Introduction
In the mid-20th century, as nations around the world rapidly expanded their electrical grids, the demand for innovative solutions in power distribution soared. Among the leading firms at the forefront of this revolution was R. A. Revell & Co. of Hebburn, County Durham. Known for their expertise in the electrical switchgear field, they faced the challenge of fabricating robust and reliable aluminium tubular busbars for the ever-growing electrical infrastructure. This case study explores how the Suffolk Iron Foundry (SIF) supported this endeavor, enhancing the fabrication process with their advanced welding technology.
The Challenge
The expansion of the electrical supply industry necessitated the establishment of numerous switching and transformer stations. These stations were critical for breaking down high power to manageable levels for local distribution. Central to this infrastructure were aluminium tubular busbars, designed to carry electrical power efficiently across long distances. R. A. Revell & Co. was tasked with fabricating these busbars, which involved welding 5½ inch diameter aluminium tubes with wall thicknesses of ⅛ inch, specified to British Standards (B.S. 2898).
The fabrication process required welding these tubes into lengths of up to 47 feet, with some busbars needing to be welded into crossover lengths of 51 feet. Given the immense strain imposed on these busbars when suspended at heights of 50 feet or more, ensuring the integrity of each weld was paramount.
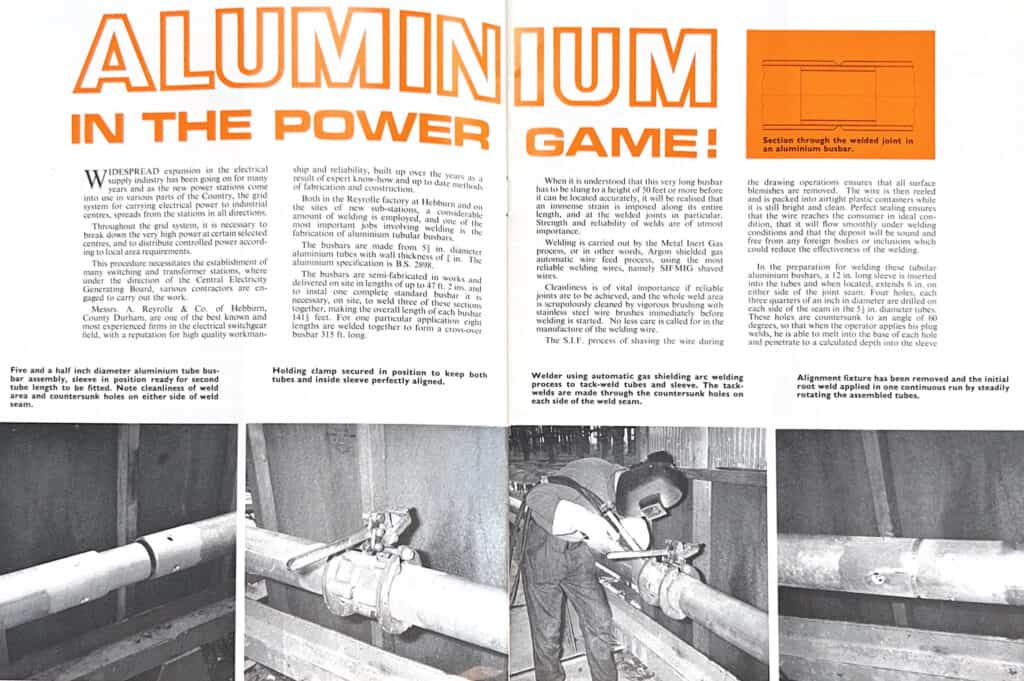
The Innovative Approach
Recognizing the complexity of this task, R. A. Revell & Co. partnered with Suffolk Iron Foundry (SIF), a company established in 1935 and renowned for its advanced welding technologies. SIF’s expertise in Metal Inert Gas (MIG) welding and their SIFMIG shaved wires became crucial to the project.
SIFMIG shaved wires were chosen for their reliability and precision. The S.I.F. process involved meticulous shaving of the wire during drawing operations to remove all surface blemishes. This ensured that the wire remained free from oxidation and impurities until it was used, guaranteeing a clean and strong weld.
