Introduction
The mid-20th century marked an era of significant advancements in rail transportation. Among these innovations was the development of the largest aluminium bogie rail tanker in Europe, a marvel of engineering designed to optimize payload capacity and efficiency. This case study explores the creation of this giant tanker and highlights the pivotal support provided by Suffolk Iron Foundry (SIF), founded in 1925, which played a crucial role in its construction.
The Vision: Lightweight and Efficient
In the 1960s, Alcan Industries Ltd. embarked on an ambitious project to design an aluminium tanker for Esso Petroleum Co. Ltd. The goal was to leverage the weight-saving potential of aluminium to increase the payload capacity of rail tankers. This innovative approach promised a 15% increase in payload capacity compared to the best two-axled steel tankers in service.
Suffolk Iron Foundry’s Crucial Support
Suffolk Iron Foundry (SIF) was already well-known for its expertise in metallurgy and welding materials. Their involvement in this project was critical, particularly in providing high-quality MIG welding materials and technical expertise. SIF’s contributions ensured that the tanker’s construction met the highest standards of durability and performance.
Engineering the Giant Aluminium Tanker
The 60 ft. long aluminium tanker, weighing 80 tons with a capacity of 20,000 gallons, was designed to exploit aluminium’s lightweight properties. This design allowed for a significant increase in payload capacity per train, optimizing the efficiency of transporting petroleum products across Europe.
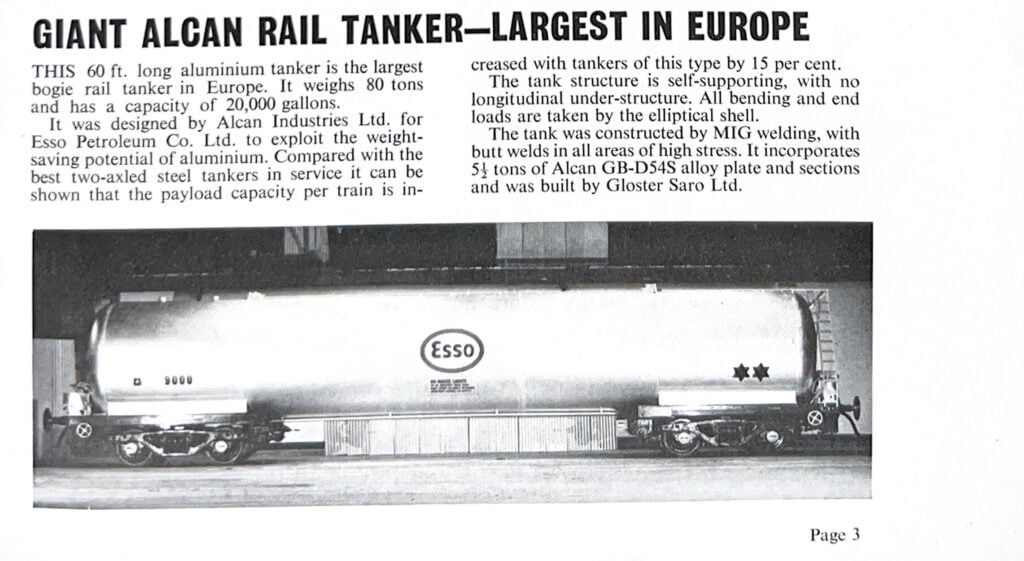
Key Features:
- Self-Supporting Structure: The tank’s structure was self-supporting, with no longitudinal under-structure. The elliptical shell design managed all bending and end loads, providing structural integrity and stability.
- MIG Welding: The tank was constructed using MIG welding, with butt welds in all high-stress areas. This technique, supported by SIF’s superior welding materials, ensured strong and reliable joints.
- Materials: The construction utilized 5.5 tons of Alcan GB-D54S alloy plate and sections. SIF’s high-quality MIG welding materials were crucial in welding these aluminium alloys effectively.
Construction by Gloster Saro Ltd.
The tanker’s construction was entrusted to Gloster Saro Ltd., a company renowned for its engineering prowess. With SIF’s support, Gloster Saro Ltd. successfully built the tanker, ensuring it met all design specifications and performance criteria.
Construction Process:
- Welding Expertise: The use of SIF’s MIG welding materials facilitated the creation of butt welds that could withstand high stress, ensuring the tanker’s durability.
