Introduction
In the mid-20th century, the maritime industry witnessed a groundbreaking shift in the materials used for shipbuilding and storage solutions. One remarkable innovation was the use of aluminium for constructing large storage tanks. This case study explores the historical development of these aluminium tanks by Gloster Saro Ltd., highlighting how Suffolk Iron Foundry (SIF), founded in 1925, provided crucial support to this pioneering endeavor.
The Rise of Aluminium in Maritime Engineering
By the 1960s, aluminium had proven its worth in various industrial applications due to its excellent strength-to-weight ratio and resistance to corrosion. Companies like Gloster Saro Ltd. began exploring aluminium’s potential for building large storage tanks designed to carry liquid ethylene. This shift promised to enhance the efficiency and safety of transporting hazardous materials by sea.
Gloster Saro Ltd.’s Aluminium Tanks
Gloster Saro Ltd., based in Anglesey, undertook the ambitious project of constructing two massive aluminium tanks. Each tank measured 87 feet in length, 27 feet in width, and 17 feet in depth, weighing approximately 46 tons. These tanks were designed to carry liquid ethylene in specially built ships, a testament to the innovative spirit of the era.
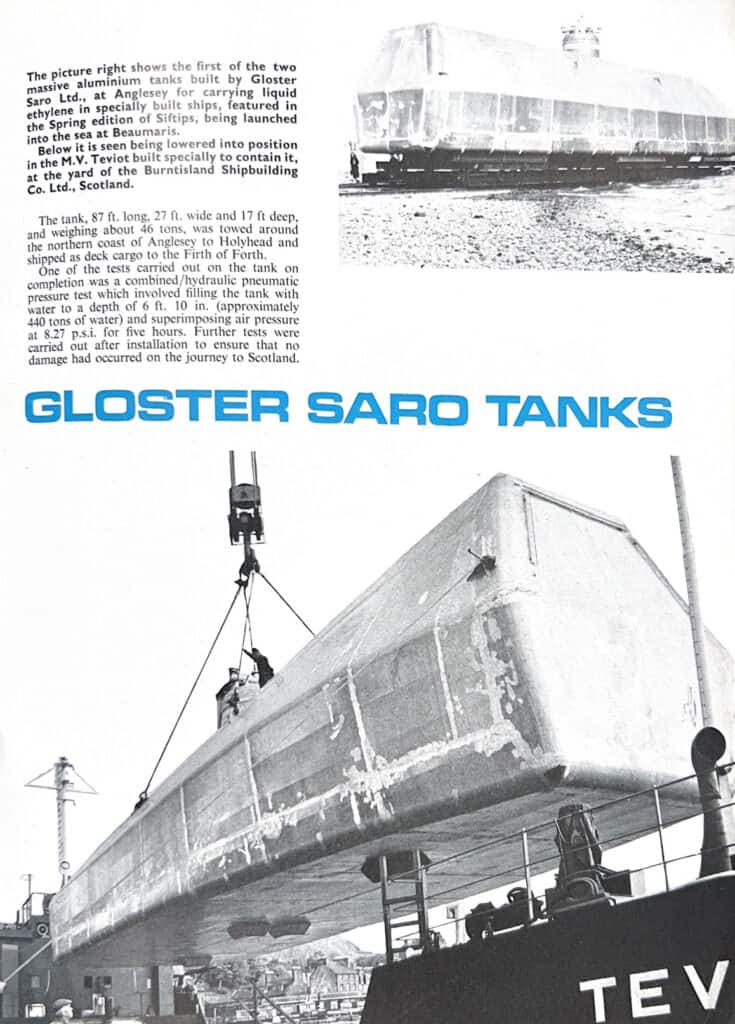
Suffolk Iron Foundry’s Crucial Support
While Suffolk Iron Foundry (SIF) had established itself as a leading provider of high-quality cast iron and metalworking solutions, their expertise extended to supporting groundbreaking projects in maritime engineering. SIF played a pivotal role in supplying the specialised SIFMIG aluminium filler wire used in the welding of these tanks. This wire was essential for ensuring the structural integrity and reliability of the tanks, given the demanding conditions they would face at sea.
Transport and Rigorous Testing
The journey of these aluminium tanks from Gloster Saro’s facility to their final destination was a feat in itself. The tanks were transported around the northern coast of Anglesey to Holyhead and then shipped as deck cargo to the Firth of Forth. Upon completion, the tanks underwent stringent testing to ensure their safety and functionality.
One notable test was a combined hydraulic and pneumatic pressure test. This involved filling the tanks with water to a depth of 6 feet 10 inches, equivalent to approximately 440 tons of water, and applying an air pressure of 8.27 p.s.i. for five hours. Further tests were conducted after installation to confirm that no damage had occurred during the journey to Scotland.
The Impact on the Maritime Industry
The successful construction and deployment of these aluminium tanks marked a significant milestone in maritime engineering. They demonstrated the feasibility and advantages of using aluminium for large-scale storage solutions, paving the way for more widespread adoption of the material in the industry.
Conclusion
The story of Gloster Saro Ltd.’s aluminium tanks is a testament to the innovative spirit and collaborative efforts that defined mid-20th-century maritime engineering. Suffolk Iron Foundry’s support, particularly in providing the crucial SIFMIG aluminium filler wire, was instrumental in realizing this vision. By embracing new materials and technologies, companies like Gloster Saro Ltd. and SIF not only advanced their own capabilities but also set new standards for the industry.
As we reflect on this historical achievement, it is clear that the combined efforts of pioneering companies and expert suppliers have paved the way for modern advancements in maritime technology. The legacy of projects like these continues to inspire innovation and progress in the industry today.