Introduction
In the mid-20th century, Cunard embarked on an ambitious project to build a new 58,000-ton Atlantic liner that would set a new standard in maritime travel. This project, executed at John Brown’s Clydebank shipyard, aimed to create the largest and most advanced passenger ship in Britain since the Queen Elizabeth. Central to this project was the innovative use of aluminium for the ship’s superstructure, a task that required the expertise of Suffolk Iron Foundry (SIF), founded in 1925. This case study explores how SIF’s advanced welding technology and materials played a pivotal role in bringing Cunard’s vision to life.
The Challenge
Building such a colossal and advanced passenger liner necessitated replacing traditional steel components with aluminium to reduce weight and enhance performance. The construction required welding 1,200 tons of aluminium, replacing 2,000 tons of steel, and enabling the inclusion of an additional deck. The success of this ambitious project hinged on ensuring the strength and durability of the aluminium superstructure, which demanded high-quality welding materials and techniques.
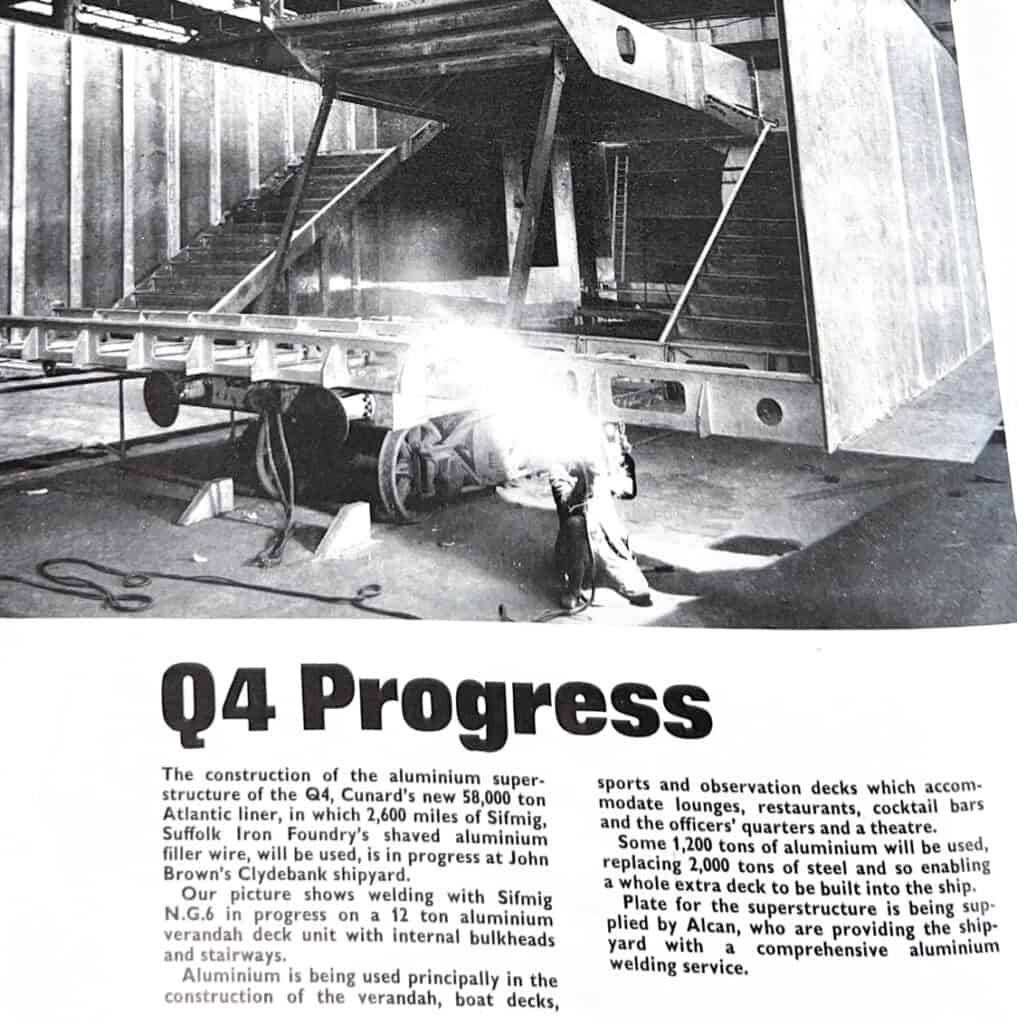
The Role of Suffolk Iron Foundry (SIF)
Founded in 1925, Suffolk Iron Foundry had established itself as a leader in welding technologies. For this project, SIF’s shaved aluminium welding filler wire, known as SIFMIG N.G.6, was selected. This 5 percent magnesium alloy provided the necessary strength and reliability for welding the extensive aluminium sections supplied by Alcan.
The choice of SIFMIG followed rigorous testing, leading to its approval by the Board of Trade for use in welding aluminium alloy to British Standards Specification 1477, NP 8 M. Each reel of SIFMIG N.G.6 was accompanied by a certificate confirming its properties, ensuring consistency and quality in the welding process.
