In the bustling city of London, where red double-decker buses have become an iconic symbol, keeping the largest fleet of buses and coaches running smoothly is no small feat. This case study delves into the meticulous processes and innovative approaches adopted by London Transport in the mid-20th century to ensure their fleet’s reliability, with a particular focus on the pivotal role played by the Suffolk Iron Foundry (SIF).
Background
By the mid-1960s, London Transport managed a fleet of nearly 8,000 vehicles, including buses and coaches, serving millions of passengers daily. Maintaining such an extensive fleet required not only routine maintenance but also efficient repair and refurbishment processes to extend the vehicles’ operational life. London Transport’s strategy involved leveraging modern factory techniques and specialized support from external partners like SIF to achieve this goal.
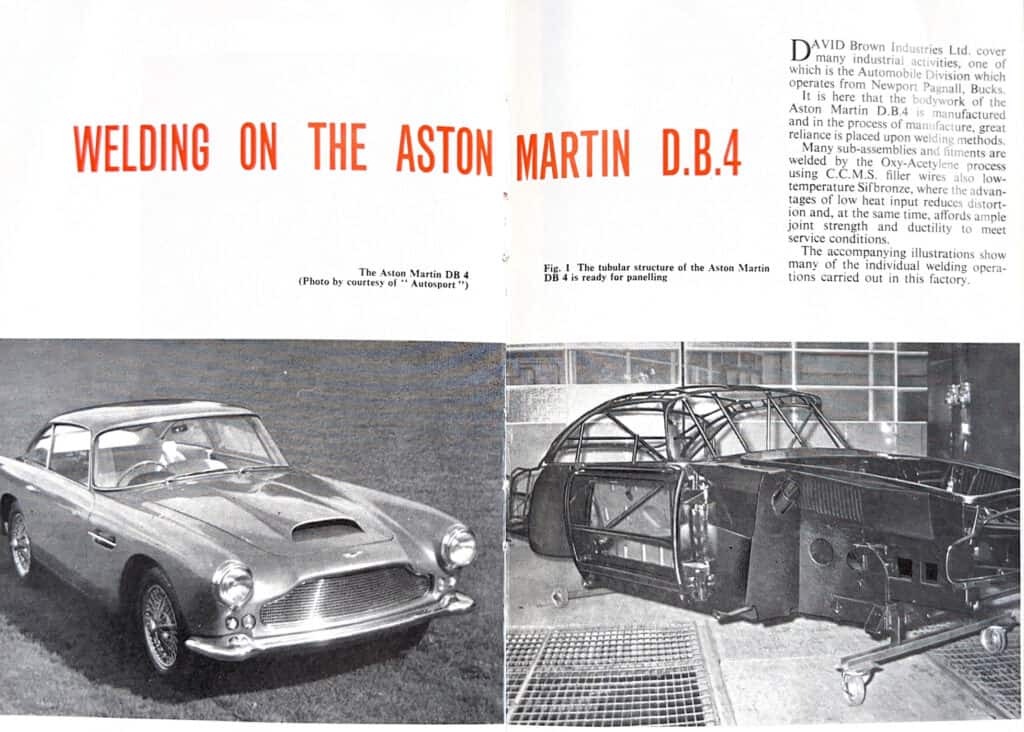
The Maintenance Challenge
Operating the world’s largest bus fleet came with significant challenges. Each bus was expected to have a working life of around twenty years, which necessitated rigorous and regular maintenance. The operational efficiency was distributed across various facilities:
- Local Garages: Equipped for day-to-day maintenance and replacement of parts.
- Aldenham Works: Dedicated to the overhaul of bus bodies and chassis.
- Chiswick Works: Focused on the overhaul of electrical and mechanical units.
A key aspect of maintaining such a large fleet was the cost-effective repair of vehicle components. Rather than replacing parts outright, London Transport’s strategy involved detailed inspection and refurbishment of components, ensuring they met stringent standards for reliability and performance.
Innovative Repair Techniques at Chiswick Works
Chiswick Works became the heart of London Transport’s repair operations. Here, each failed unit, such as an engine or gearbox, was dismantled entirely. Every part underwent thorough cleaning and inspection to determine its suitability for further use. Parts were categorized as:
- Serviceable: Fit for immediate use.
- Repairable: Capable of being economically repaired.
- Scrap: Beyond repair and discarded.
This meticulous approach ensured that no sub-standard parts were reused, minimizing the risk of future failures. The emphasis on repair over replacement led to significant cost savings and extended the life of many components.
