Introduction
In the bustling industrial heartland of Bradford, Yorkshire, a remarkable transformation was taking place in the 1960s and 70s. Yorkshire Engineering Co. Ltd., established in 1949, was at the forefront of this change, manufacturing some of the largest and most efficient road tankers in the country. This case study delves into the historical partnership between Yorkshire Engineering and the Suffolk Iron Foundry (SIF), founded in 1925, which played a crucial role in revolutionizing tanker construction through innovative welding techniques and materials.
The Challenge
As urbanization and industrial activities increased, so did the demand for efficient and reliable transportation of liquids. Traditional steel tankers, while robust, were heavy and limited in their payload capacity. Yorkshire Engineering faced the challenge of increasing the efficiency and capacity of their road tankers without compromising on strength and durability.
The Aluminum Advantage
In response to these challenges, Yorkshire Engineering began exploring the use of aluminum for their tankers. Aluminum’s lighter weight compared to steel meant that tankers could carry more liquid per trip, significantly enhancing efficiency. However, working with aluminum required specialized welding techniques and materials.
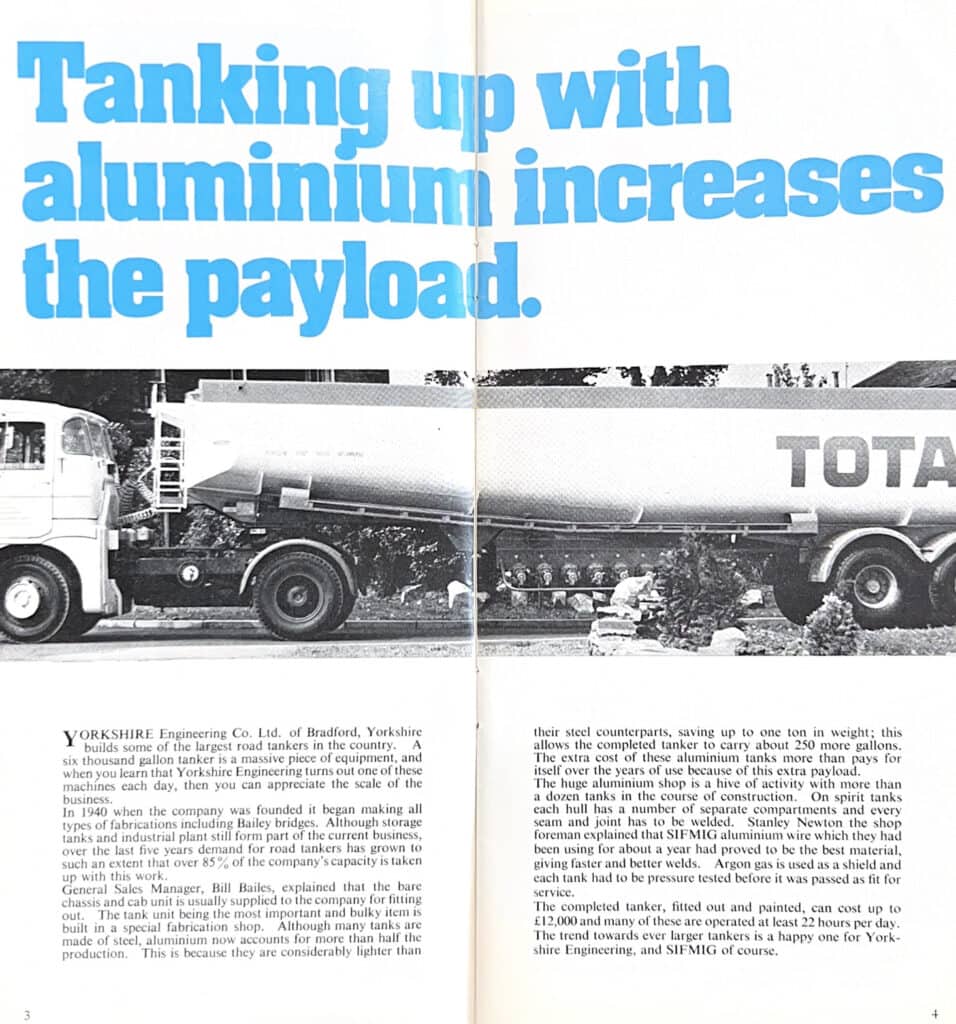
The SIF Solution
SIF, with their extensive experience in welding technology, provided the perfect solution. They introduced Yorkshire Engineering to SIFMIG aluminum wire, which proved to be the best material for welding aluminum tanks. This wire allowed for faster and better welds, essential for maintaining the structural integrity of the tankers under heavy loads.
Implementation and Innovations
The production process at Yorkshire Engineering was a hive of activity. The fabrication shop, dedicated to building the tank units, saw more than a dozen tanks under construction at any given time. Each hull, equipped with multiple compartments, required precise welding of every seam and joint using an argon shield to prevent oxidation and ensure strong bonds.
