Introduction
In the high-octane world of racing, where every fraction of a second counts, the pursuit of speed and performance is relentless. From racing cars and motor cycles to lightweight pedal cycles, breaking world speed records is a testament to the precision and innovation behind these machines. At the heart of this innovation is the Reynolds Tube Company Ltd., renowned for their world-famous Reynolds “531” tubing. This case study explores how their collaboration with Suffolk Iron Foundry (SIF) and the use of Sifbronze welding techniques have driven them to new heights, setting records and advancing the technology of modern transport.
The Challenge: Creating High-Performance Frames
Year after year, new world speed records are set by vehicles built with Reynolds “531” tubing, only to be broken again by better designs and higher performance standards. This tubing is celebrated for its high strength and low weight, making it ideal for the frames and chassis of racing vehicles. However, achieving such high standards of performance required equally advanced manufacturing techniques, particularly in welding.
Reynolds Tube Company Ltd.: The Pursuit of Perfection
Located at Hay Hall, Tyseley, Birmingham, Reynolds Tube Company Ltd. has been a cornerstone in the development of modern transport. Their “531” tubing is a staple in the construction of frames for racing cars, motorcycles, and pedal cycles. The challenge lay in welding this high-quality steel tubing without compromising its inherent properties. This is where SIF and their Sifbronze welding techniques became indispensable.
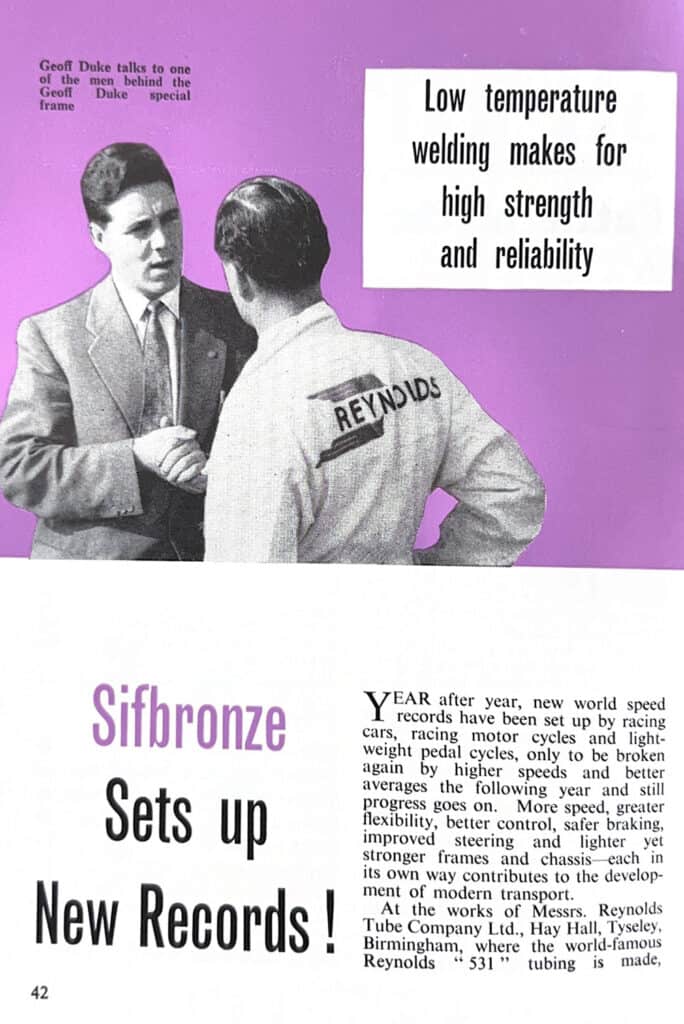
SIF’s Contribution to Excellence
Suffolk Iron Foundry (SIF) brought their expertise in low-temperature welding to the table, ensuring that the welding process did not adversely affect the high strength and special physical properties of the “531” tubing.
- Low-Temperature Welding:
- Sifbronze welding employs a filler metal with a minimum tensile strength of 28 T.P.S.I. The application temperature of Sifbronze, ranging from 850 to 900 degrees Celsius, is significantly lower than traditional fusion welding temperatures. This low-temperature application preserves the tubing’s strength and prevents brittleness or reduction in strength adjacent to the joints.
