Introduction
In the annals of British engineering, few projects stand out as prominently as the construction of the Mersey road tunnels. These subterranean highways have long been vital arteries connecting Liverpool and Birkenhead, bearing the weight of thousands of vehicles daily. By the mid-1960s, the need for a new tunnel to alleviate traffic congestion had become pressing. This is the story of how the new Mersey road tunnel was built, the challenges faced by its builders, and how Suffolk Iron Foundry (SIF) played a pivotal role in its construction.
The Challenge: Constructing a Modern Tunnel
Authorized by the Mersey Tunnel Act of 1965, the new tunnel’s construction was overseen by the Mersey Tunnel Joint Committee. This committee included representatives from Liverpool, Birkenhead, and Wallasey. The chosen site for the new tunnel was about one mile downstream from the first road tunnel, which had been built between 1926 and 1934. This older tunnel provided a crucial four-lane highway between Liverpool and Birkenhead but had become increasingly congested over the decades.
The task at hand was daunting: constructing a new tunnel under the River Mersey, dealing with the damp, dirty, and challenging conditions inherent to such an endeavor. Initial work began in December 1965 with the excavation of a pilot tunnel. This phase involved extensive borings, echo-soundings, and sonar surveys to determine rock levels and strata. The pilot tunnel, excavated by Marples Ridgway Ltd., was essential for identifying faults and assessing water inflow problems, which could then be mitigated through fissure grouting.
The Main Tunnel Construction
The pilot tunnel’s success demonstrated the benefits of using machinery for excavation. This led to the decision to employ an economical segmental lining for the main tunnel, which was critical for maintaining the structure’s integrity under the river. In April 1967, the main construction contract was awarded to a consortium comprising Edmund Nuttall, Sons and Co. (London) Ltd., Guy F. Atkinson and Co., and Sir Alfred McAlpine and Son Ltd.
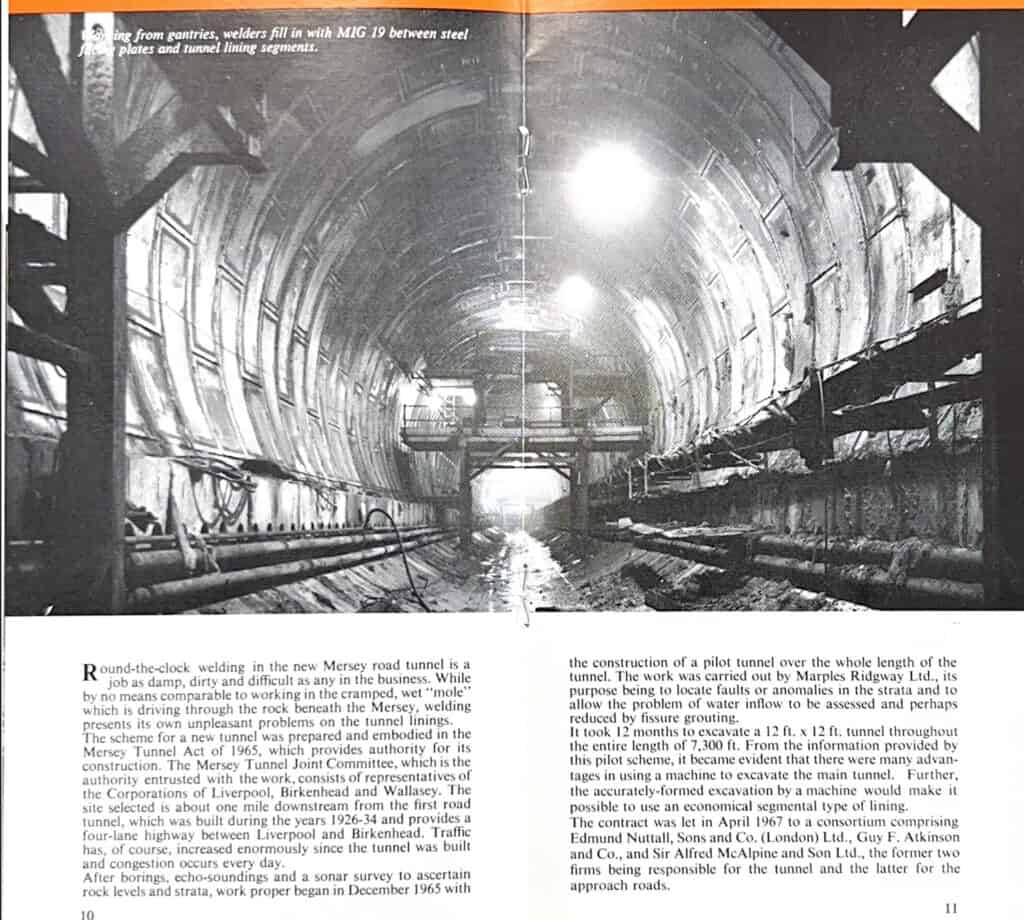
SIF’s Crucial Support
Amidst these engineering feats, the role of welding became paramount. Welding the tunnel lining segments, ensuring they were both watertight and structurally sound, presented a significant challenge. This is where Suffolk Iron Foundry (SIF) came in, providing expertise and advanced welding solutions that were critical to the project’s success.
