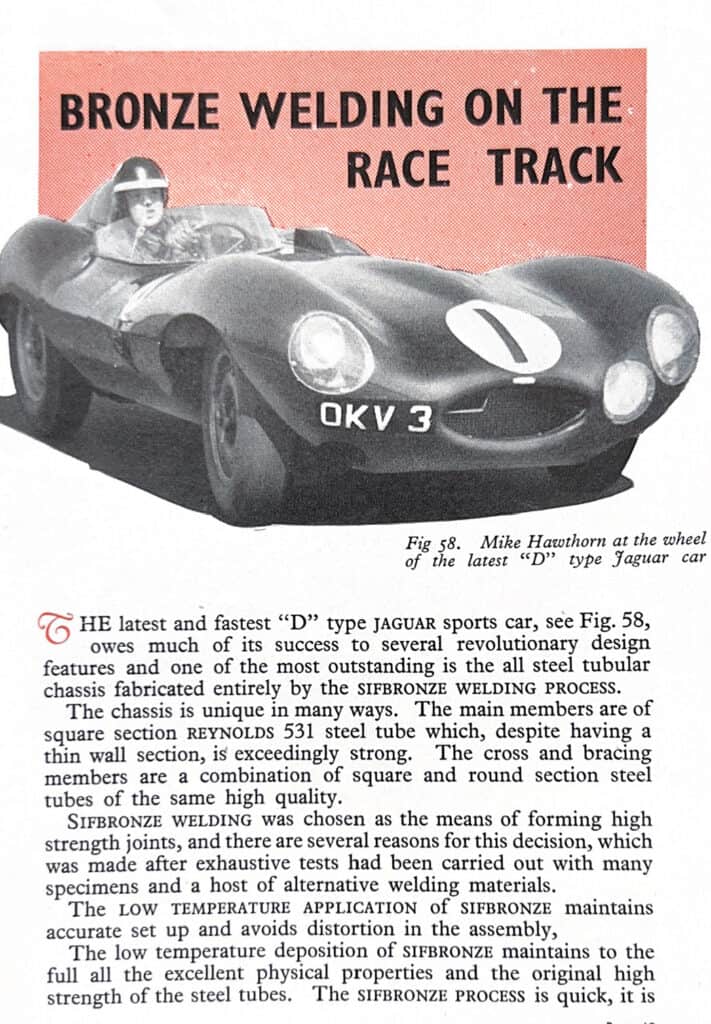
The Chassis: Strength and Precision
The Jaguar D-Type’s tubular chassis was crafted from Reynolds 531 steel tubes, chosen for their remarkable strength-to-weight ratio. Despite being thin-walled, these tubes provided the necessary durability for the rigours of high-speed racing. The chassis design incorporated square and round section tubes to enhance flexibility and support.
What set the D-Type apart was the use of Sifbronze No. 1 welding rods to form the high-strength joints throughout the chassis. Sifbronze welding was selected for its ability to create precise, distortion-free welds that maintained the steel’s inherent strength. The low-temperature application of Sifbronze minimized the risk of weakening the material or causing misalignment during the assembly process. As a result, the chassis was both lightweight—at under 60 lbs—and incredibly strong.
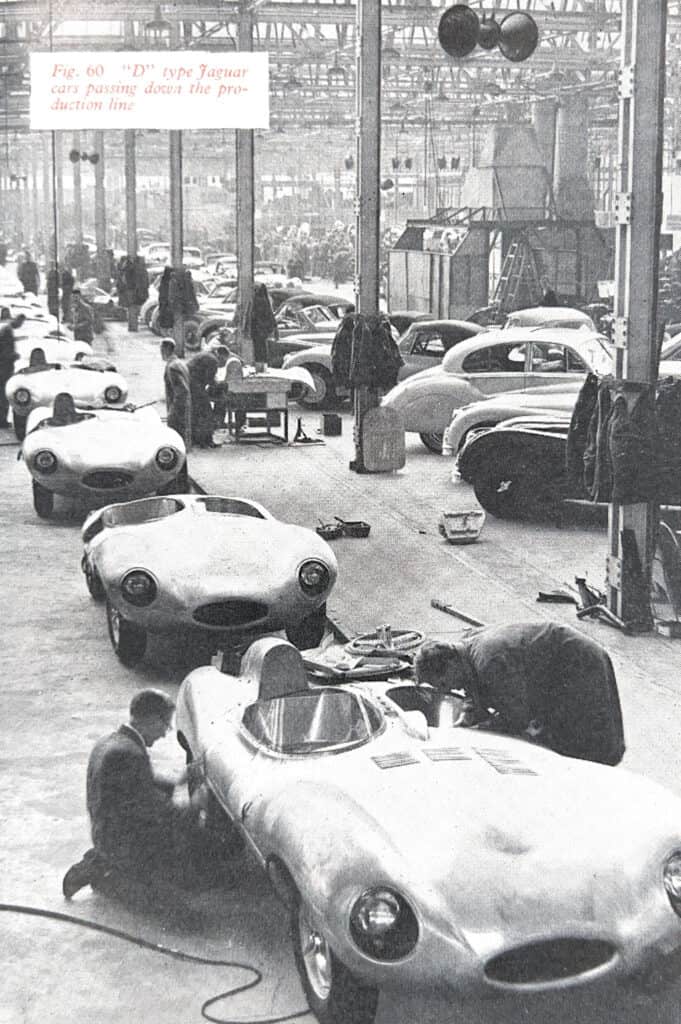
Why Sifbronze?
