Introduction
In the annals of aviation history, the development of in-flight refuelling stands as one of the most transformative innovations. Spearheaded by Sir Alan Cobham in the early 1930s, what began as an air-circus stunt soon evolved into a crucial technological advancement, redefining the boundaries of aerial capabilities. Central to this revolution was the collaboration between Flight Refuelling Ltd. and Suffolk Iron Foundry (SIF), established in 1925, whose expertise in advanced welding techniques and material sciences played a pivotal role.
The Challenge
As aviation technology advanced, the demand for extended flight capabilities grew. Traditional refuelling methods were inadequate for the needs of modern aircraft, especially during long-range missions and military operations. The solution lay in developing reliable, efficient, and safe in-flight refuelling systems. This task required precise engineering and robust materials to withstand the extreme conditions of high-altitude operations.
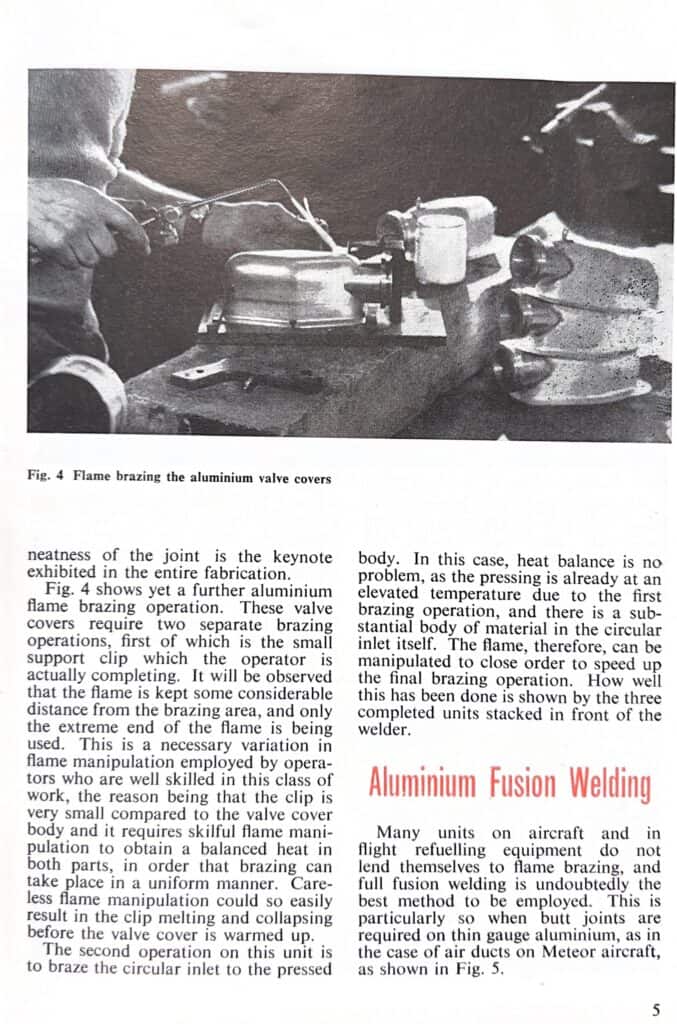
Enter Suffolk Iron Foundry (SIF)
Founded in 1925, SIF had a rich history of metallurgical innovation and engineering excellence. Their expertise in advanced welding techniques, particularly with challenging materials like aluminium and mild steel, made them the ideal partner for Flight Refuelling Ltd. SIF’s commitment to quality and precision aligned perfectly with the stringent requirements of aviation engineering.
The Collaboration
Flight Refuelling Ltd. and SIF embarked on a collaborative journey to develop the next generation of in-flight refuelling systems. The key to their success lay in the innovative use of Sifbronze welding techniques, which were crucial in fabricating the complex components required for the refuelling systems.
- Flame Brazing Aluminium Valve Covers:
- Technique: The process involved two separate brazing operations. The first step required precision in brazing small support clips to the valve cover bodies. Skilled operators used controlled flame manipulation to ensure uniform heating, preventing the clips from melting or collapsing.
- Outcome: The resulting valve covers were robust and reliable, capable of withstanding the rigours of high-altitude refuelling operations.
- Mild Steel Fusion Welding for Flare Carrier Tubes:
- Technique: This process involved filling breather holes in the flare carrier tubes using mild steel fusion welding. The low heat input of Sifbronze welding preserved the structural integrity of the tubes, preventing distortion and scaling.
- Outcome: The breather holes allowed gases to escape during welding, avoiding pressure build-up and ensuring the safety of both the equipment and the operators.
- Ground Reception Couplings:
- Technique: SIF’s welding operations also extended to fabricating ground reception couplings. Using jig tacking and Sifbronze welding, SIF produced strong and robust handles required for these couplings.
- Outcome: These couplings were essential for ground operations, enhancing the efficiency and safety of the refuelling process.
Historical Impact
The partnership between Flight Refuelling Ltd. and SIF culminated in the successful development and deployment of in-flight refuelling systems. These systems extended the operational range of aircraft, allowing for longer missions without the need for frequent landings. This advancement proved invaluable during World War II and the subsequent Cold War period, providing strategic advantages to allied forces.
