Introduction
In the dynamic world of aviation, safety and reliability are paramount. The mid-20th century saw rapid advancements in aircraft technology, accompanied by stringent standards to ensure the highest quality in every component. A key player in this evolution was the Suffolk Iron Foundry (SIF), founded in 1925, whose expertise in welding significantly contributed to the rigorous inspection and approval processes for aircraft welding. This case study explores how SIF supported the aviation industry, particularly through their involvement with Sifbronze Welding, and highlights the importance of these contributions in a historical context.
The Challenge
The Aircraft Inspection Department (A.I.D.) had established a rigid code of inspection for Oxy-Acetylene Welding on aircraft structures. Welding operators had to undergo approval tests that included visual inspection and mechanical testing of joints on various metal classes. These tests ensured that each operator met the minimum standards required to work on critical aircraft components. However, there were no specific tests or standards for Sifbronze Welding, which was primarily used for non-high-stress fittings and structures. This presented a challenge: how to maintain quality and reliability without established standards.
The SIF Solution
Recognizing the unique properties and applications of Sifbronze Welding, SIF played a crucial role in supporting the aviation industry through innovative techniques and expert guidance. While the A.I.D. focused on stringent inspections for Oxy-Acetylene Welding, SIF worked closely with aircraft designers and stress analysts to ensure that Sifbronze Welds met the necessary quality standards, even in the absence of formal testing protocols.
Implementation and Innovations
SIF’s approach involved a combination of meticulous craftsmanship and advanced welding technology. Their expertise in Sifbronze Welding allowed for precise and reliable joins on aircraft fittings, which, although not highly stressed, were crucial for the overall integrity of the aircraft. By working in conjunction with A.I.D. approved regulations, SIF ensured that these welds were visually inspected and adhered to the highest standards of quality.
The process began with thorough training for welding operators, who were instructed in the specific techniques required for Sifbronze Welding. This included understanding the material properties, optimal welding temperatures, and correct application methods. Operators were then tested on their ability to produce consistent, high-quality welds under various conditions.
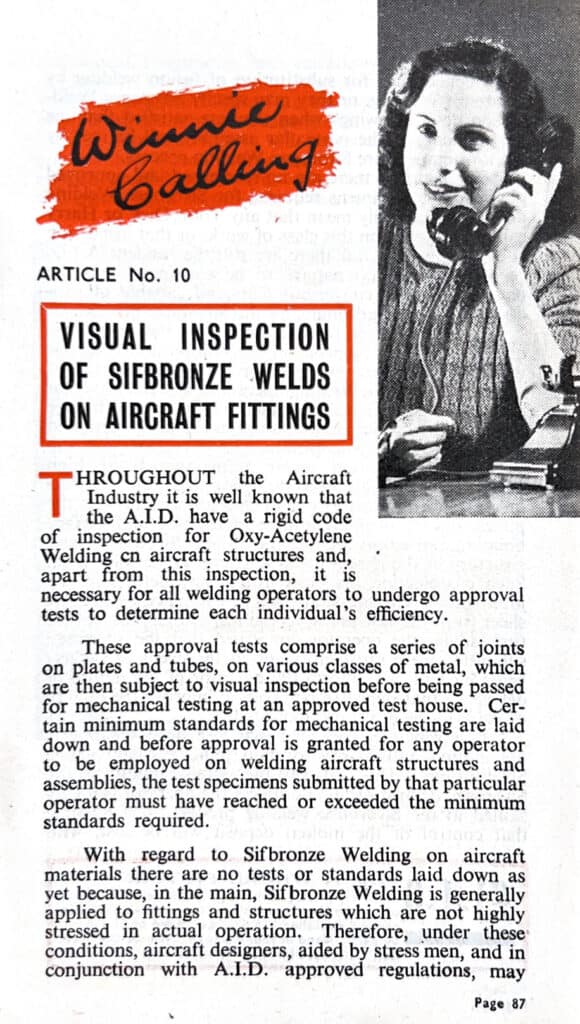
Visual Inspection and Quality Assurance
Given the lack of mechanical testing standards for Sifbronze Welds, visual inspection became a critical component of quality assurance. SIF developed detailed inspection protocols to identify any potential defects in the welds. These protocols included checking for uniformity, absence of cracks or voids, and proper alignment of the welded components.
To further ensure quality, SIF collaborated with aircraft manufacturers to perform periodic audits and reviews of the welding processes. This proactive approach allowed for continuous improvement and adaptation to new challenges, reinforcing the reliability of Sifbronze Welds in aircraft applications.
Historical Impact
The contributions of SIF to the aviation industry during this period were significant. By providing expert knowledge and rigorous inspection protocols for Sifbronze Welding, SIF helped maintain high standards of safety and reliability in aircraft construction. This support was particularly valuable in the context of the rapidly evolving aviation technology of the mid-20th century.
For SIF, founded in 1925, this involvement highlighted their longstanding commitment to innovation and excellence in welding. Their ability to adapt to the specific needs of the aviation industry and collaborate effectively with regulatory bodies and manufacturers underscored their pivotal role in advancing welding standards.
Conclusion
The story of SIF’s support for the aviation industry is a testament to the importance of expertise and collaboration in maintaining high standards of quality and safety. Through their work with Sifbronze Welding, SIF not only addressed the immediate challenges posed by the lack of formal testing standards but also laid the groundwork for future advancements in welding technology.
This historical case study illustrates how SIF’s contributions were instrumental in ensuring the reliability of aircraft components, thereby supporting the broader goals of the aviation industry. As we look back on this period, it’s clear that the legacy of SIF’s innovation and dedication to excellence continues to inspire and inform the field of industrial welding today.