Introduction
The early 1960s were a transformative period for household technology, with the refrigerator becoming an indispensable part of modern living. Among the most notable advancements in this domain was the A.E.I. Hotpoint’s 1961 “Iced Diamond” refrigerator. Designed to perfection, these refrigerators represented the pinnacle of innovation, elegance, and functionality. Central to their manufacturing success was the expert support of Suffolk Iron Foundry (SIF), whose advanced welding techniques ensured these kitchen marvels met the highest standards of quality and reliability.
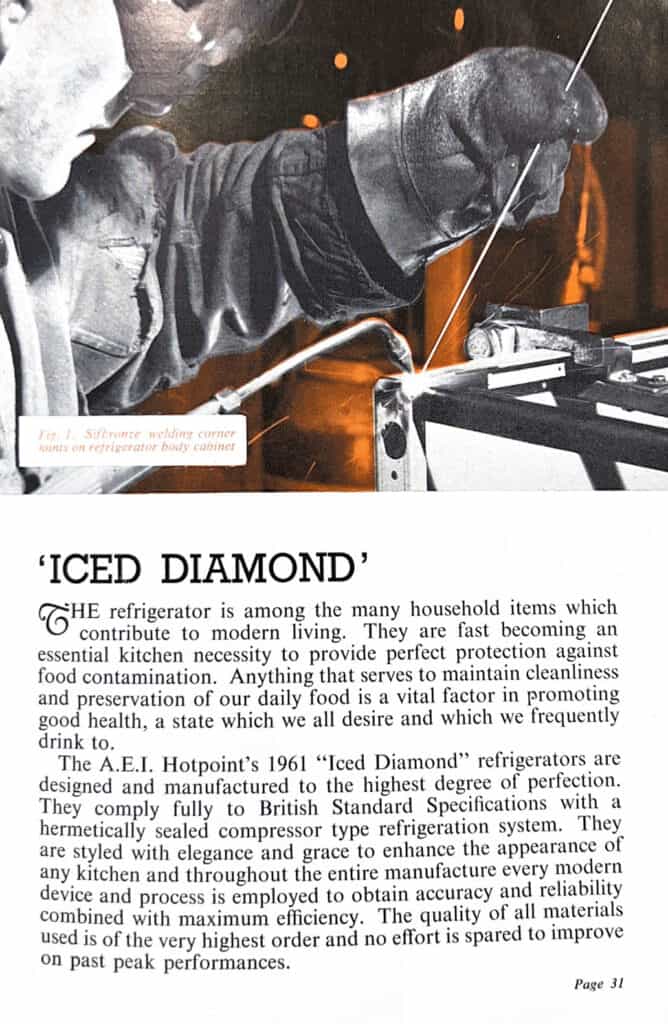
The Need for Perfection in Modern Living
Refrigerators were rapidly evolving from luxury items to essential household appliances, crucial for maintaining food safety and promoting good health. The “Iced Diamond” series from Hotpoint was a leap forward, promising not only superior performance but also aesthetic appeal. To achieve this, every aspect of their production needed to be flawless, a challenge that required cutting-edge technology and exceptional craftsmanship.
The Role of Welding in Refrigerator Manufacturing
Manufacturing the “Iced Diamond” refrigerators involved several advanced processes, with welding playing a pivotal role in ensuring the structural integrity and functionality of the units. Each refrigerator featured a hermetically sealed compressor type refrigeration system, compliant with British Standard Specifications. The compressors, cabinet structures, and door panels all required precise welding to maintain their form and function under constant use.
