Introduction
In the dark, dangerous depths of 19th and early 20th-century coal mines, the safety of miners was a paramount concern. Explosions caused by methane gas (fire-damp) were a constant threat. The invention of the safety lamp by Sir Humphrey Davy in 1815 marked a significant breakthrough, providing miners with a means to detect and mitigate the presence of hazardous gases. This case study explores the historical evolution of the safety lamp, highlighting how Suffolk Iron Foundry (SIF) played a critical role in advancing this vital technology.
The Challenge
Mining has always been fraught with dangers, but none were more feared than the explosive potential of methane gas. Sir Humphrey Davy’s invention of the “Davy’s Safety Lamp” offered a measure of protection by using a flame enclosed within a mesh screen to prevent the ignition of methane. However, the lamp had its limitations. If the air currents in the mine exceeded 5 feet per second, the flame could be driven through the mesh, potentially igniting the gas and causing an explosion.
As mining techniques and mine ventilation improved, air currents in mines could reach speeds of 20 to 30 feet per second. The original Davy’s Lamp was no longer sufficient to ensure the safety of miners. The industry needed a more reliable solution to keep pace with these advancements.
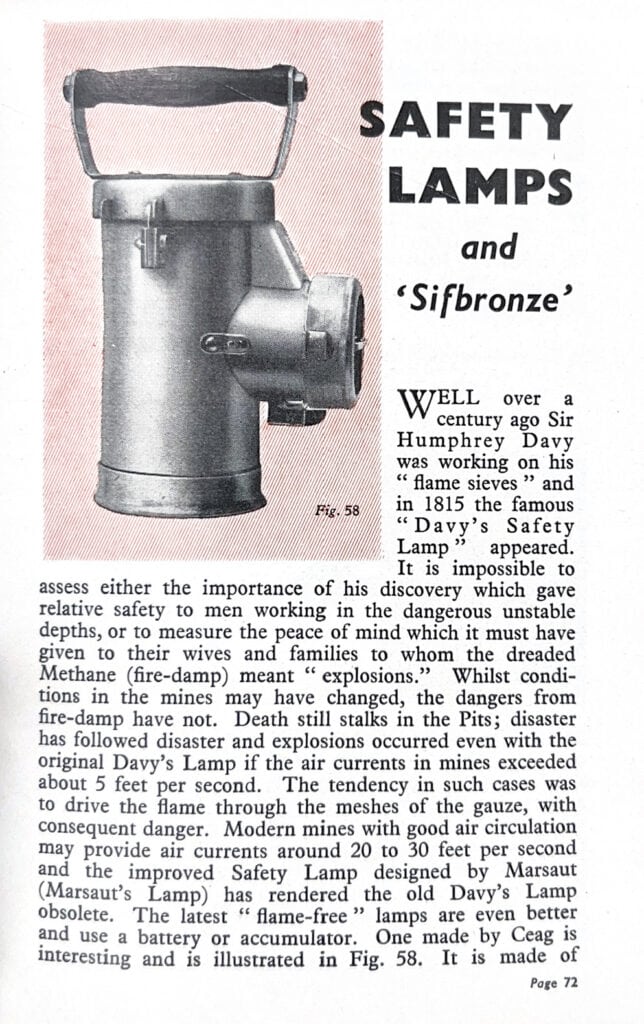
The Role of SIF
By the mid-20th century, new designs and technologies were being explored to enhance the safety and reliability of mining lamps. Among the leading innovators was Marsaut, who improved upon Davy’s design, and later, companies like Ceag introduced “flame-free” lamps powered by batteries or accumulators.
Suffolk Iron Foundry (SIF), established in 1935, became a crucial player in this evolution. Known for their expertise in metalworking and welding, SIF’s Sifbronze welding technology provided the necessary precision and durability required in the construction of modern safety lamps. Sifbronze welding was particularly effective in joining dissimilar metals, such as cast iron fittings to copper feed pipes, ensuring robust and reliable connections.
Engineering Excellence
The collaboration with SIF allowed for significant advancements in the design and manufacture of safety lamps. For instance, the improved Marsaut’s Lamp featured multiple gauzes and shields to better protect the flame from high air currents, significantly reducing the risk of ignition. SIF’s Sifbronze welding played a critical role in ensuring that these intricate components were securely and precisely joined, enhancing the overall safety and reliability of the lamp.
The next leap forward came with the development of flame-free lamps by companies like Ceag. These lamps utilized batteries or accumulators, eliminating the flame altogether and further reducing the risk of explosions. The manufacturing process for these modern lamps required high-quality welding to ensure the integrity of the electrical connections and the overall durability of the lamp in harsh mining environments. SIF’s advanced welding techniques provided the reliability needed for these crucial components.
Impact and Legacy
The continuous improvements in safety lamp technology, supported by SIF’s welding expertise, had a profound impact on the mining industry. The modern safety lamps were not only safer but also more efficient and easier to use, providing miners with greater peace of mind and reducing the incidence of deadly explosions.
The legacy of this collaboration is evident in the enhanced safety standards of the mining industry. The advancements in safety lamp technology, driven by the innovative use of Sifbronze welding, set new benchmarks for reliability and durability. These improvements helped to save countless lives and underscored the importance of ongoing innovation and collaboration in industrial safety.
Conclusion
The evolution of the safety lamp from Sir Humphrey Davy’s original design to the modern flame-free versions is a testament to the power of innovation and collaboration. Suffolk Iron Foundry’s (SIF) contribution, through their advanced Sifbronze welding technology, was instrumental in enhancing the safety and reliability of these vital devices.
This historical case study highlights the importance of precision engineering, meticulous manufacturing, and strategic partnerships in advancing safety technology. It showcases how SIF’s expertise supported the development of safety lamps that not only met the demands of modern mining but also significantly improved the safety and well-being of miners. The enduring legacy of these advancements continues to influence safety standards in the mining industry today.