The Role of Suffolk Iron Foundry (SIF)
Suffolk Iron Foundry played a crucial role in supporting London Transport’s repair efforts, particularly in the welding and reclamation processes. SIF’s expertise in cast welding was indispensable for repairing large, complex parts that were too damaged for conventional repair methods.
One notable collaboration involved the repair of cylinder control sleeves. Originally costing 40 shillings each, these sleeves were repaired at a fraction of the cost—8 shillings—using advanced electrolysis techniques to build them up with a layer of pure nickel. This process, supported by SIF’s welding capabilities, ensured that repaired parts met the same high standards as new ones.
Achieving Efficiency and Sustainability
The integration of external expertise from SIF and other specialized firms allowed London Transport to maintain a high standard of operational efficiency. The Chiswick Works, equipped with dedicated sections for cast iron, light alloy, and miscellaneous repairs, operated like a well-oiled machine. Key practices included:
- Comprehensive Dismantling: Ensuring every part was inspected and categorized.
- Advanced Welding Techniques: Utilizing SIF’s capabilities to repair parts that would otherwise be scrapped.
- Economic Repairs: Prioritizing cost-effective repairs to maximize the value of each component.
By the 1960s, nearly 50 buses were overhauled weekly at Aldenham Works, with corresponding units passing through Chiswick for mechanical refurbishment. This streamlined process was a testament to the effective planning and collaboration that underpinned London Transport’s maintenance strategy.
Conclusion
The success of London Transport’s maintenance program in the mid-20th century was a result of meticulous planning, innovative repair techniques, and strategic collaborations. The support from Suffolk Iron Foundry, particularly in advanced welding and repair, was instrumental in ensuring the longevity and reliability of the fleet. This case study highlights how historical practices and partnerships can offer valuable lessons in efficiency, sustainability, and operational excellence.
