Over the years, the art of welding has played an essential role in the evolution of motorsport, particularly in the fabrication of high-performance racing cars. The Lotus Racing Car, a vehicle synonymous with speed and agility, relied heavily on the precision and strength of all-welded construction. With over 140 welded joints, the car’s chassis was a product of meticulous design and expert welding techniques, ensuring it could withstand the demands of high-speed racing.
Revolutionizing Racing Car Fabrication
The Progress Chassis Co. in Hornsey was at the forefront of producing the Lotus Racing Car, showcasing innovative welding and chassis assembly methods. The all-welded structure comprised a prefabricated side frame and base frame, built using a mix of rectangular and round steel sections. The precise alignment of these sections during the fabrication process was critical to ensuring the car’s structural integrity.
One key challenge was ensuring that each joint could withstand the stress and vibration experienced at high speeds while also maintaining the lightness and flexibility that gave the Lotus its competitive edge. The careful welding techniques applied during this stage were vital to achieving these goals, allowing the car to perform exceptionally well on the track.
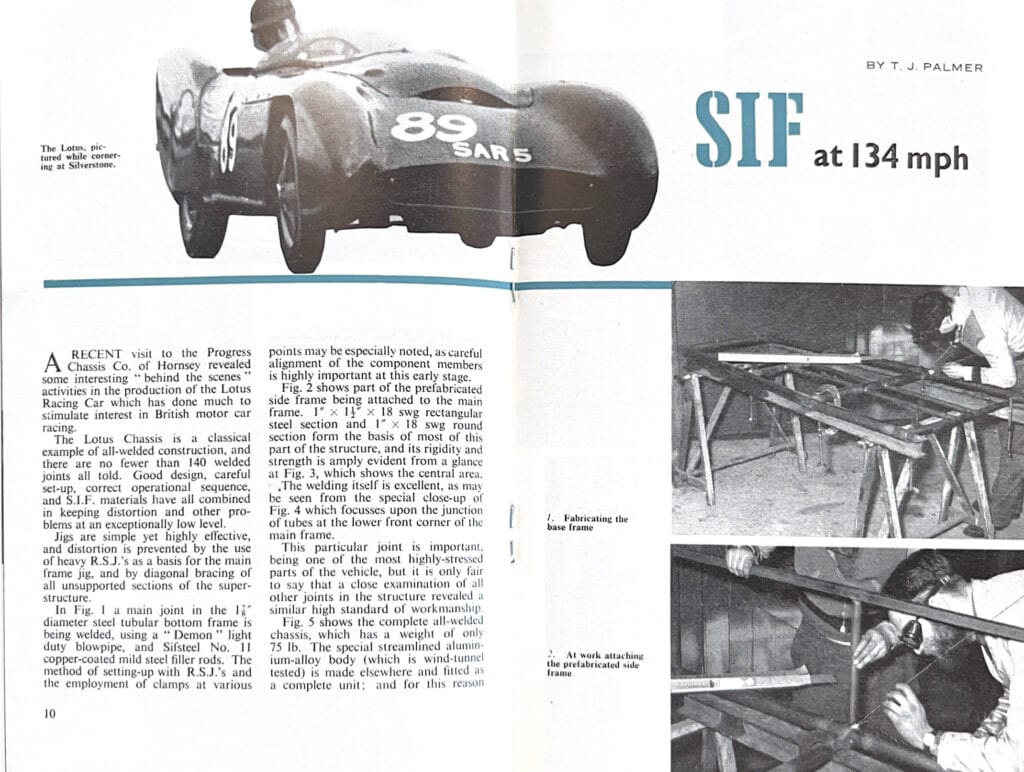
Precision Welding for Critical Joints
At the heart of the Lotus chassis was a 1½-inch diameter steel tubular bottom frame, joined with precision using expert welding methods. The frame jig, a crucial tool in the construction process, held the steel sections in place, ensuring the perfect alignment needed for a strong and lightweight structure. The welds were performed using techniques that minimized distortion, keeping the joints smooth and consistent, even under the intense demands of racing.
As the welding progressed, the focus shifted to the finer details, such as critical corner joints that connected the base and side frames. These points were not only among the most highly stressed areas of the vehicle but were also crucial to the overall strength and rigidity of the car. Creating clean, solid welds in these critical areas was essential for the car’s safety and performance at high speeds.
The Legacy of Sifbronze in Racing Car Manufacturing
The precision welding techniques used in the production of the Lotus Racing Car are a testament to the importance of expert craftsmanship in motorsport. The vehicle’s strength, flexibility, and performance can be directly traced back to the quality of its welded joints, a key factor in its ability to reach speeds of 134 mph on the racetrack. As with other iconic racing vehicles, the Lotus Racing Car’s success depended not just on its design but on the hidden skill and precision that went into every weld.
The legacy of these welding innovations continues to influence the construction of high-performance vehicles today, where the balance between strength and weight remains a critical challenge. Thanks to advances in welding techniques, exemplified by the Lotus Racing Car, the motorsport industry has continued to push the boundaries of speed, safety, and performance.