Introduction
In the world of aviation, few advancements have been as revolutionary as in-flight refuelling and the sophisticated ground equipment that supports these operations. Central to these developments was the meticulous work of Flight Refuelling Ltd., a pioneer in aerial refuelling technologies, and their collaboration with the Suffolk Iron Foundry (SIF). Founded in 1925, SIF’s expertise in advanced welding techniques played a pivotal role in this journey, particularly through their innovative use of Sifbronze.
The Early Days of In-Flight Refuelling
The 1930s saw the daring vision of Sir Alan Cobham take flight. His early experiments in in-flight refuelling were initially seen as circus stunts but soon evolved into a critical technology for extending the range and capabilities of military and civilian aircraft. These advancements were especially crucial during World War II and the Cold War era, where the ability to refuel mid-air provided strategic advantages.
The Need for Advanced Welding Techniques
As Flight Refuelling Ltd. pushed the boundaries of what was possible, the need for reliable, durable, and precise welding became evident. The traditional fusion welding methods, operating at high temperatures of around 1500°C, often led to localized distortion, scaling, and cracking in the weld-affected zones. These issues posed significant challenges in maintaining the integrity and performance of aircraft and ground equipment components.
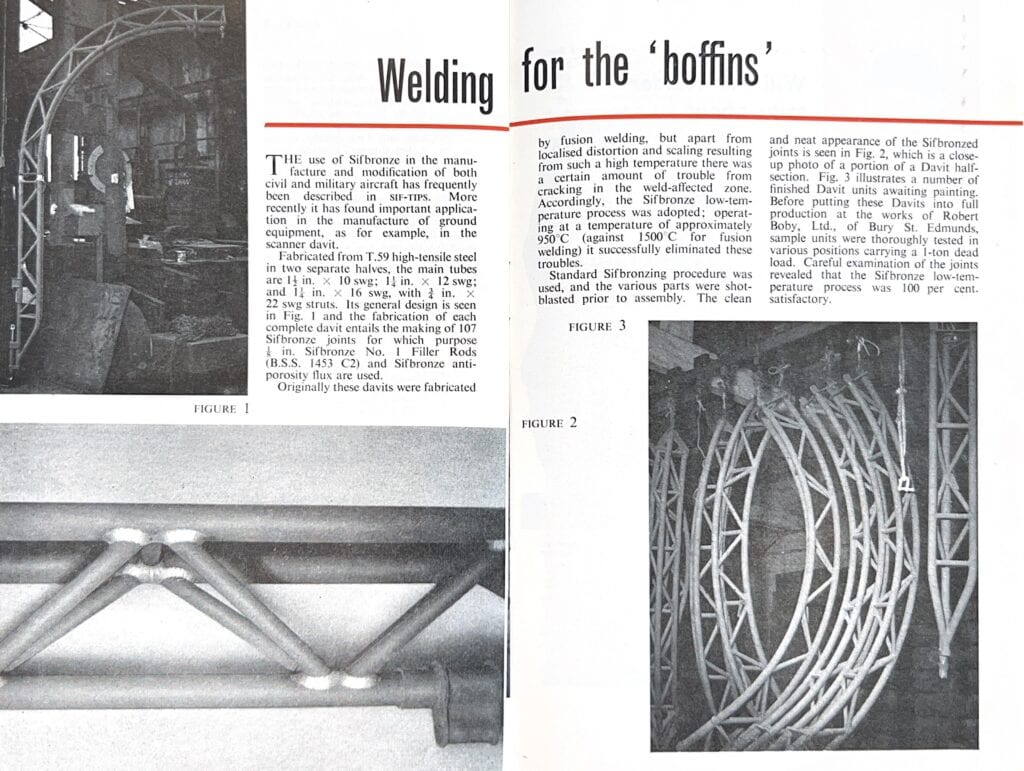
Enter Sifbronze
Suffolk Iron Foundry, with its rich history of metallurgical innovation, introduced Sifbronze – a low-temperature welding process operating at approximately 950°C. This technique was a game-changer, effectively eliminating the problems associated with high-temperature welding. The collaboration between Flight Refuelling Ltd. and SIF soon became a cornerstone of their success.
Case Study: The Scanner Davit
One of the notable applications of Sifbronze was in the fabrication of scanner davits for ground equipment. These davits, crucial for operations, were made from T.59 high-tensile steel. The process involved several steps to ensure the highest quality and durability:
- Design and Fabrication:
- The davits were designed in two halves, with main tubes of various specifications (1¼ in. × 10 swg; 1½ in. × 12 swg; and 1¾ in. × 16 swg) and struts (¾ in. × 22 swg).
- Each davit required 107 Sifbronze joints, utilizing Sifbronze No. 1 Filler Rods and anti-porosity flux.
- Challenges of Fusion Welding:
- Initial attempts at fabricating these davits using fusion welding resulted in significant issues due to high temperatures, such as localized distortion and cracking.
- Adoption of Sifbronze:
- By adopting the Sifbronze low-temperature process, these problems were effectively mitigated.
- Standard procedures included shot-blasting parts prior to assembly to ensure clean and neat joints.
- Quality Assurance:
- The finished davits underwent rigorous testing at the facilities of Robert Boby, Ltd., in Bury St. Edmunds.
- These tests involved placing the davits in various positions and subjecting them to a 1-ton dead load.
- The Sifbronze joints demonstrated exceptional performance, with a 100% satisfaction rate, confirming the reliability and strength of the low-temperature welding process.
Impact and Legacy
The success of the Sifbronze process had far-reaching implications. It not only ensured the durability and safety of critical components in aviation but also set new standards in the manufacturing of ground equipment. The clean, neat, and robust joints produced by Sifbronze became a hallmark of quality.
A Testament to Innovation and Collaboration
The story of Flight Refuelling Ltd. and Suffolk Iron Foundry is a testament to the power of innovation and collaboration. By leveraging the expertise of SIF and the revolutionary Sifbronze welding technique, Flight Refuelling Ltd. was able to overcome significant engineering challenges and achieve new heights in aviation technology.
Conclusion
As we look back at this historical collaboration, we celebrate the ingenuity and dedication of the engineers and metallurgists who made these advancements possible. The partnership between Flight Refuelling Ltd. and Suffolk Iron Foundry not only revolutionized in-flight refuelling but also left an indelible mark on the field of aviation engineering. Their legacy continues to inspire and set the standard for excellence in the industry.