- Welding Tunnel Lining Segments:
- The tunnel lining segments required precise and robust welding to withstand the pressures exerted by the river above. SIF’s advanced MIG 19 welding techniques were employed, ensuring that the steel flange plates and tunnel lining segments were securely joined. This process was crucial for preventing water ingress and maintaining the tunnel’s structural integrity.
- Round-the-Clock Operations:
- Given the scale of the project, welding operations had to be conducted around the clock. Welders, working from gantries, filled in gaps between the steel plates, ensuring seamless joints. SIF’s reliable welding materials and techniques were essential for maintaining the high standards required for this continuous operation.
- Dealing with Adverse Conditions:
- The working conditions were far from ideal, characterized by dampness, dirt, and confined spaces. Despite these challenges, SIF’s welding solutions proved resilient, ensuring that the welds remained strong and durable under harsh conditions.
Historical Impact
The completion of the new Mersey road tunnel marked a significant milestone in British engineering. It not only alleviated traffic congestion but also showcased the ingenuity and resilience of the engineers and workers involved. The tunnel’s construction, supported by SIF’s welding expertise, stands as a testament to the collaboration between different companies and the application of advanced industrial techniques.
Photographs from the era capture the scale of the operation, with welders meticulously working on the tunnel linings, their efforts illuminated by the harsh lights of the underground environment. These images highlight the critical role of welding in ensuring the tunnel’s success and longevity.
Conclusion
The story of the new Mersey road tunnel is a celebration of human ingenuity and industrial collaboration. Suffolk Iron Foundry’s contributions, through their advanced welding techniques, were instrumental in overcoming the significant challenges posed by the project. This case study not only underscores the importance of quality welding in large-scale construction projects but also commemorates the skilled workers whose efforts made such engineering marvels possible.
As traffic flows smoothly through the tunnel today, it serves as a lasting reminder of the remarkable achievements of those who dared to build beneath the river, and the indispensable support of companies like SIF in making such visions a reality.
