Introduction
In the 1960s, as industries across the globe were rapidly modernizing, a silent revolution was underway in the field of welding. This revolution was led by Kerry’s (Ultrasonics) Ltd., a London-based company specializing in ultrasonic welding. At the heart of this innovation was the Suffolk Iron Foundry (SIF), founded in 1925, whose expertise and technological advancements played a crucial role in bringing ultrasonic welding to the forefront of industrial processes.
The Challenge
Traditional welding methods, which relied heavily on heat, posed several challenges. The intense heat required for fusion welding could damage sensitive components, especially in precision industries such as electronics and microcircuitry. Additionally, welding dissimilar metals and very thin materials presented significant difficulties. Industries needed a solution that could provide strong, reliable welds without the drawbacks of conventional welding techniques.
The Ultrasonic Solution
Ultrasonic welding emerged as a game-changer. This process uses high-frequency vibrations combined with pressure to create solid-state welds without external heat. The vibrations produce shear waves at the interface of the materials, resulting in a weld stronger than the base materials. This technique was particularly effective for welding soft non-ferrous metals like aluminum and for joining dissimilar metals.
The Role of SIF
SIF’s involvement was pivotal in refining and advancing ultrasonic welding technology. Known for their expertise in welding materials and techniques, SIF collaborated with Kerry’s (Ultrasonics) Ltd. to enhance the equipment and processes used in ultrasonic welding. Their contributions included developing specialized ultrasonic wire bonders and improving the welding apparatus to handle various industrial applications, from microcircuits to larger structural components.
Implementation and Innovations
Kerry’s (Ultrasonics) Ltd., with SIF’s support, introduced ultrasonic welding equipment that could handle the smallest jointing applications. This equipment was ideal for assembling transistors and microcircuit devices, where precision and reliability were paramount. The ability to use aluminum lead wires instead of gold significantly reduced costs while maintaining high performance.
On the heavier side, SIF’s advancements allowed ultrasonic welding to tackle more robust tasks. Using powerful 20 kW machines, the technology could weld thicker materials and larger areas, making it suitable for a wide range of industrial applications. For instance, a 0.2 in² (1.3 cm²) weld in mild steel could be achieved with a thickness limit of 0.04 in (1 mm), while the same area weld in aluminum could handle up to ⅛ in (3.1 mm).
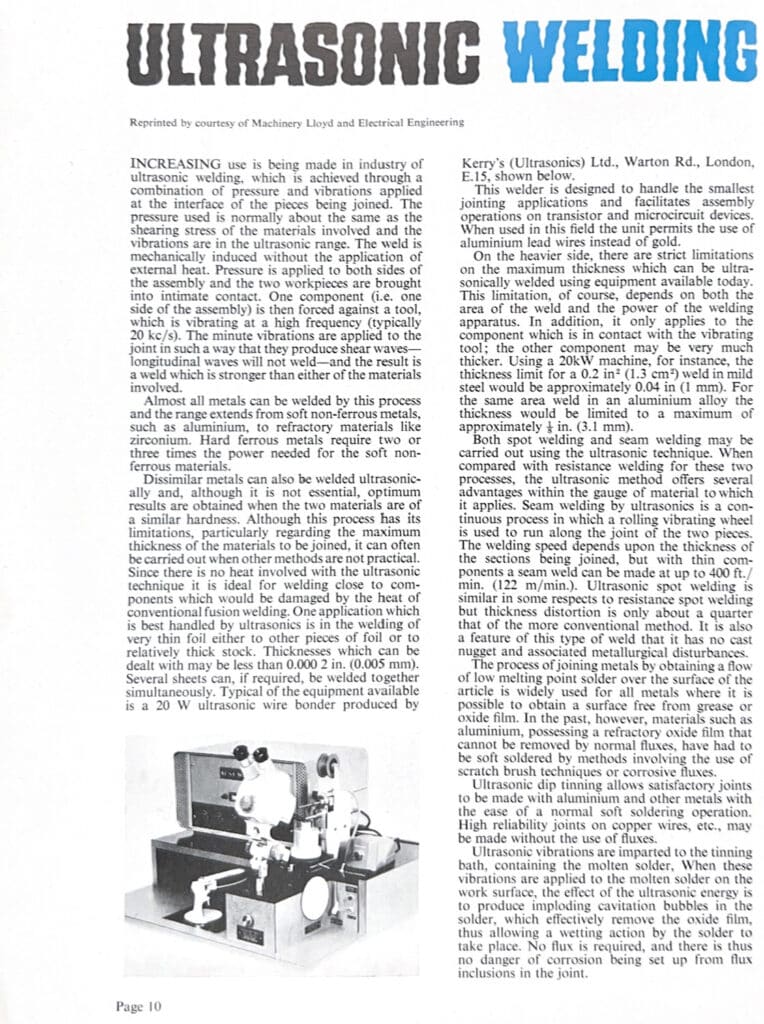
Spot and Seam Welding
Both spot and seam welding processes benefited from ultrasonic technology. Unlike traditional resistance welding, ultrasonic welding offered minimal distortion and no cast nugget, resulting in cleaner, more precise welds. Seam welding, in particular, used a rolling vibrating wheel to create continuous welds at speeds up to 400 ft./min. (122 m/min.), far surpassing the capabilities of conventional methods.
Ultrasonic Dip Tinning
Another breakthrough was ultrasonic dip tinning, which allowed for high-reliability joints without using flux. This process involved imparting ultrasonic vibrations to the tinning bath, removing oxide films from the work surface and enabling effective soldering. This innovation was especially valuable for aluminum and other metals that traditionally required aggressive fluxes for soldering.
Historical Impact
The partnership between SIF and Kerry’s (Ultrasonics) Ltd. marked a significant milestone in the evolution of welding technology. Industries that required precision and reliability, such as electronics, aerospace, and automotive, saw immediate benefits. The ability to weld delicate and dissimilar materials without heat opened new possibilities for design and manufacturing.
For SIF, this collaboration underscored their legacy of innovation and excellence in welding technology. Founded in 1925, SIF had long been a leader in developing advanced welding solutions, and their work with ultrasonic welding solidified their reputation as pioneers in the field.
Conclusion
The story of SIF and Kerry’s (Ultrasonics) Ltd. is a testament to the power of innovation and collaboration. By pushing the boundaries of what was possible with welding technology, they not only addressed the immediate needs of their time but also laid the groundwork for future advancements. This historical partnership serves as an inspiring example of how ingenuity and teamwork can drive progress and create solutions that stand the test of time.
As industries continue to evolve, the legacy of SIF and Kerry’s (Ultrasonics) Ltd. lives on, reminding us of the silent revolution that transformed welding and set new standards for excellence in manufacturing.