Introduction
The mid-20th century was a period of remarkable industrial growth and innovation. Companies across various sectors sought to push the boundaries of what was possible, striving for greater efficiency and effectiveness in their operations. One such company was Yorkshire Engineering Co. Ltd. of Bradford, Yorkshire. Founded in 1949, Yorkshire Engineering quickly established itself as a leader in the manufacture of large road tankers. This case study explores how the Suffolk Iron Foundry (SIF), established in 1925, played a pivotal role in supporting Yorkshire Engineering through their pioneering use of aluminum in tanker construction.
The Challenge
As the demand for road tankers surged in the post-war years, Yorkshire Engineering faced the challenge of increasing payload capacity while maintaining structural integrity and durability. Traditional steel tanks, though robust, were heavy and limited the payload that each tanker could carry. The company needed a solution that would reduce the weight of the tankers without compromising on strength and safety.
The SIF Solution
Enter SIF, renowned for their expertise in welding technology and materials. Recognizing the potential of aluminum as a lighter alternative to steel, Yorkshire Engineering collaborated with SIF to integrate advanced welding techniques into their manufacturing process. SIF’s Sifalumin No. 14 filler rods and SIFMIG aluminum wire became the cornerstones of this transformation.
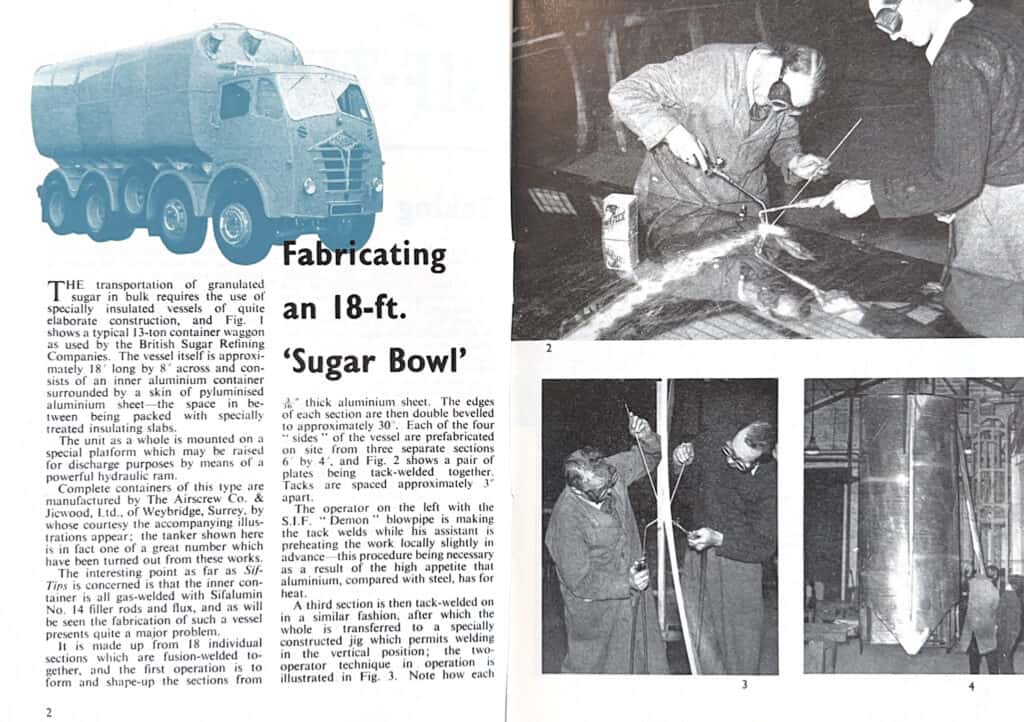
Implementation and Innovations
The transition to aluminum fabrication was no small feat. Yorkshire Engineering’s fabrication shop became a hive of activity, focusing on the construction of the new, lighter tankers. Each tanker, with a capacity of up to 6,000 gallons, required meticulous welding to ensure that every seam and joint was perfectly sealed.
Bill Bailes, General Sales Manager of Yorkshire Engineering, highlighted the advantages of using aluminum: “Although many tanks are still made of steel, aluminum now accounts for more than half the production. This is because they are considerably lighter than their steel counterparts, saving up to one ton in weight and allowing the completed tanker to carry about 250 more gallons.”
The collaboration with SIF was crucial in achieving these results. Stanley Newton, the shop foreman, explained, “SIFMIG aluminum wire, which we have been using for about a year, has proved to be the best material, giving faster and better welds.” The use of argon gas as a shield during welding further enhanced the quality and durability of the tanks.
Historical Impact
This innovative approach had a significant impact on both companies. For Yorkshire Engineering, the ability to produce lighter, more efficient tankers set them apart in the industry. The completed tankers, each costing up to £12,000, were in high demand and operated for at least 22 hours per day, underscoring their reliability and efficiency.
For SIF, this collaboration reinforced their reputation as leaders in welding technology. Founded in 1925, SIF had a long history of supporting industrial advancements, and their work with Yorkshire Engineering exemplified their commitment to innovation and excellence.
Conclusion
The partnership between Yorkshire Engineering and SIF is a shining example of how collaboration and technological innovation can drive industry forward. By embracing aluminum and leveraging SIF’s welding expertise, Yorkshire Engineering was able to produce tankers that not only met but exceeded the demands of the time. This case study serves as a testament to the enduring legacy of both companies and their contributions to industrial progress.
The story of Yorkshire Engineering and SIF is one of vision, innovation, and the relentless pursuit of excellence—a narrative that continues to inspire and inform the industry today.