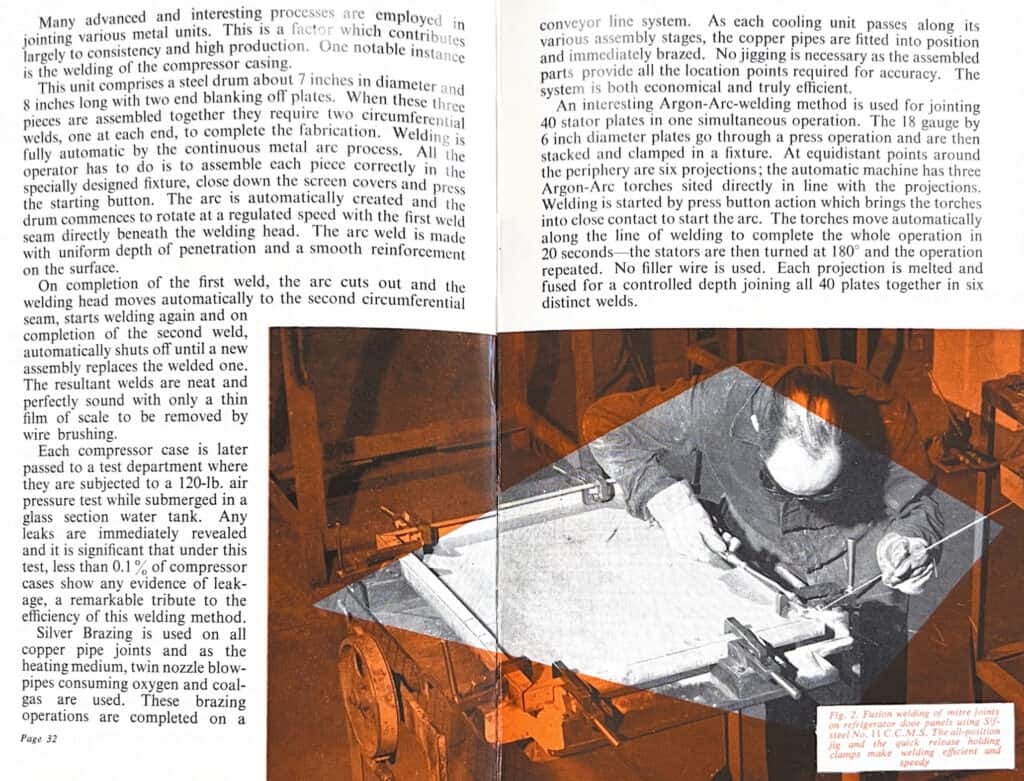
SIF’s Critical Support
Suffolk Iron Foundry (SIF) brought their expertise to bear in this ambitious project. Their Sifbronze welding products and techniques were integral to various stages of the refrigerator’s production, providing the necessary strength and reliability.
- Welding the Compressor Casing:
- The compressor casing, a vital component of the refrigerator, consisted of a steel drum with end plates. SIF’s continuous metal arc process automated this welding task, ensuring uniform depth of penetration and smooth reinforcement. This precision reduced defects and enhanced the durability of the compressors.
- Silver Brazing Copper Pipe Joints:
- The use of SIF’s silver brazing methods on copper pipe joints ensured leak-proof connections. Twin nozzle blowpipes using oxygen and coal-gas allowed for efficient brazing along the assembly line, crucial for the cooling system’s reliability.
- Argon-Arc Welding of Stator Plates:
- Joining 40 stator plates simultaneously with argon-arc welding was another example of SIF’s innovation. This automated process melted and fused each projection precisely, ensuring consistent and robust joints, essential for the operational efficiency of the cooling units.
- Sifbronze Welding on Cabinet Corners:
- The main body of the refrigerator cabinets was formed from single sheets of mild steel, requiring low-temperature Sifbronze welding for assembly. This method minimized distortion, ensuring the cabinets maintained their shape and structural integrity.
- Fusion Welding on Door Panels:
- The refrigerator doors, crafted from high-grade mild steel, required precise oxy-acetylene fusion welding. The Sifsteel No. 11 welding wires used for these joints produced neat, strong, and reliable welds, contributing to the overall durability and aesthetic finish of the refrigerators.
