Products Used in Car Body Fabrication:
- Sifbronze Fluxcoated Rods: These are essential for welding joints in critical car body assemblies, ensuring strength, rigidity, and weatherproofing.
- Pressed Steel Body Panels: Manufactured for various car models, such as the Jowett Javelin and Bradford Van, these panels form the core structure of the vehicles.
- Special Jigs and Assembly Tools: These are used to position panels precisely during welding, minimize distortion, and ensure optimal alignment for the car body structure.
Over the years, Sifbronze welding has played an integral role in automotive manufacturing, particularly in constructing pressed steel motor bodies. This innovative welding process has not only ensured the structural integrity of vehicles but also contributed to weatherproofing and durability—crucial for cars that face the full force of the elements on the road.
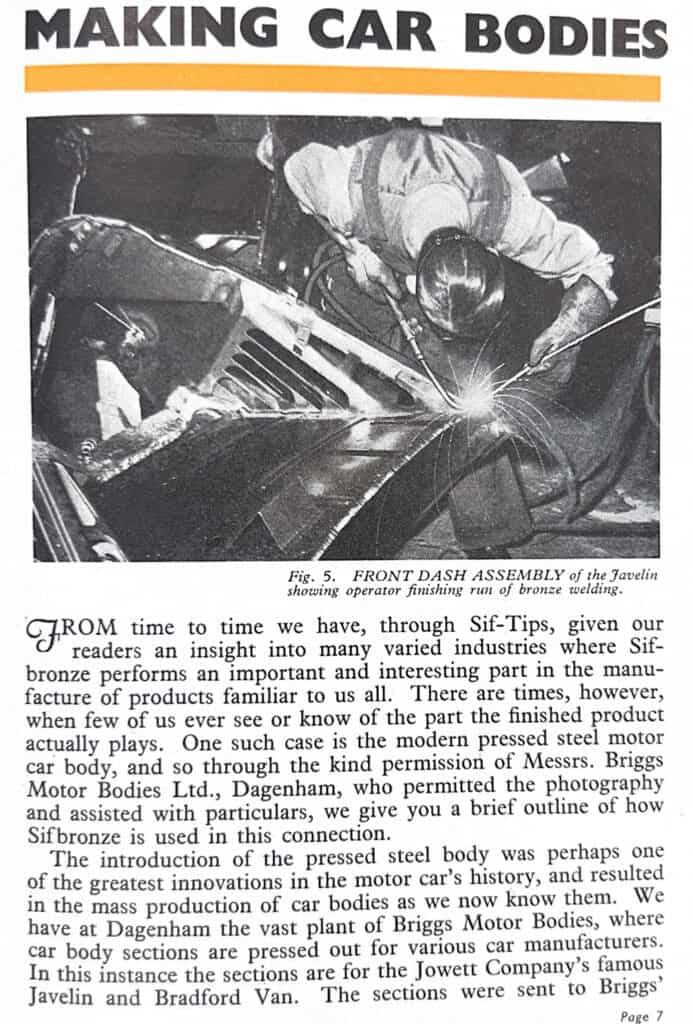
Revolutionizing Car Body Production
At factories like Briggs Motor Bodies Ltd. in Dagenham, producing pressed steel bodies for vehicles revolutionized mass production in the automotive industry. These steel body sections, created for models such as the Jowett Javelin and Bradford Van, were designed to be both lightweight and strong. The challenge was to join these sections seamlessly while maintaining their structural integrity and resisting weather-related wear over time.
This is where Sifbronze welding came into play. Using Sifbronze Fluxcoated Rods, skilled operators were able to weld critical joints along the car’s body sections. This low-temperature process was ideal for preventing distortion and avoiding scaling or burn marks on the panels—issues that could compromise both the vehicle’s appearance and functionality.