Engineering Excellence in Action
The project featured welding with SIFMIG N.G.6 on a 12-ton aluminium verandah deck unit, complete with internal bulkheads and stairways. Aluminium was extensively used in constructing the verandah, boat decks, sports and observation decks, lounges, restaurants, cocktail bars, officers’ quarters, and a theatre.
SIFMIG N.G.6’s total requirement for the project was between 20 and 30 tons, translating to over 2,640 miles of welding wire. This extensive use underscored the importance of reliable welding materials and techniques in constructing the ship’s superstructure.
To ensure the highest standards in welding, Alcan Industries Ltd. and its research associate, Aluminium Laboratories Ltd., organized a seminar. Mr. Hector Constantine, Alcan’s chief welding demonstrator, discussed the finer points of SIFMIG welding with technical representatives from Cunard, John Brown & Co., Lloyds Register of Shipping, and the Board of Trade. This seminar ensured that the latest welding and fabricating techniques were employed in the construction.
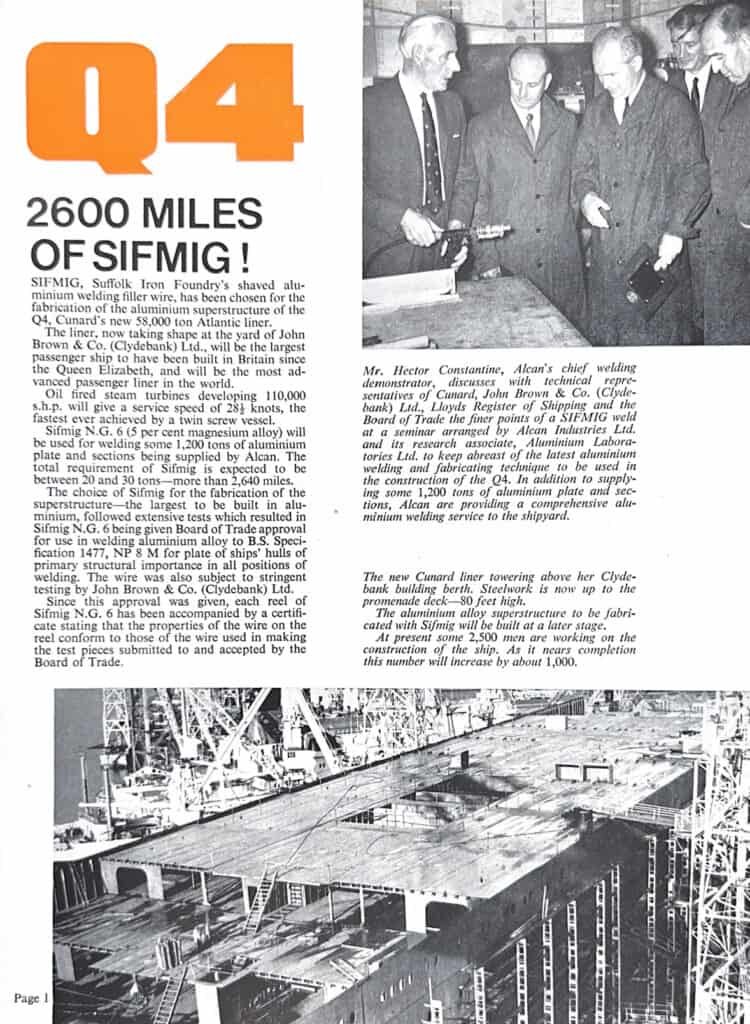
The Outcome
The construction of the liner’s aluminium superstructure progressed smoothly, with steelwork reaching up to the 80-foot-high promenade deck. At this stage, 2,500 workers were engaged in the construction, with an additional 1,000 expected as completion neared.
The use of 2,600 miles of SIFMIG aluminium welding filler wire was crucial to the project’s success. The advanced welding techniques and high-quality materials provided by SIF ensured the strength and reliability of the aluminium superstructure, contributing to the liner’s status as the most advanced passenger vessel in the world.
Legacy and Impact
The successful construction of Cunard’s new Atlantic liner demonstrated the transformative impact of innovative welding techniques and high-quality materials. Suffolk Iron Foundry’s SIFMIG aluminium welding filler wire was instrumental in ensuring the structural integrity and durability of the ship’s aluminium superstructure.
This historical case study highlights the importance of collaboration and technological advancement in maritime engineering. It underscores how strategic partnerships and the adoption of cutting-edge materials and techniques can lead to groundbreaking achievements in shipbuilding, setting new standards for the industry.
SIF’s contribution to Cunard’s landmark project not only exemplified their expertise in welding technology but also cemented their reputation as a key player in the evolution of maritime construction. The success of this project laid the groundwork for future innovations, ensuring that Cunard’s fleet remained at the forefront of luxury and technological advancement in passenger travel.
- Article Links –
- 180 years of sailing with Cunard – https://www.cunard.com/en-gb/cunard-stories/180-years-of-cunard
- Cunard Line History – https://www.cruisecritic.co.uk/articles/cunard-line-history