- Enhanced Strength and Reliability:
- The joints made with Sifbronze filler metal are bonded to the tube surfaces through intergranular penetration, ensuring high strength and durability. Under destructive testing, fractures invariably occur away from the joint area, retaining about 90% of the unwelded tube’s strength.
- Precision in Alignment:
- The low temperature application also minimizes distortion, allowing for perfect set-up and alignment. This precision is critical in high-performance structures where alignment is paramount to overall performance and safety.
Historical Impact: Advancing Modern Transport
The collaboration between Reynolds Tube Company Ltd. and SIF has had a profound impact on the development of modern transport. The use of Sifbronze welding allowed Reynolds to produce lighter yet stronger frames and chassis, contributing to significant improvements in speed, flexibility, control, and safety.
At the works of Reynolds Tube Company, the application of Sifbronze welding was evident in the production of frames for some of the most popular motor cycles in the world. Figures 1 and 2 from historical records show the intricate welding of these frames, highlighting the precision and care involved. The nearness of Sifbronze fillet welding is showcased in close-up images, demonstrating the clean and strong joints essential for high-speed racing.
Setting Records and Looking Forward
Thanks to this partnership, Reynolds Tube Company continued to set new world speed records. The frames and chassis produced with Sifbronze welding were lighter, stronger, and more reliable, pushing the boundaries of what was possible in racing technology. Production batches of Sifbronze welded “Douglas Earl” forks further underscored the scale and efficiency of this collaboration.
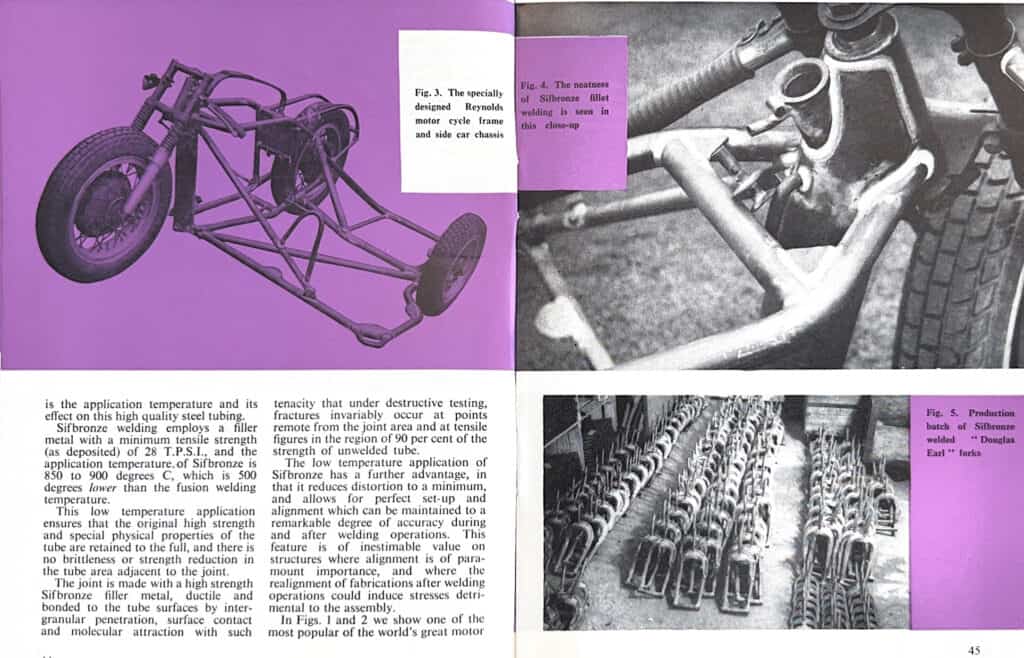
Conclusion
The story of Reynolds Tube Company Ltd. and Suffolk Iron Foundry is one of innovation, precision, and relentless pursuit of excellence. The integration of Sifbronze welding techniques into the manufacturing process of Reynolds’ “531” tubing frames has not only set new records but also advanced the technology of modern transport.
This historical case study celebrates the synergy between two pioneering companies whose dedication to quality and performance has left an indelible mark on the racing world. Through their collaboration, Reynolds and SIF have shown that with the right materials and techniques, the limits of speed and performance can always be pushed further.