Sifbronze welding was crucial to this process due to several key benefits. First, the welding rods provided a high degree of control over the welds, ensuring accuracy and maintaining the integrity of the Reynolds 531 steel tubes. Second, the low-temperature application prevented any distortion that could affect the car’s aerodynamics and performance on the track.
Additionally, the chassis underwent rigorous testing using specialized test rig apparatus to ensure that the joints were flawless, and the frame was aligned with exacting standards. This allowed the D-Type to achieve its lightweight structure while retaining the strength to dominate in races like the 24 Hours of Le Mans.
Performance on the Track
The strength and precision of the Jaguar D-Type’s chassis, made possible by using Sifbronze welding, played a pivotal role in its on-track performance. The car’s lightweight frame allowed for better speed and manoeuvrability, and its strong joints ensured durability even under the harsh conditions of endurance racing. Drivers like Mike Hawthorn pushed the D-Type to its limits, relying on the impeccable engineering behind the vehicle’s design.
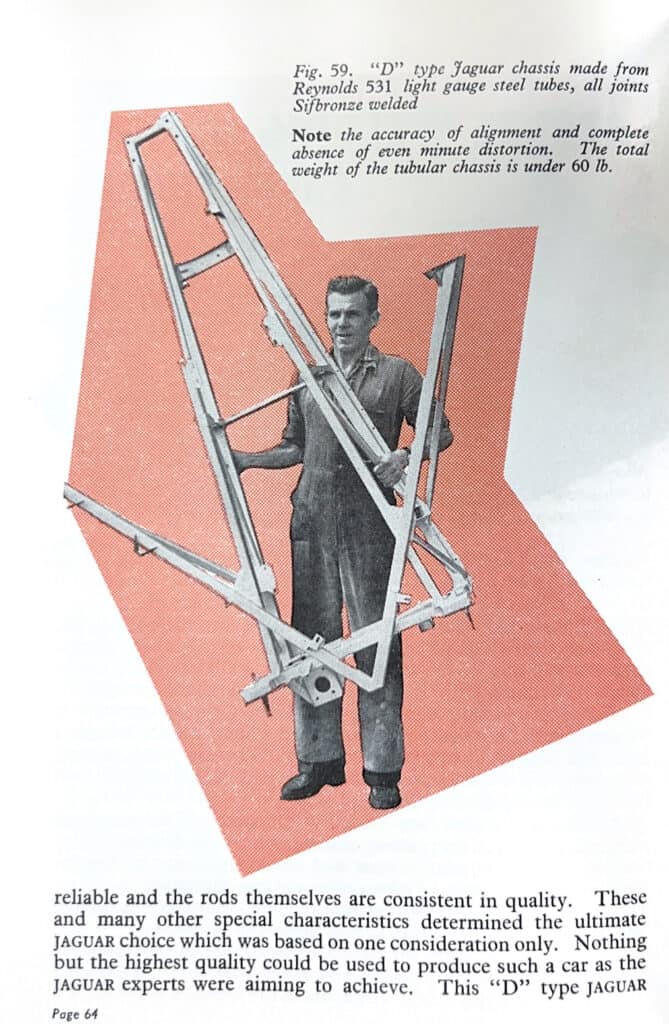
A Lasting Legacy
The collaboration between Reynolds Steel and Sifbronze Welding produced more than just a racing car; it created a legend. The Jaguar D-Type’s triumphs on the track testify to the importance of using high-quality materials and welding techniques to push the possible boundaries. Today, the D-Type remains a symbol of innovation in motorsport, with its legacy cemented in the annals of racing history, thanks in no small part to the power of Sifbronze.
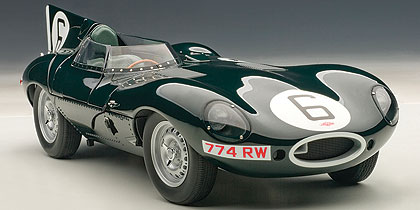