Products Used in the Fabrication of the Boiler:
- Sifbronze Welding Materials are extensively used in the construction of the inner and outer welded sections, ensuring the boiler’s durability and integrity.
- Sifsil Copper Filler Rods: Employed in the fusion welding process for joining copper components, providing solid and pressure-resistant welds.
- Copper Welding Procedure: This is a specialised technique critical for creating airtight seals in the boiler’s high-pressure environment.
The fabrication of a two-ton boiler is no ordinary task. At J.A. Welch Coppersmiths Ltd. of London, this monumental job was undertaken for an essential oils distillation plant. With a 250-gallon capacity, this specific boiler is needed to withstand the demanding conditions of heating under 180 pounds per square inch of steam pressure. The result was a feat of engineering precision, relying on Sifbronze welding materials and expert craftsmanship to produce an industrial boiler that would not only meet but exceed the required performance standards.
The boiler consisted of two main components: an outer welded shell of steel and an inner copper vessel, separated by a jacket in which high-pressure steam circulated. This complex structure required exceptional attention to detail, especially considering the working pressures involved. The choice of Sifbronze welding materials was critical in ensuring that the joints and seams were capable of withstanding not only the pressure but also the high temperatures to which the boiler would be exposed.
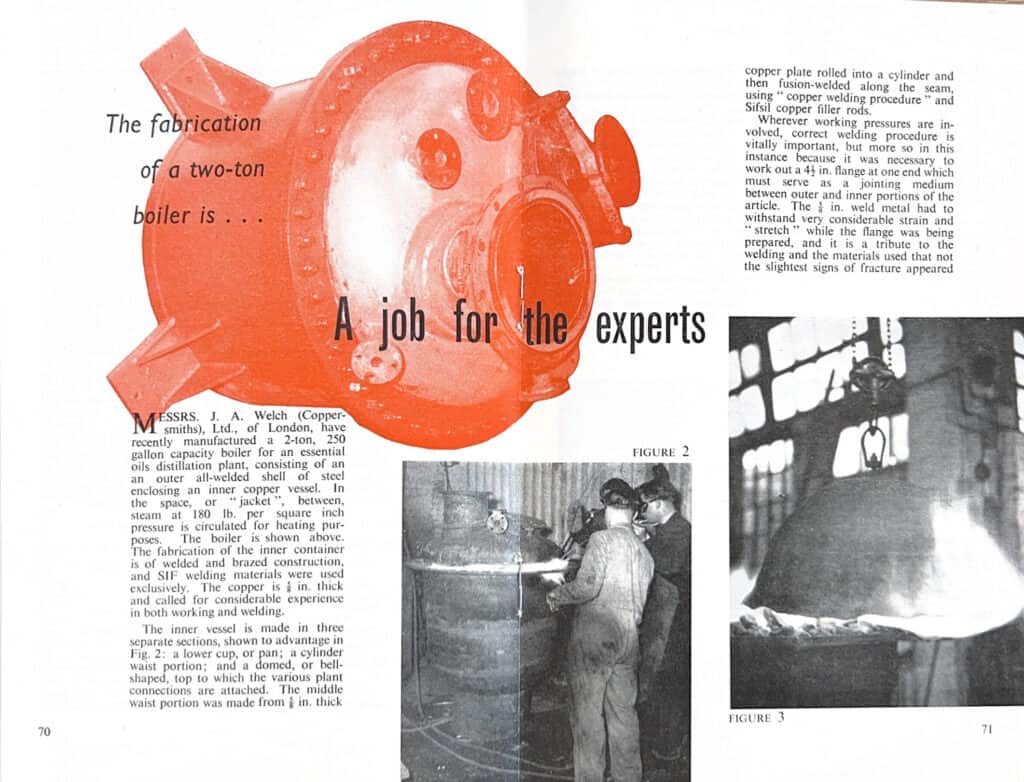
The fabrication of the inner container required the use of Sifsil copper filler rods. These rods were vital in the copper welding procedure used to fuse the copper plates that made up the vessel. The copper plate, ⅜ inch thick, was rolled into a cylinder and then fusion welded along the seam using these specialized filler rods. Given the extreme pressures and heat the boiler was designed to handle, the welds’ quality was paramount.
The boiler was fabricated in three distinct sections:
- The Lower Cup (or Pan): This was the base of the boiler, which required seamless welds to handle the considerable weight and pressure from the upper sections.
- The Waist Portion: This middle section, formed from ⅜ inch-thick copper, required precision welding to join it with the upper and lower sections.
- The Domed, or Bell-Shaped Top: The final component to which the various input and output connections were attached.
A particularly challenging aspect of the construction was the preparation of a 4 ½ inch flange at one end of the vessel, which would serve as the jointing medium between the outer and inner portions of the boiler. This flange had to be ⅜ inch thick and capable of withstanding significant strain and stretch during both the welding process and operational use. Sifbronze welding materials were crucial in ensuring that the welds remained solid and flexible, even under extreme conditions. The welding process was so precise that no signs of fracture or weakness appeared, even after extensive testing.
The final construction of the boiler was a testament to the skill and expertise of the welders at J.A. Welch Coppersmiths. Using Sifbronze and Sifsil products, they crafted a two-ton industrial vessel capable of handling high-pressure steam for extended periods. The flawless welding ensured that the boiler could operate safely and efficiently, meeting the demanding specifications required for the distillation plant.
By combining traditional coppersmithing techniques with modern welding technology, J.A. Welch produced a boiler that symbolises industrial innovation and craftsmanship. The use of Sifbronze welding materials played a critical role in the project’s success, allowing the boiler to maintain its structural integrity and performance in even the harshest conditions.