Introduction
In the golden age of aviation, the 1950s and 60s, the race to develop safer, more reliable aircraft was in full throttle. Behind the scenes, one critical factor that played a significant role in this endeavor was the advancement of welding techniques. This case study explores how the Suffolk Iron Foundry (SIF), founded in 1925, supported and enhanced aircraft construction through their expertise in welding, particularly Oxy-Acetylene Welding, which was crucial for achieving the highest standards of precision and safety.
The Challenge
Aircraft manufacturing demands the utmost precision in every component, especially in welding. The Aircraft Inspection Department (A.I.D.) had stringent codes for Oxy-Acetylene Welding on aircraft structures. This process required welders to master correct blowpipe angles, proper feed rod angles, and the coordination of both hands to produce flawless welds. The challenge was not just achieving these standards but maintaining them consistently across all welding operations.
The SIF Solution
Recognizing the critical role of welding in aircraft construction, SIF dedicated their resources and expertise to support the aviation industry. They focused on developing advanced training programs and refining welding techniques to ensure that every weld met the rigorous standards set by the A.I.D.
Implementation and Innovations
Training and Mastery: SIF understood that mastering welding techniques required more than just basic training. They established intensive training programs where welders practiced the correct angles of blowpipe and feed rod repeatedly until they achieved almost automatic precision. This relentless practice was crucial for developing the muscle memory needed to perform high-quality welds consistently.
Advanced Techniques: Incorrect angles in either the blowpipe or feed rod could severely compromise the quality of the weld, particularly in circumferential seam welds on tubular structures. SIF’s training emphasized the importance of starting the weld at the lowest point on static tubular members and finishing at the highest point in a horizontal position. This approach minimized the risk of misdirected angles and ensured uniformity in the weld.
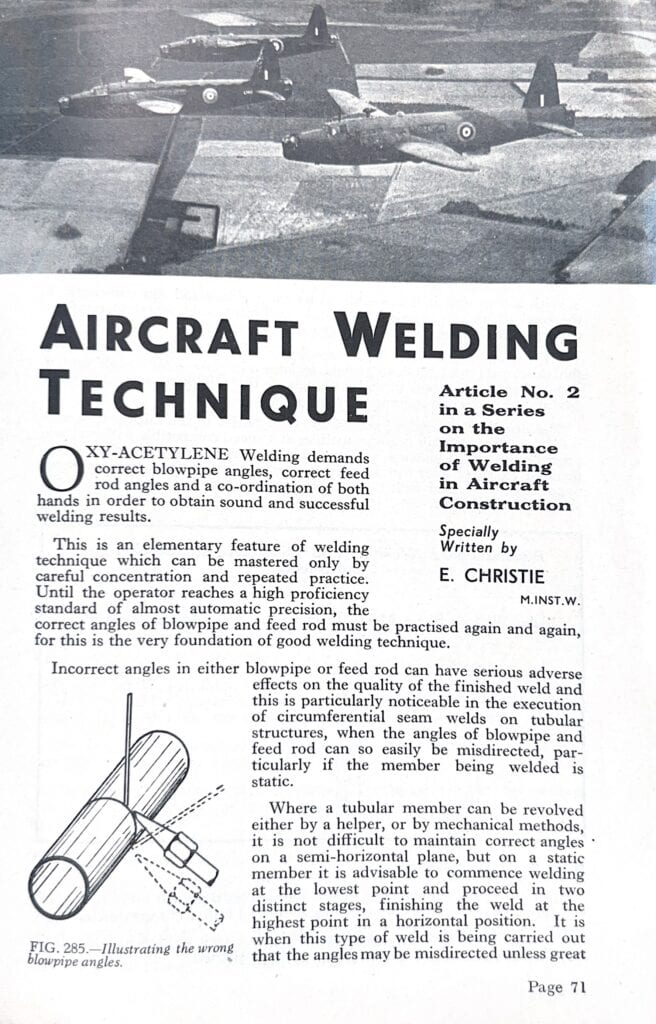
Mechanical Assistance: To further enhance accuracy, SIF introduced mechanical methods to aid welders. Where possible, tubular members were revolved using mechanical devices, allowing welders to maintain correct angles more easily. This innovation significantly improved the quality of circumferential seam welds, which are critical for the integrity of aircraft structures.
Quality Assurance: SIF implemented a rigorous quality assurance process. Each weld was subjected to visual inspection and mechanical testing to ensure it met the required standards. This process not only identified any defects but also provided valuable feedback to welders, helping them continually improve their techniques.
Historical Impact
SIF’s contributions had a profound impact on the aviation industry. By enhancing welding techniques and ensuring rigorous training and quality control, they helped elevate the standards of aircraft construction. The reliability and safety of aircraft components improved significantly, contributing to the overall advancement of aviation technology.
For SIF, founded in 1925, this period marked a significant chapter in their legacy of innovation and excellence. Their commitment to precision and quality in welding not only supported the aviation industry but also set new benchmarks for welding practices in other sectors.
Conclusion
The story of SIF’s involvement in aircraft welding is a testament to the importance of precision and expertise in industrial processes. Their dedication to improving welding standards played a crucial role in the evolution of aircraft technology, ensuring that every component met the highest standards of safety and reliability.
This historical case study highlights the enduring impact of SIF’s contributions. As we reflect on this era, it is clear that their innovations and commitment to excellence have left a lasting legacy in the field of welding and beyond. The lessons learned from their approach continue to inspire and inform best practices in industrial welding today, reminding us of the critical role that precision and dedication play in achieving technological progress.