The Front Dash Assembly
A notable application of this method was in the front dash assembly of the Jowett Javelin, one of the more popular models of the time. The assembly consisted of several key components: the toe board, the top dash panel, and two side dash panels. These sections were initially spot-welded in specially designed jigs to hold them in place. After positioning, the edges where the sections met were cleaned to ensure the smooth and consistent flow of Sifbronze during welding.
The welding process focused on the joint edges of the top and side dash panels. This precise welding strengthened the assembly and acted as a critical weather excluder, keeping rain, dust, and other elements out. This was crucial for improving the car’s longevity and reliability, particularly in harsh weather conditions.
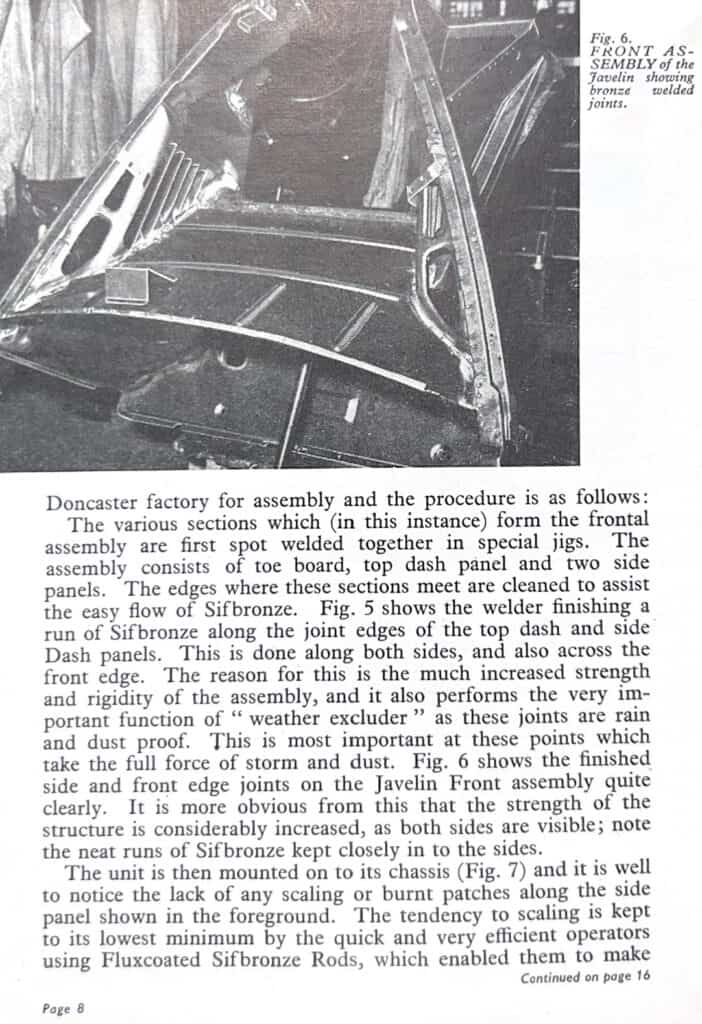
Strengthening the Vehicle’s Structure
As shown in the accompanying images, the Sifbronze welding process resulted in joints that were exceptionally strong and uniform. These joints provided rigidity to the front dash assembly and significantly increased the overall strength of the car body. These joints were functional and visually neat, with the Sifbronze welds forming clean, tight lines that helped keep the body secure.
Once the welding was complete, the unit was mounted onto the chassis. Thanks to the use of Fluxcoated Sifbronze Rods and efficient welding techniques, operators avoided scaling or burn patches along the panels, preserving the car body’s structural and aesthetic quality.
The Legacy of Sifbronze in Car Manufacturing
The role of Sifbronze in car body fabrication is a testament to the importance of reliable, high-quality welding techniques in the automotive industry. From enhancing the strength and durability of vehicles to ensuring that they remained weatherproof, Sifbronze welding helped pave the way for advancements in car manufacturing. The innovation seen in models like the Jowett Javelin and Bradford Van reminds us that the quality of a vehicle depends as much on the hidden craftsmanship as it does on the visible design.