- Precision and Quality: The meticulous construction process, supported by SIF’s technical expertise, ensured that every weld was executed with precision, contributing to the overall quality of the tanker.
The Impact of Innovation
The completion of Europe’s largest aluminium tanker marked a significant milestone in rail transportation. The lightweight and efficient design, made possible by the use of aluminium and advanced welding techniques, set new standards for the industry.
Benefits:
- Increased Payload Capacity: The innovative design allowed for a 15% increase in payload capacity per train, enhancing the efficiency of petroleum transport.
- Durability and Reliability: The use of high-quality materials and precision welding ensured that the tanker could withstand the rigors of rail transport.
Conclusion
The collaboration between Alcan Industries Ltd., Esso Petroleum Co. Ltd., Gloster Saro Ltd., and Suffolk Iron Foundry (SIF) exemplifies the power of innovation and expertise in achieving engineering excellence. SIF’s contributions, particularly in providing superior welding materials and technical support, were instrumental in the successful construction of Europe’s largest aluminium tanker.
This case study highlights the importance of collaboration and quality materials in advancing transportation technology. The legacy of this project continues to inspire modern engineering practices, reflecting a commitment to innovation and excellence that remains as relevant today as it was in the mid-20th century.
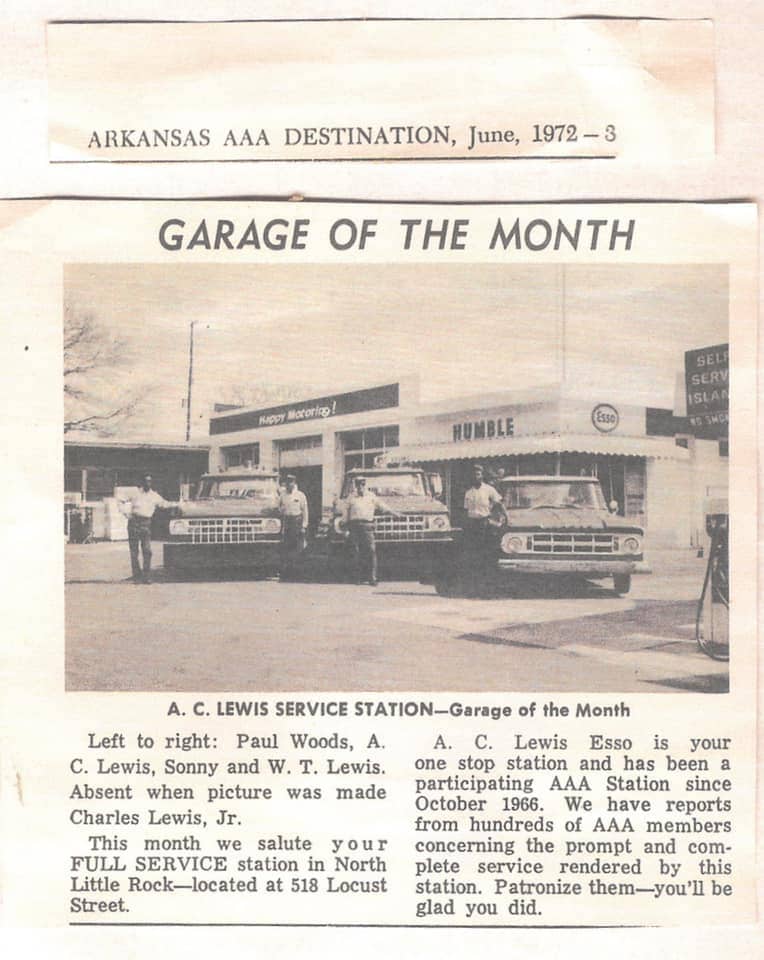
- References –
- Esso Garage of the Year Ad – https://www.facebook.com/photo.php?fbid=1076633102826396&id=298617247294656&set=a.519882938501418
- Article Links –
- History of Esso in the UK – https://www.exxonmobil.co.uk/company/overview/about-us/history-of-esso-in-the-uk
- Our History – https://www.esso.ca/en-ca/our-history
- Esso a rich history in the UK – https://www.fleetmaxxsolutions.co.uk/news/esso-a-rich-history-in-the-uk/