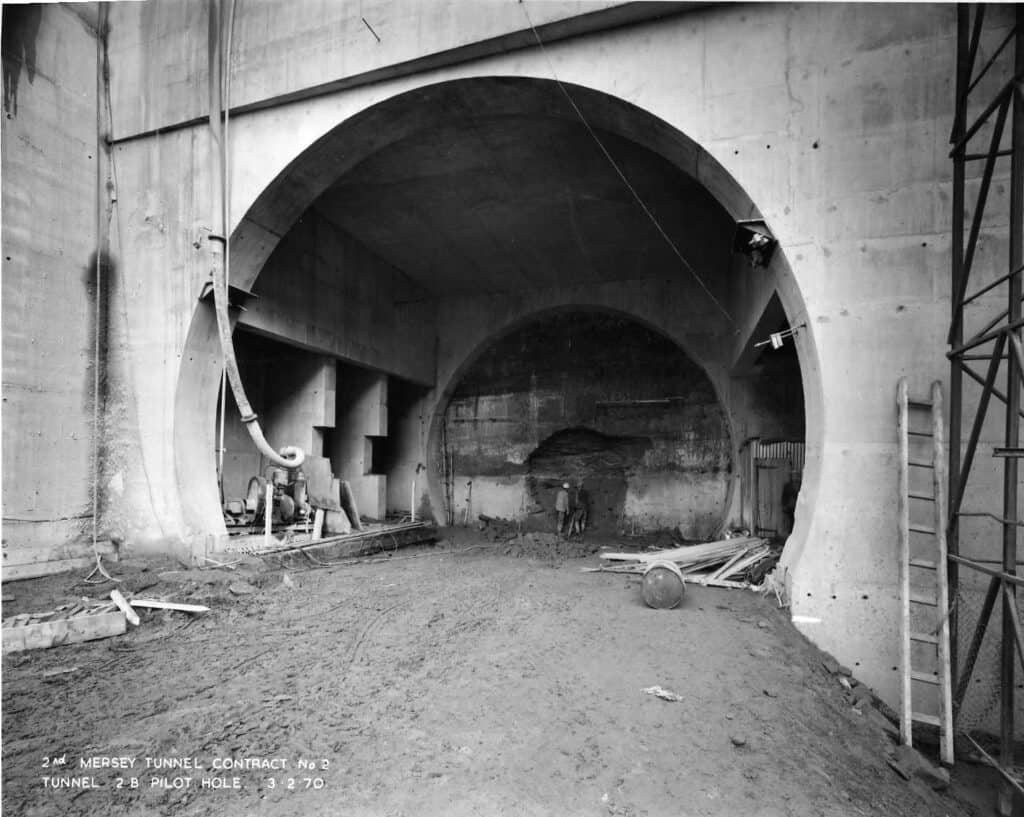
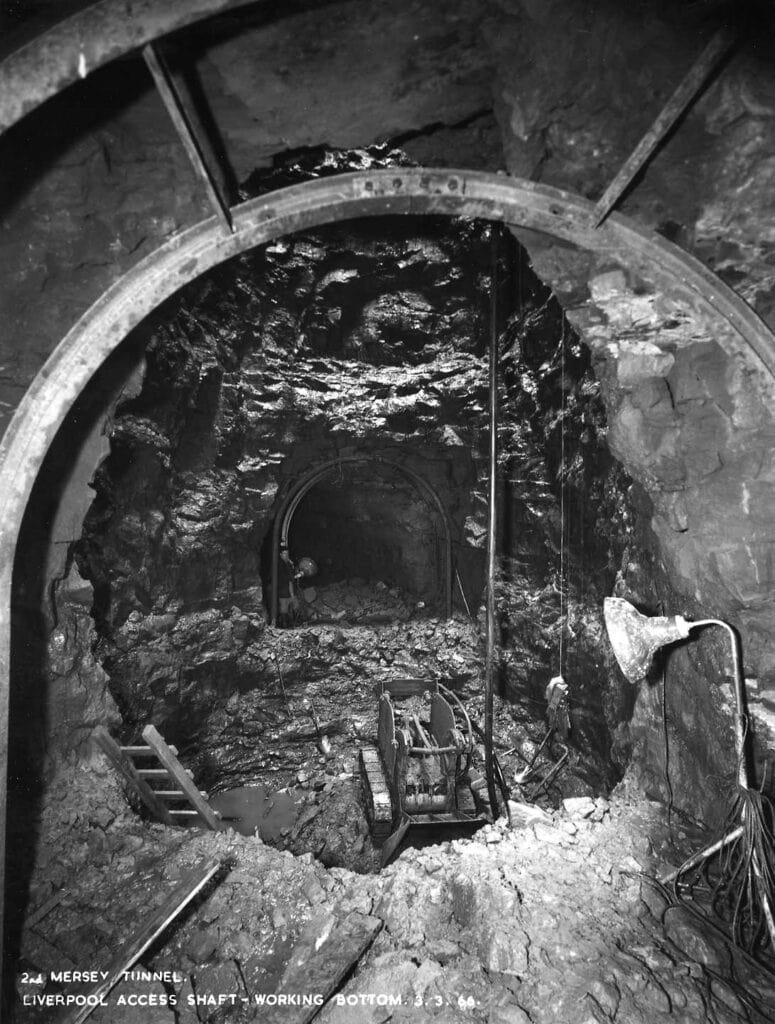
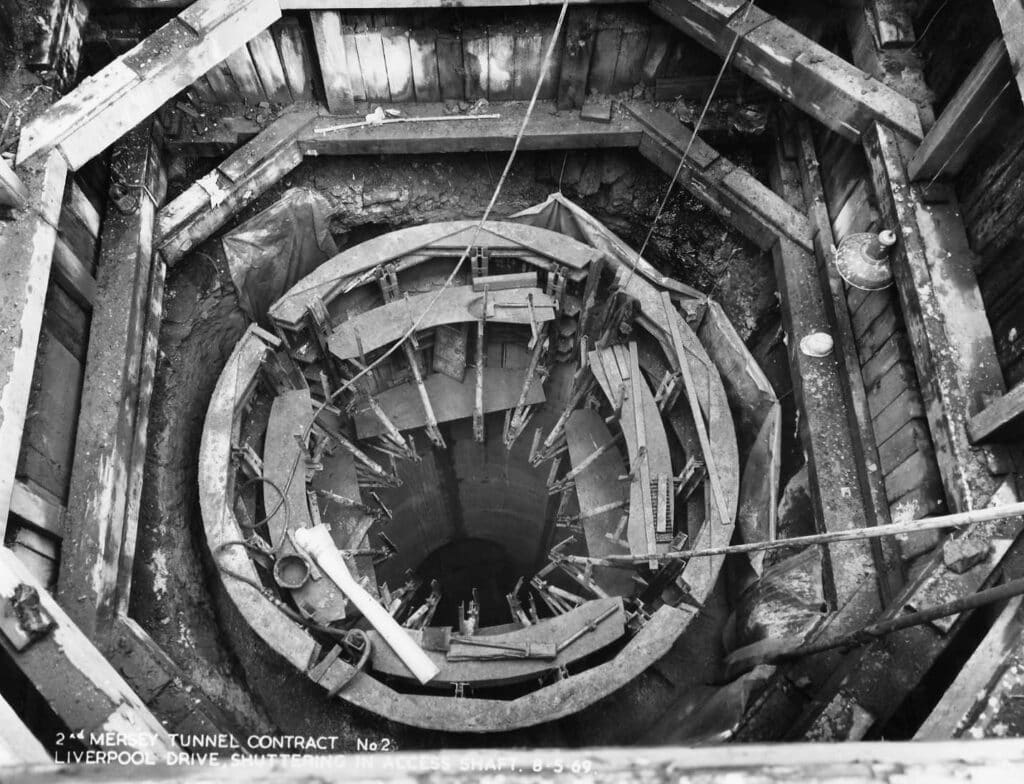
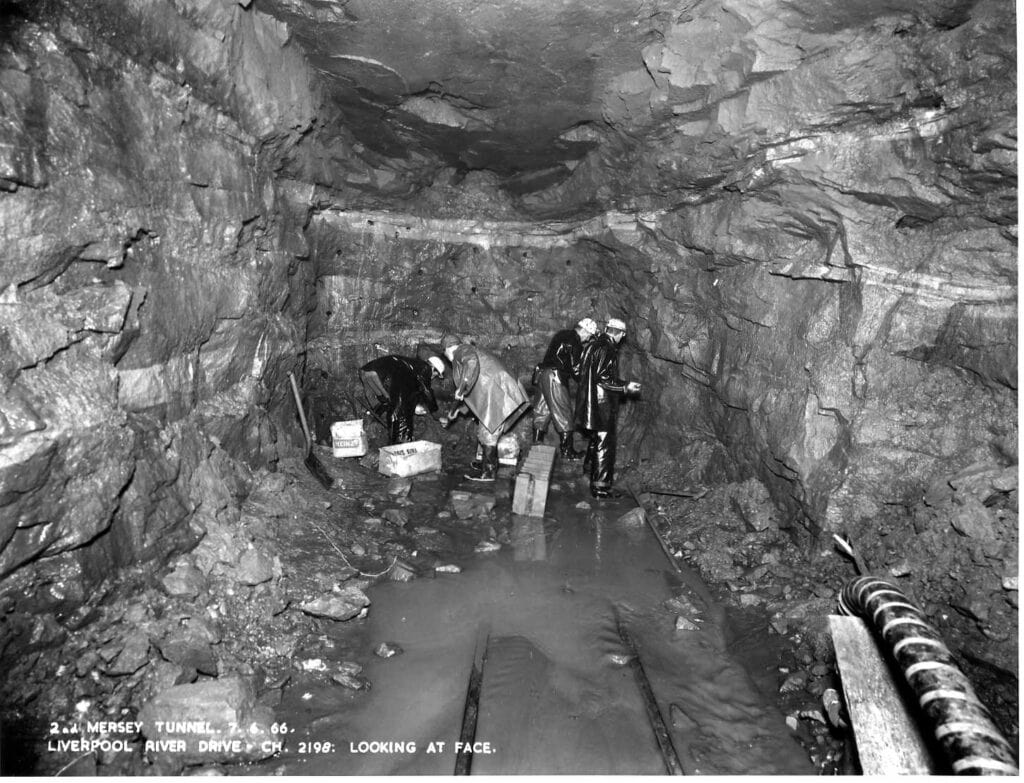
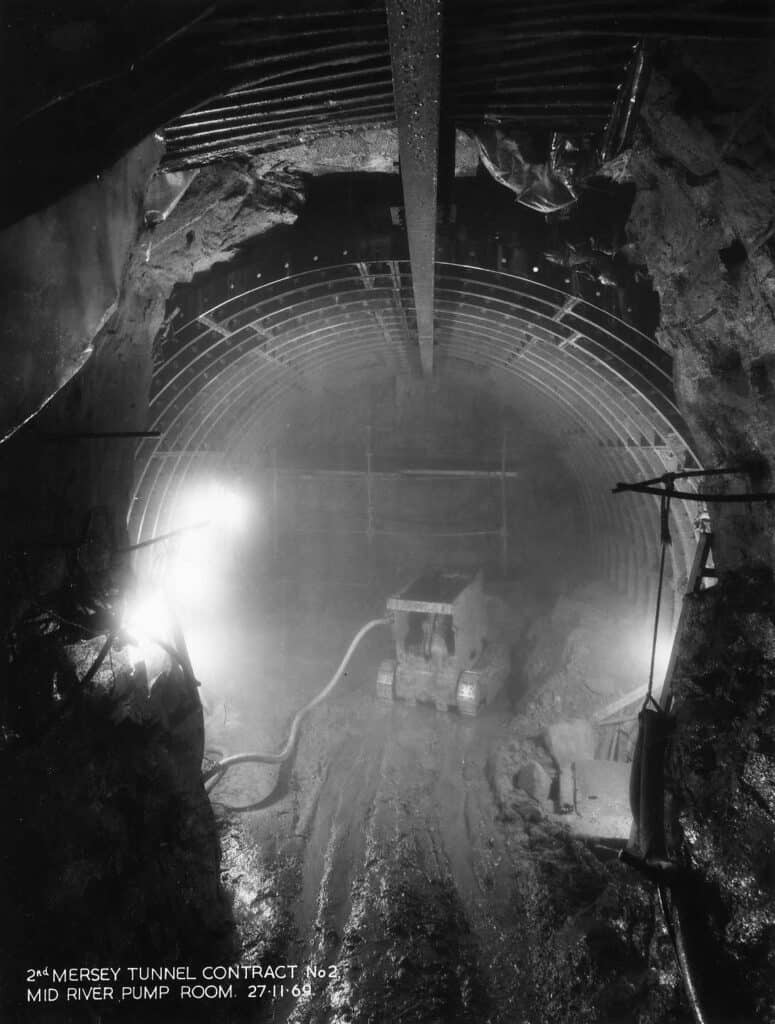