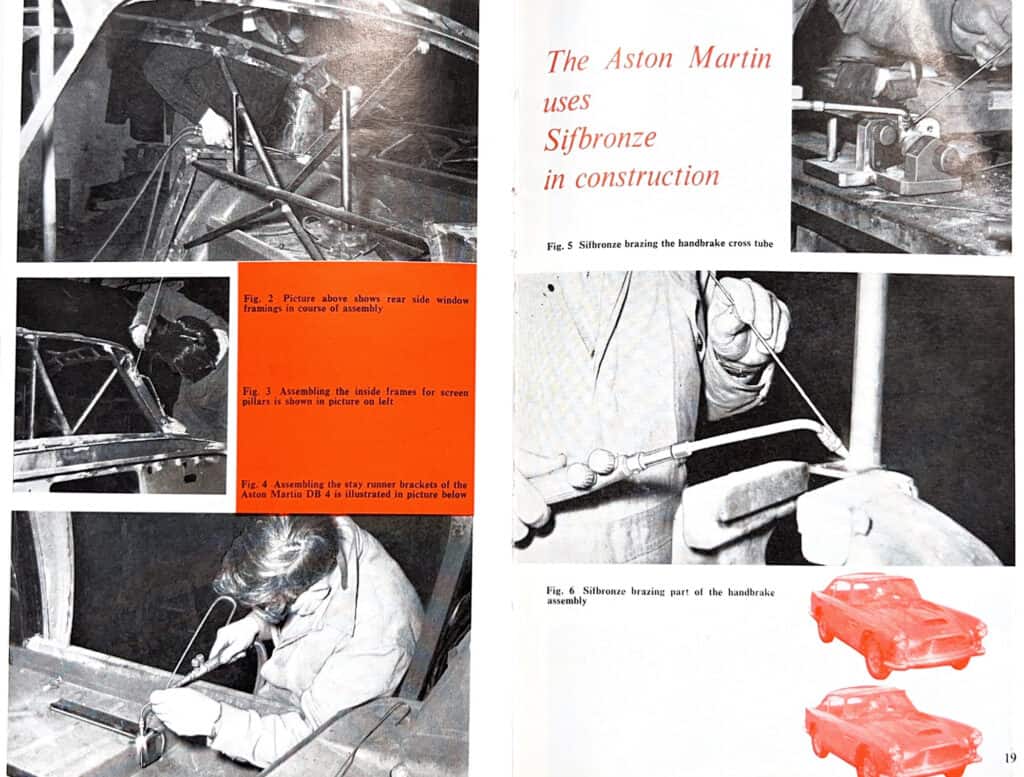
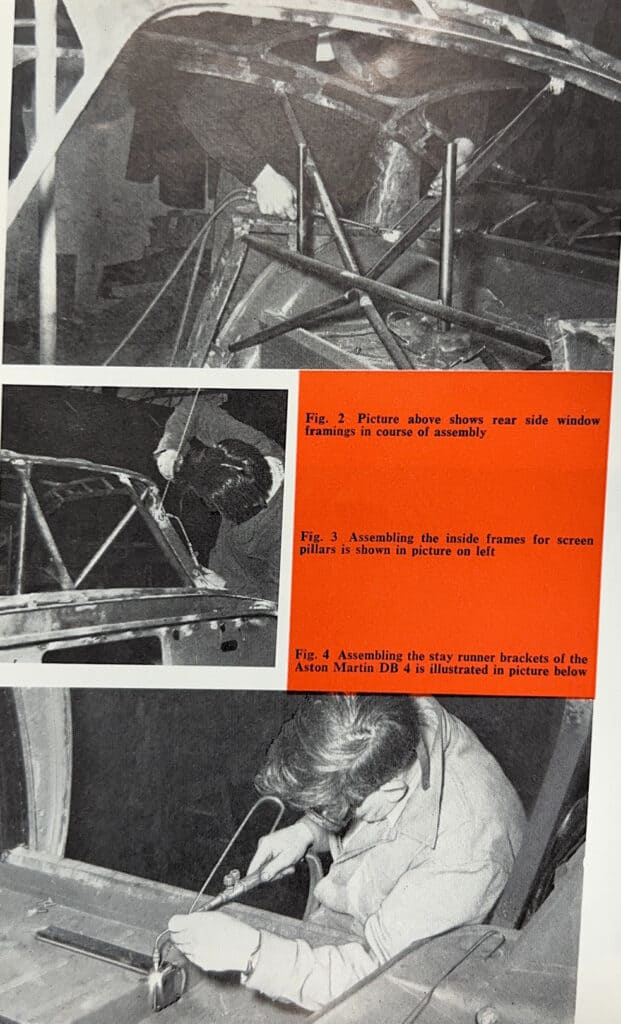
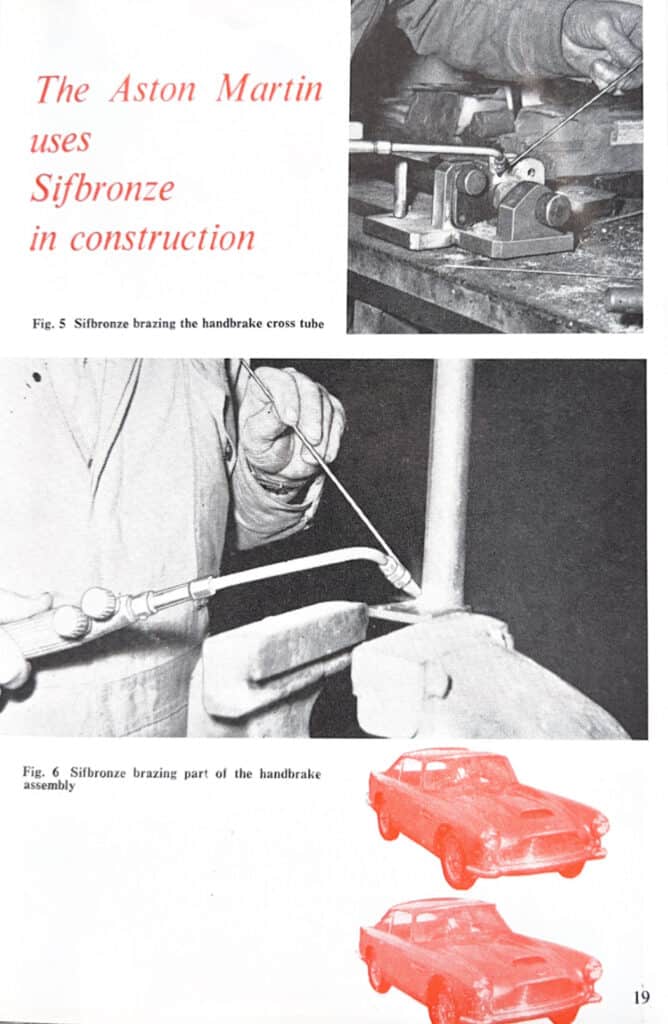
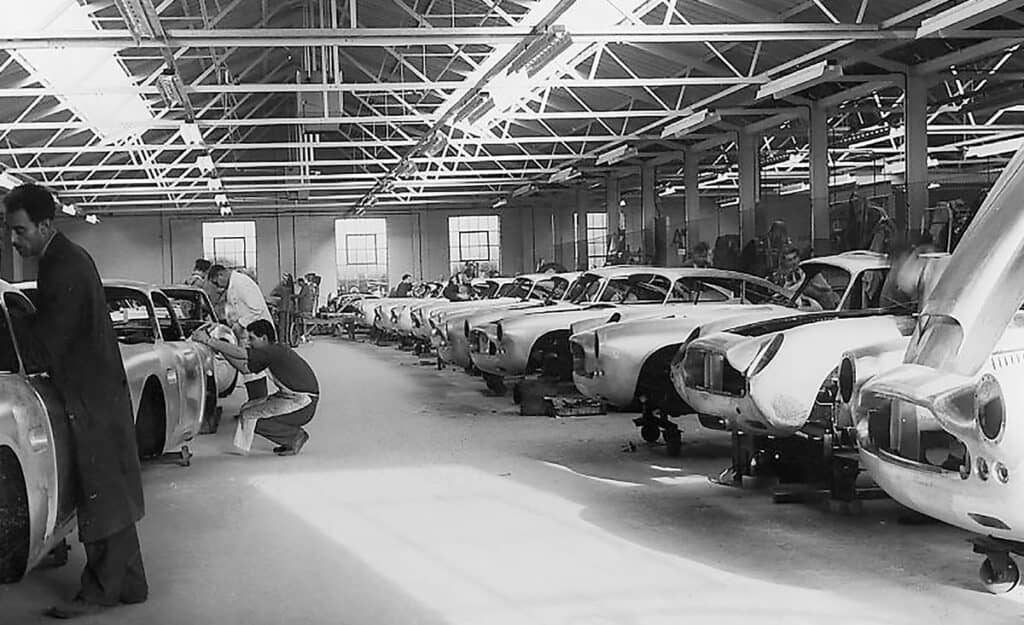

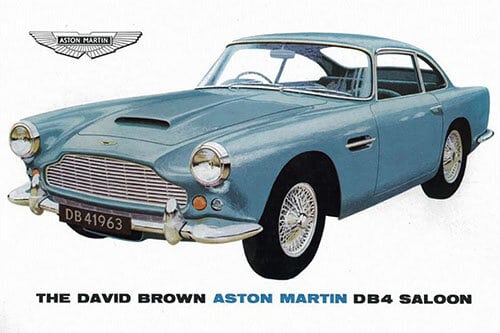
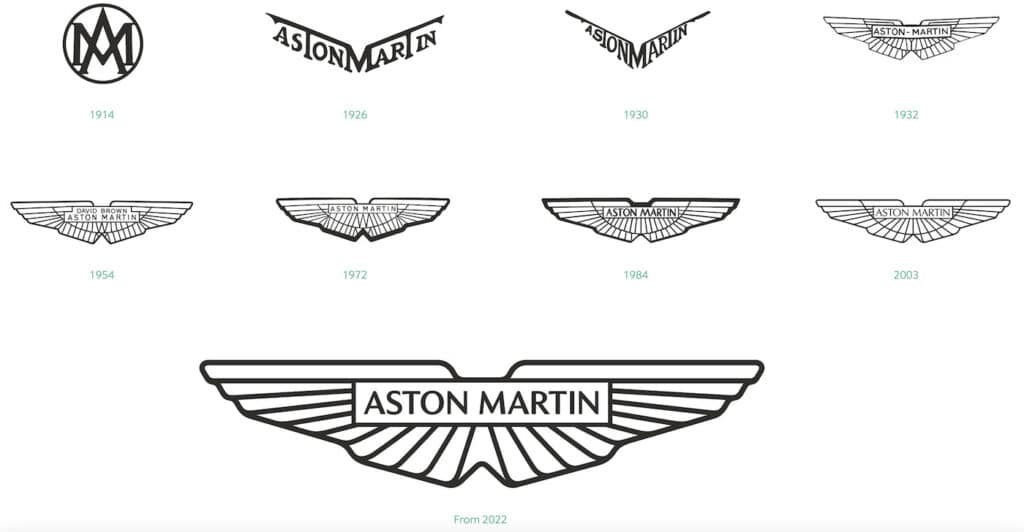
- References –
- Production, Overhaul, British Transport Films, 1958 – https://www.ltmuseum.co.uk/collections/collections-online/film-video/item/2018-948
- London Transport Aldenham Bus Works – https://www.youtube.com/watch?v=ngFAa8Floac
- Shillibeer horse bus on Bury Street in 1829 – https://www.ltmuseum.co.uk/collections/collections-online/artwork/item/1996-86
- Early motor bus and a horse bus, 1900 – https://www.ltmuseum.co.uk/collections/collections-online/photographs/item/1998-75518
- old-london-transport logo – https://www.clicksouvenirs.com/p/history-of-the-london-bus
- Article Links –
- A short history of London’s buses – https://www.ltmuseum.co.uk/collections/stories/transport/short-history-londons-buses