Introduction
In the 1970s, the shipbuilding industry was on the cusp of a revolution. Innovations in materials and construction techniques were transforming the capabilities and performance of marine vessels. A prime example of this innovation was the construction of the first all-aluminium hydrofoil by Vosper Thornycroft Ltd. This ambitious project, undertaken at the company’s Portchester Yard, was significantly supported by Suffolk Iron Foundry (SIF), founded in 1925. This case study explores how SIF’s advanced aluminium filler wire, SIFMIG NG6, played a crucial role in the success of this groundbreaking hydrofoil.
The Challenge
Vosper Thornycroft, a company renowned for its high-speed patrol vessels and corvettes, merged with John I. Thornycroft & Co. Ltd. in 1966. This merger combined their expertise and bolstered their reputation for quality and progressive design. The new entity continued to innovate, forming a hovercraft division and securing an agreement with Supramar A.G. of Lucerne to build hydrofoil craft based on Swiss designs.
The project at hand was a fast passenger craft for the Far East Hydrofoil Co. Ltd. of Hong Kong, valued at nearly £5,000,000. The hydrofoil, with an overall length of 98 feet and a fully loaded displacement of 77 tons, was designed to carry 135 passengers at speeds up to 40 knots. Achieving such performance required a lightweight yet strong construction, making aluminium/magnesium alloy the material of choice. The challenge was to weld this material effectively to ensure structural integrity and performance.
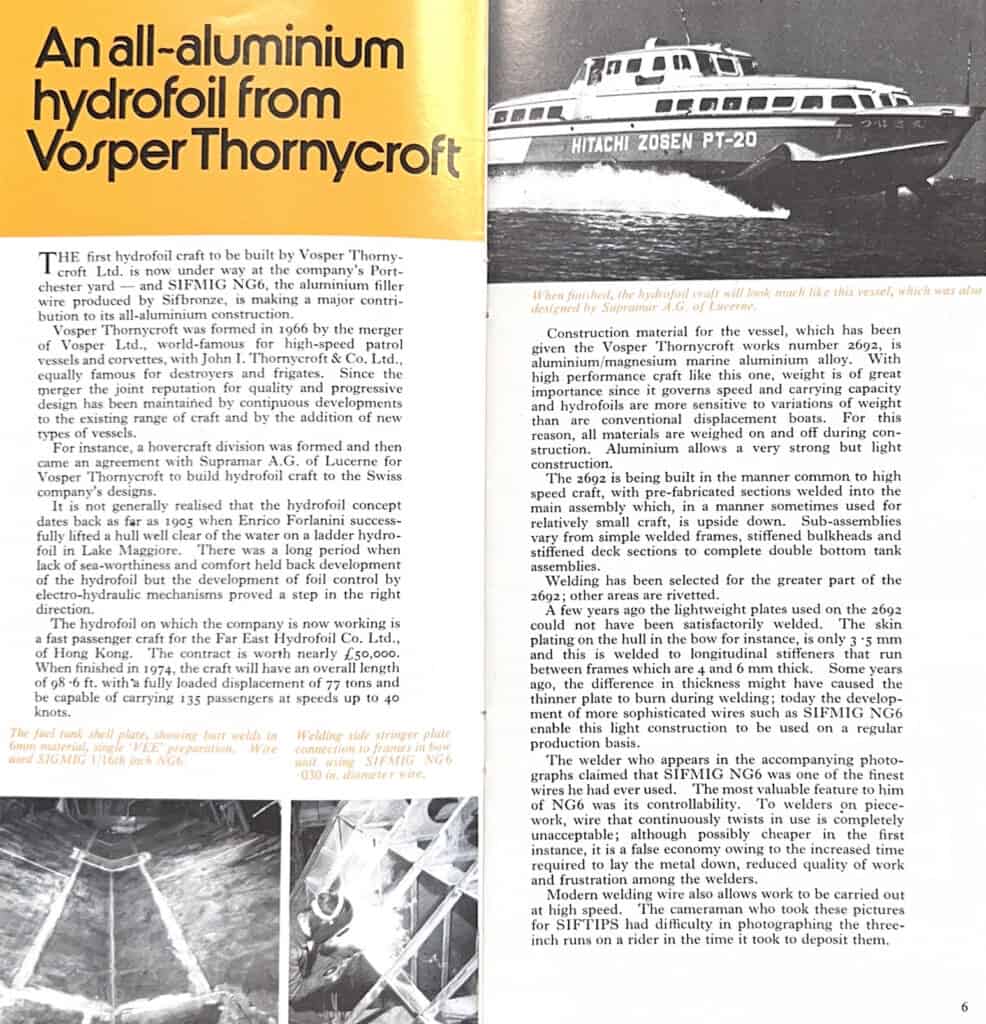
The Role of Suffolk Iron Foundry (SIF)
Suffolk Iron Foundry, established in 1925, was a pioneer in welding technology. For this project, their SIFMIG NG6 aluminium filler wire was selected. This wire, a 5 percent magnesium alloy, was essential for welding the hydrofoil’s aluminium components. The choice of SIFMIG NG6 followed extensive testing and approval by marine and shipping authorities.
The properties of SIFMIG NG6 made it ideal for this project:
- Strength and Durability: The filler wire provided strong, reliable welds essential for the hydrofoil’s performance.
- Controllability: Welders appreciated the wire’s controllability, which was crucial for maintaining high welding speeds without sacrificing quality.
- Adaptability: The wire could handle variations in material thickness, a common challenge in constructing high-speed craft.
Engineering Excellence
The hydrofoil, designated as works number 2692, was built using pre-fabricated sections welded into the main assembly. This method, common for high-speed craft, often involved working with the assembly upside down to facilitate construction. Welding was the primary method for joining the various components, including simple welded frames, stiffened bulkheads, and double bottom tank assemblies.
A notable aspect of the construction was the welding of lightweight plates. The skin plating on the hull in the bow, only 3/16 inch thick, was welded to longitudinal stiffeners that were 4 to 6 mm thick. Previously, such differences in thickness posed a risk of burning the thinner plate during welding. However, the sophisticated properties of SIFMIG NG6 allowed for precise, high-quality welds, making such construction feasible.
The Outcome
The construction of the hydrofoil progressed efficiently, with SIFMIG NG6 enabling high-speed, high-quality welding. The resulting vessel, completed in 1974, met all performance expectations, demonstrating speeds up to 40 knots and comfortably carrying 135 passengers.
The project underscored the critical role of advanced welding materials and techniques in modern shipbuilding. SIF’s contribution through their SIFMIG NG6 filler wire was instrumental in achieving the project’s ambitious goals. The hydrofoil not only showcased Vosper Thornycroft’s engineering prowess but also highlighted the importance of strategic partnerships in pushing the boundaries of marine technology.
Legacy and Impact
The successful construction of the all-aluminium hydrofoil marked a significant milestone in marine engineering. It demonstrated the potential of lightweight materials in enhancing vessel performance and set new standards for future projects. SIF’s role in this project exemplified their commitment to innovation and quality, solidifying their position as a key player in the welding industry.
This historical case study highlights the transformative impact of collaboration and technological advancement. It showcases how Suffolk Iron Foundry’s expertise and innovative materials contributed to the success of a pioneering project, setting a precedent for future advancements in the marine industry. The legacy of this hydrofoil continues to influence modern shipbuilding, reflecting the enduring value of innovation and excellence in engineering.