Historical Impact and Legacy
The meticulous welding processes supported by SIF were instrumental in the production of over 4,000 “Iced Diamond” refrigerators weekly, totaling 16,000 Sifbronze welds. The resulting products had negligible defects, underscoring the effectiveness of SIF’s contributions. This collaboration not only enhanced the quality and efficiency of Hotpoint’s refrigerators but also set new industry standards.
Photographs from the era show skilled welders at work, their precision and expertise evident in every joint and seam. The successful integration of SIF’s welding technologies ensured that each refrigerator met the rigorous demands of modern households, combining elegance with unmatched reliability.
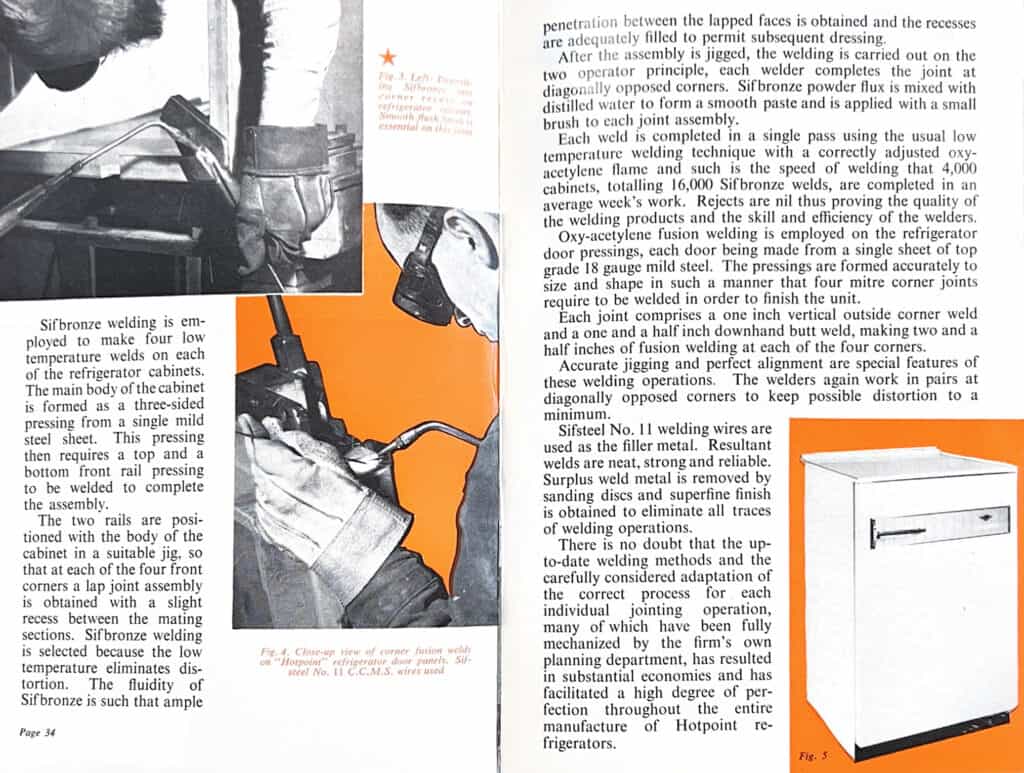
Conclusion
The story of Hotpoint’s “Iced Diamond” refrigerators is a testament to the power of collaboration and technological innovation. Suffolk Iron Foundry’s advanced welding solutions played a crucial role in turning a visionary design into a practical, everyday essential. This case study highlights the importance of quality craftsmanship and the enduring impact of SIF’s contributions to the home appliance industry.
Through the seamless integration of SIF’s expertise, the “Iced Diamond” refrigerators not only enhanced the daily lives of countless families but also paved the way for future advancements in household technology. The legacy of this collaboration continues to inspire excellence in manufacturing and engineering, reminding us of the importance of precision and reliability in creating products that stand the test of time.