Bill Bailes, General Sales Manager at Yorkshire Engineering, explained the shift: “Although many tanks are made of steel, aluminum now accounts for more than half the production. This is because they are considerably lighter than their steel counterparts, saving up to one ton in weight. This allows the completed tanker to carry about 250 more gallons. The extra cost of these aluminum tanks more than pays for itself over the years of use because of this extra payload.”
Stanley Newton, the shop foreman, praised the SIFMIG aluminum wire: “We’ve been using SIFMIG aluminum wire for about a year, and it has proven to be the best material. It gives us faster and better welds, which are crucial for the durability of these tanks.”
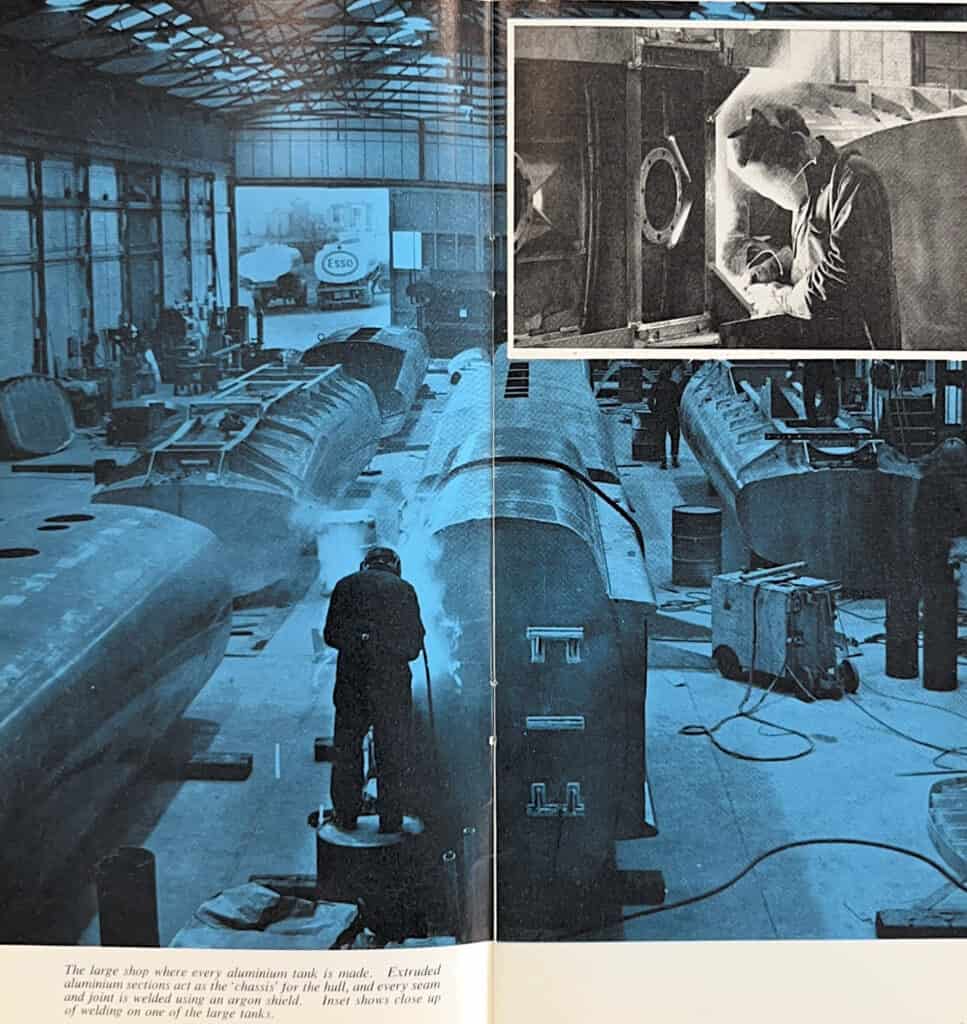
Historical Impact
The partnership between Yorkshire Engineering and SIF had a profound impact on the tanker industry. The aluminum tankers, costing up to £12,000 each, quickly became a favorite among local authorities and industrial users. They were not only more efficient but also demonstrated exceptional durability, operating at least 22 hours per day and significantly reducing transportation costs.
SIF’s contributions were instrumental in this success. Their expertise in welding and materials provided Yorkshire Engineering with the tools needed to innovate and stay ahead of the competition. Founded in 1925, SIF’s legacy of innovation and excellence was further cemented through this collaboration.
Conclusion
The story of Yorkshire Engineering and SIF is a testament to the power of innovation and collaboration. By embracing aluminum and leveraging advanced welding techniques, they transformed the road tanker industry, setting new standards for efficiency and reliability. This historical partnership showcases how two companies, through shared vision and expertise, can achieve remarkable success and leave a lasting impact on their industry.
As we look back on this era, it’s clear that the collaboration between Yorkshire Engineering and SIF not only met the challenges of their time but also paved the way for future advancements in industrial manufacturing and transportation. This case study serves as an inspiring example of how ingenuity and teamwork can drive progress and create solutions that stand the test of time.