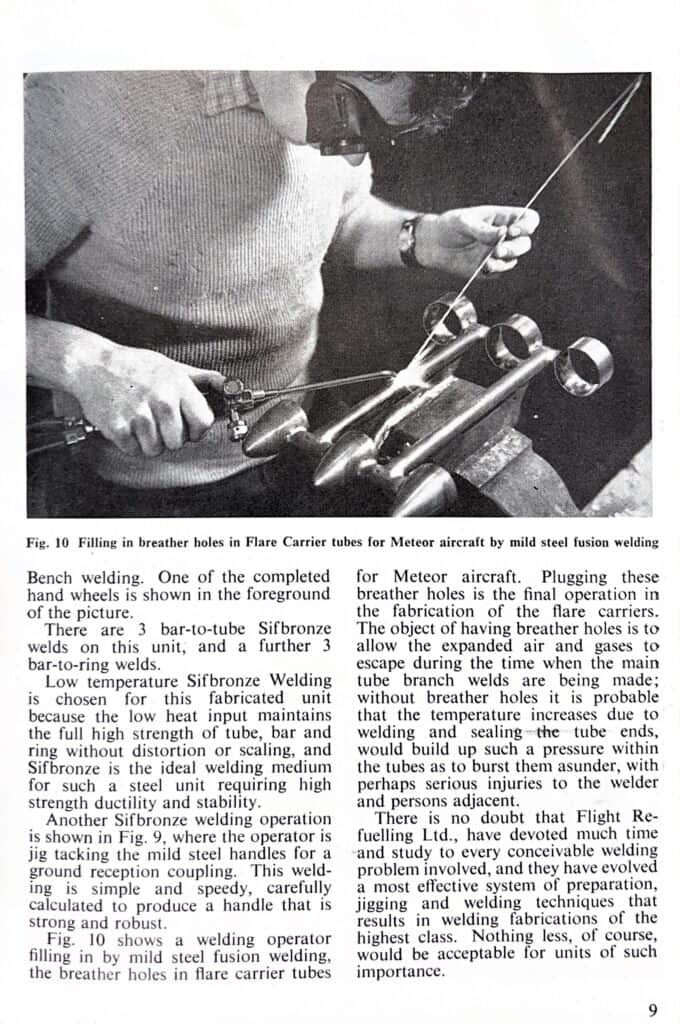
Legacy
SIF’s contributions to aviation extended beyond their technical expertise. Their commitment to quality, innovation, and precision set new standards in the industry. The techniques and materials developed during this collaboration laid the groundwork for future advancements in aerospace engineering.
Conclusion
The story of Flight Refuelling Ltd. and Suffolk Iron Foundry is a testament to the power of collaboration and innovation. By leveraging SIF’s metallurgical expertise and pioneering welding techniques, Flight Refuelling Ltd. achieved a breakthrough that revolutionized aviation. This case study not only highlights a significant technological achievement but also underscores the enduring impact of strategic partnerships in driving progress.
As we look back at this historical collaboration, we celebrate the ingenuity and dedication of the engineers and metallurgists who made in-flight refuelling a reality, forever changing the landscape of aviation.
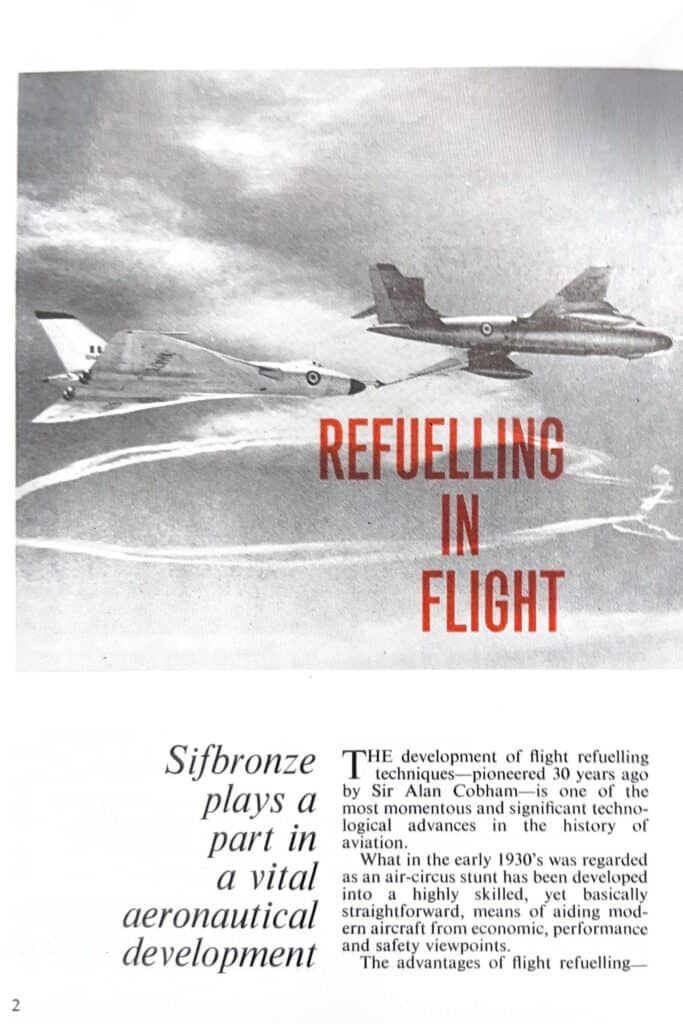