Introduction
In the bustling industrial landscape of mid-20th century Britain, the Avonmouth Docks played a pivotal role in facilitating trade and transport. These docks were the lifeline for road and rail traffic, connecting key economic hubs. In this historical context, a sudden breakdown of a critical swing bridge at the docks presented a major crisis. The engineers at Magnodïcs (Bristol) Ltd., renowned for their expertise in structural repairs, were called to action. This case study explores how Magnodïcs, with the vital support of Suffolk Iron Foundry (SIF), addressed this urgent challenge with remarkable efficiency and skill.
The Challenge
One fateful day, Magnodïcs received an emergency call from the Engineers Department at Avonmouth Docks. A roller bracket, crucial for the operation of a swing bridge that carried both road and rail traffic, had been smashed to pieces. With the bridge stuck in the open position, at least a third of the docks was rendered inaccessible, disrupting operations severely. Replacement castings would take months to procure, necessitating an immediate and effective repair solution.
The Swing Bridge and its Counter Balance, with a combined weight of approximately 700 tons, exerted about 500 tons of this weight on the roller brackets. The critical task was to repair these brackets swiftly and ensure they could bear the immense load during the bridge’s opening and closing operations.
The Rapid Response
The situation demanded not just expertise but also speed. Upon inspection, Magnodïcs executives Messrs. L. and W. Adkins decided to transport the broken castings, each weighing 10 cwts, to their works for immediate repair. The process was far from straightforward, as the numerous broken pieces needed precise fitting and welding to ensure alignment with the main structure’s bolt holes.
Suffolk Iron Foundry (SIF), founded in 1925 and known for their advanced welding materials and techniques, became an essential part of this operation. SIF’s cast-iron filler rods were chosen for the repair due to their superior strength and reliability. These materials ensured that the welds would be robust and durable, critical for the heavy-duty application of the swing bridge.
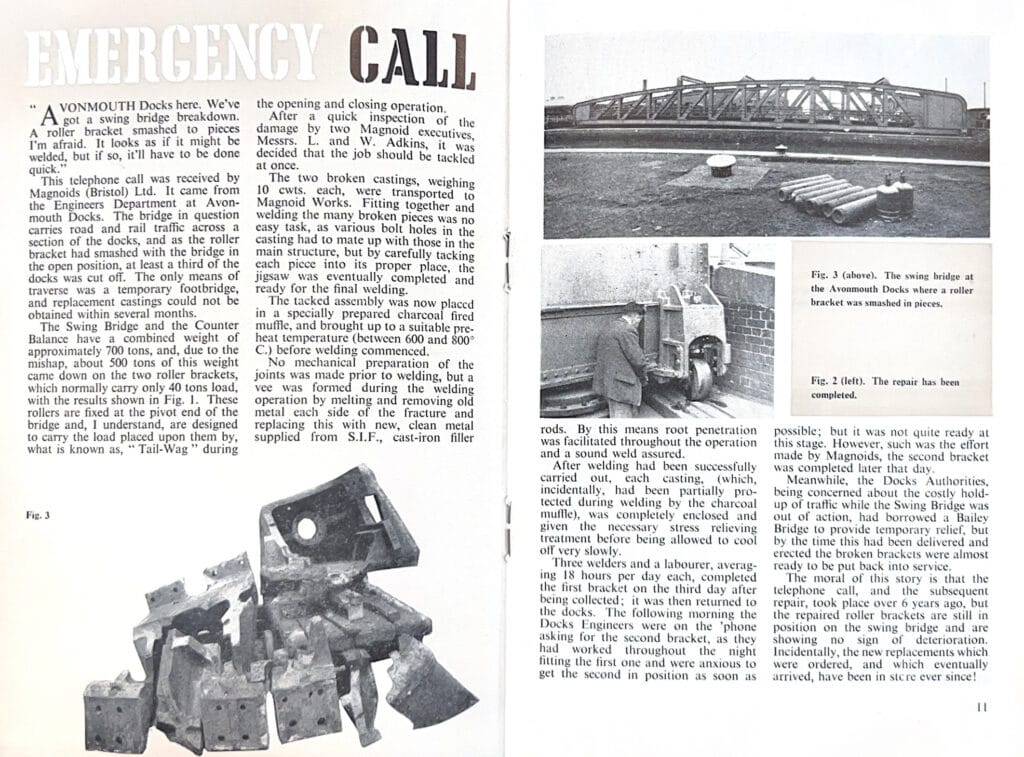
Engineering Excellence
The broken castings were carefully tacked together, creating a complex jigsaw of metal pieces that were meticulously aligned. This assembly was then placed in a specially prepared charcoal-fired muffle and pre-heated to between 600 and 800°C. This pre-heating process was crucial for achieving a sound weld.
Using SIF’s cast-iron filler rods, the welders at Magnodïcs formed a vee during the welding process by melting and removing old metal from the fracture sides and replacing it with new, clean metal. This method facilitated deep root penetration and ensured a strong weld throughout the operation.
The welding process was rigorous. Each casting was partially protected during welding to maintain structural integrity. After welding, the castings underwent stress-relieving treatment to ensure they could handle the immense operational stresses they would face.
The Outcome
The dedicated team of three welders and a laborer worked around the clock, averaging 18-hour days. The first bracket was completed and returned to the docks within three days. The docks engineers, working tirelessly, fitted the first bracket overnight and eagerly awaited the second, which was completed shortly thereafter.
The repaired roller brackets were installed successfully, allowing the swing bridge to resume operation much sooner than anticipated. Remarkably, six years later, these repaired brackets were still in service, showing no signs of deterioration, while the replacement brackets remained unused in storage.
Conclusion
The emergency repair at Avonmouth Docks stands as a testament to the effectiveness of rapid, skilled engineering and the importance of high-quality materials. Magnodïcs’ swift response and meticulous work, supported by Suffolk Iron Foundry’s superior cast-iron filler rods, ensured the continued operation of a critical piece of infrastructure.
This historical case study highlights the critical role of collaboration and innovation in overcoming engineering challenges. It showcases how SIF’s advanced materials contributed to a successful and durable repair, underscoring the lasting impact of quality craftsmanship and expert execution in maintaining vital industrial operations.