4o
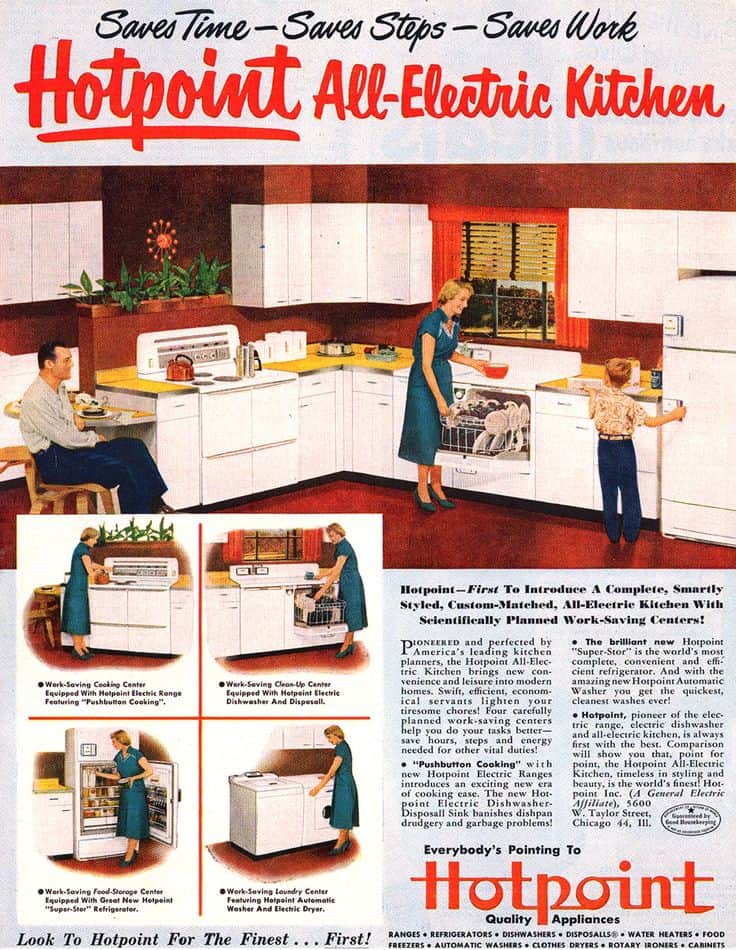
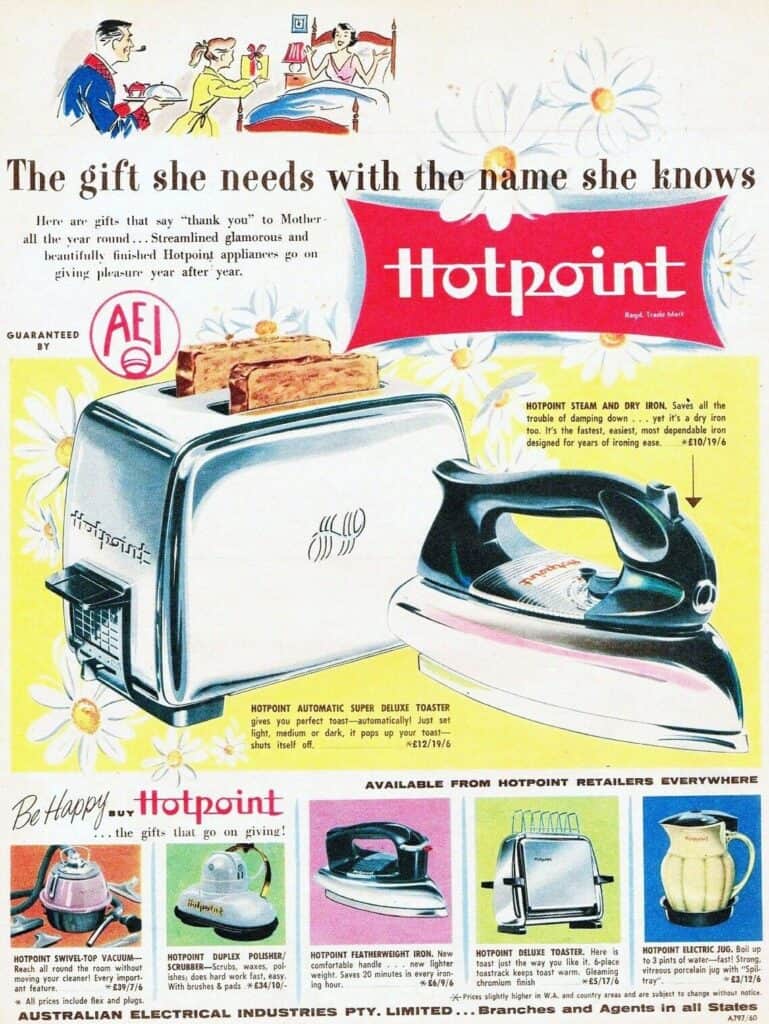
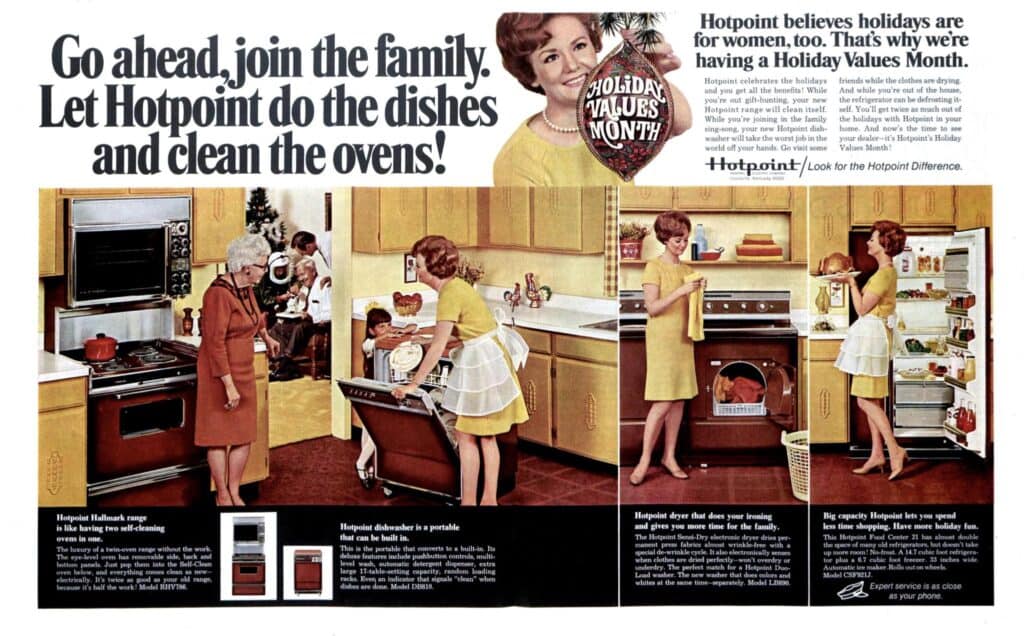
- References –
- 1960 Hotpoint Poster – https://uk.pinterest.com/pin/hotpoint-1960–762586149382435038/
- 1968 Hotpoint Appliances Ad – https://www.reddit.com/r/vintageads/comments/155szrb/1968_hotpoint_appliances_ad/?rdt=41052
- 1950 Hotpoint All-electric Kitchin Ad – https://ar.pinterest.com/pin/1950-hotpoint-allelectric-kitchen-vintage-ad-advertising-etsy-canada–339881103141811054/
- Vintage 1954 Hotpoint Super-Oven Commercial – https://www.youtube.com/watch?v=yBWY8qLIbCQ
- Vintage Hotpoint Commercial – https://www.youtube.com/watch?v=3uqgewhR7Pg
- Article Links –
- Our Story – https://www.hotpoint.com/hotpoint-history/