Execution
The welding process began with thorough preparation of the aluminium tubes. Each tube end was chamfered to an angle of 60 degrees to ensure perfect root penetration. A 12-inch long sleeve was inserted into the tubes, extending 6 inches on either side of the joint seam. Four countersunk holes were drilled on each side of the seam to facilitate plug welding, ensuring a strong and void-free weld root.
Site welding at the Pelham Switching and Transformer Station in Hertfordshire involved setting up the 47-foot tubes in specially designed holding clamps. These clamps kept the tubes perfectly aligned, allowing the welder to lay down the initial root run in one continuous pass. This technique avoided the uneven deposition that could result from traditional tack welding methods.
Multiple welding passes were made to complete each joint, with stainless steel wire brushing between passes to remove any blemishes. The final welds were meticulously ground and polished to ensure a smooth, strong joint free from any inclusions or defects.
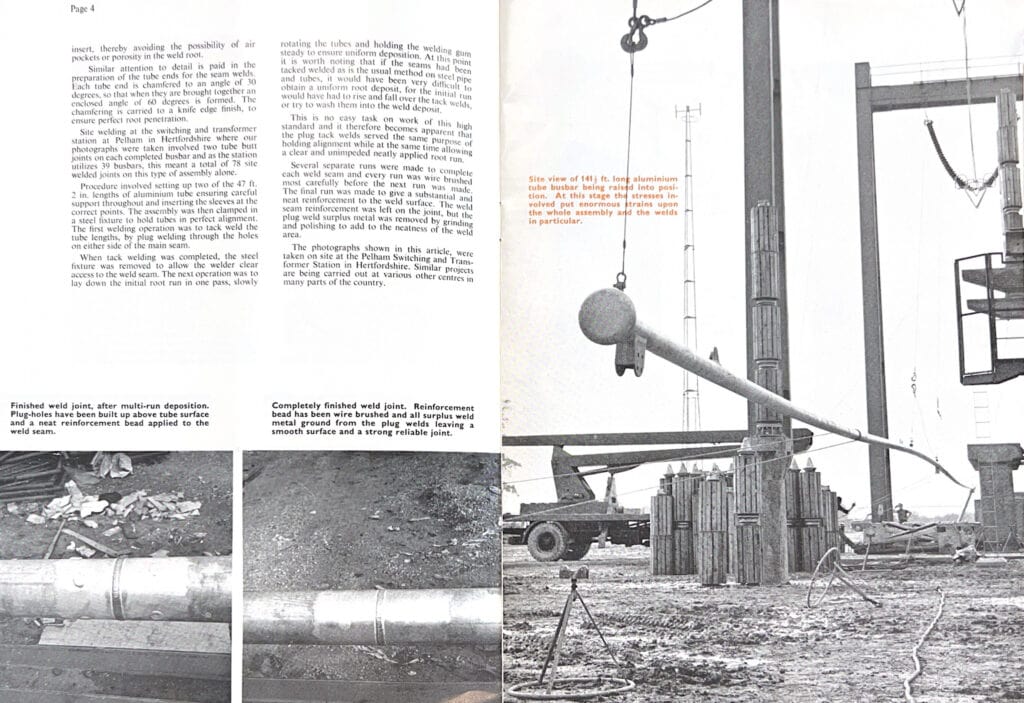
Impact and Legacy
The successful fabrication and installation of the aluminium busbars at Pelham Station were a testament to the effectiveness of SIF’s welding technology. The reliability of these welds ensured the efficient transmission of electrical power across the grid, supporting the expanding electrical infrastructure.
The photographs and detailed descriptions of the welding process highlighted in industry publications served as a benchmark for similar projects across the country. R. A. Revell & Co.’s reputation for high-quality workmanship and innovative fabrication methods was further solidified, thanks in no small part to the support from SIF.
Conclusion
The collaboration between R. A. Revell & Co. and Suffolk Iron Foundry exemplifies the power of combining industry expertise with advanced technology. SIF’s precision welding techniques and high-quality materials played a crucial role in the successful fabrication of aluminium busbars, ensuring the reliability of the electrical grid during a period of rapid expansion.
This historical case study underscores the importance of innovation, meticulous preparation, and skilled execution in engineering projects. It highlights how strategic partnerships and the adoption of advanced technologies can overcome complex challenges and drive progress, leaving a lasting legacy in the field of electrical power distribution.