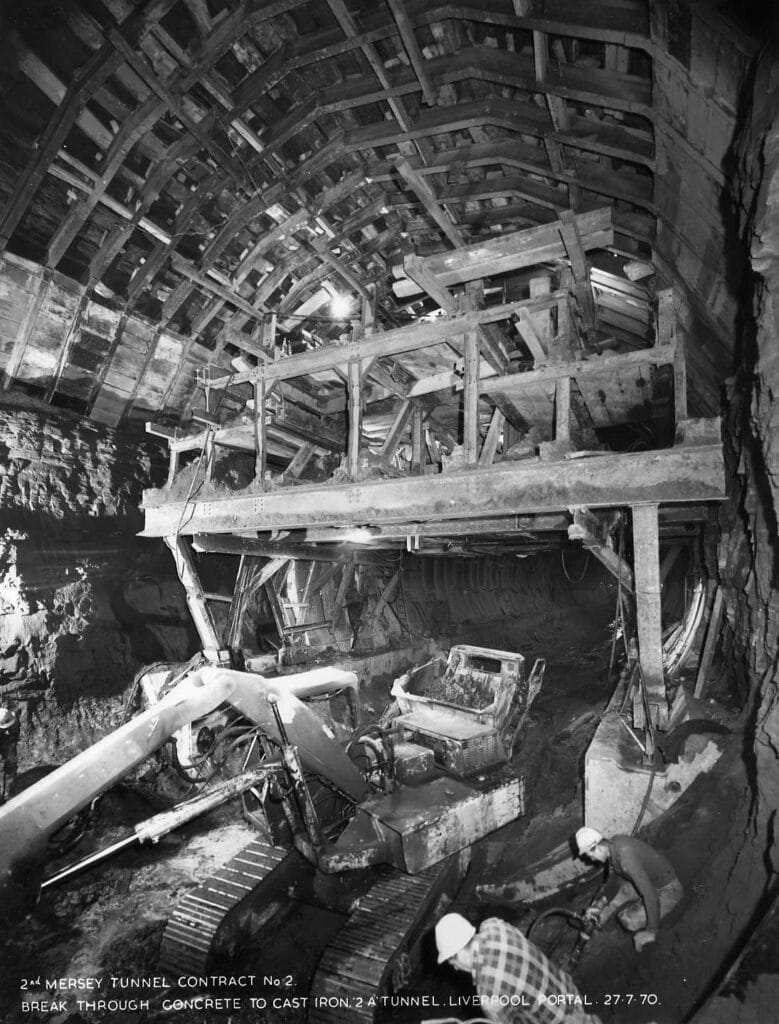
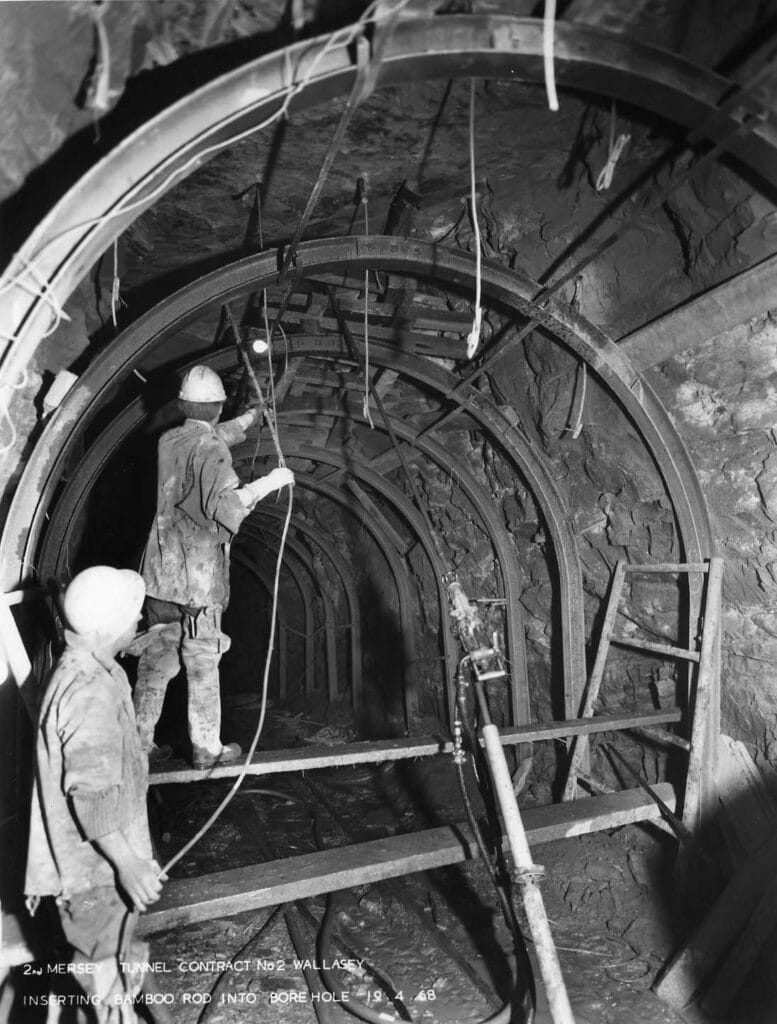
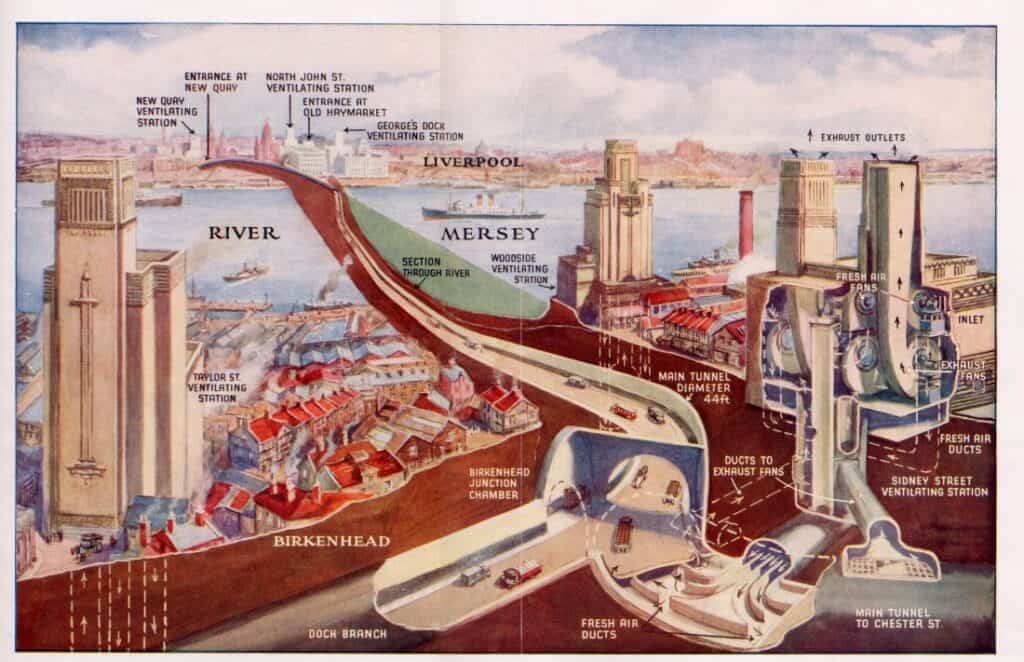
- Article Links –
- http://www.tunnelusers.org.uk/history.htm
- https://www.liverpoolmuseums.org.uk/why-queensway-mersey-tunnel-was-built
- https://www.liverpoolecho.co.uk/news/liverpool-news/story-merseysides-road-tunnels-men-24814913
- References –
- The Building of Mersey Tunnel (1,2,3,4,5,6,7) – https://www.liverpoolcityregion-ca.gov.uk/news/the-building-of-kingsway-tunnel-in-pictures
- Magic Of The Mersey Tunnels – Full Documentary – https://www.youtube.com/watch?v=hjSczoLTUjQ
- Steam under the Mersey. The Mersey railway. The first Mersey Tunnel – https://www.youtube.com/watch?v=wZdWkdw2V6c